Smallest membrane, 3 ohm:
All measurements are done at 30 cm distance, frequency sweep starting at 200Hz.
My 120x120 mm as reference (blue):
All measurements are done at 30 cm distance, frequency sweep starting at 200Hz.
My 120x120 mm as reference (blue):
Last edited:
Second membrane, 6 ohm. Seems as it is the same as the first one but with double lenght/height:
Really high distortion, did you get that as well båndsei or did I mess up this measurement?
I am also a little bit suprised over the lf response.
Really high distortion, did you get that as well båndsei or did I mess up this measurement?
I am also a little bit suprised over the lf response.
Third membrane, same height as the second one but a little wider pleats, 4 ohm:
These three membranes are 5 mm thick.
Compared to mine, they have less "lf but more hf".
Same +6 dB/octave though.
Looking at the distortion, I think number 2 and 3 are too long compared to the pleat width. Do you agree, båndsei?
These three membranes are 5 mm thick.
Compared to mine, they have less "lf but more hf".
Same +6 dB/octave though.
Looking at the distortion, I think number 2 and 3 are too long compared to the pleat width. Do you agree, båndsei?
Forth membrane. Same pleat width but membrane is 6,5 mm thick. 4,3 ohm:
Now it gets interesting:
Great lf and hf response and really lower distortion.
With a wave guide in front of this one...
Now it gets interesting:
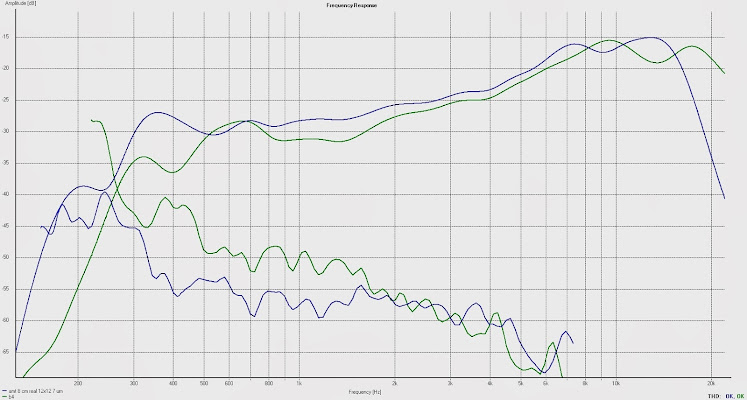
Great lf and hf response and really lower distortion.
With a wave guide in front of this one...
Last one. Membrane is 6,5 mm thick but now the pleat width is 1,5 mm (I think the first two were less 1 mm and the third and fourth 1 mm). 4,1 ohm:
Good frequency response but high distortion.
Well that´s it. Do you want me to re-do some measurements, båndsei?
Some reflections: All båndsei´s membranes have a good hf response but only the fourth had a resonable lf response together with low distortion.
So I should test with narrower pleats and not wider.
Any more thoughts?

Good frequency response but high distortion.
Well that´s it. Do you want me to re-do some measurements, båndsei?
Some reflections: All båndsei´s membranes have a good hf response but only the fourth had a resonable lf response together with low distortion.
So I should test with narrower pleats and not wider.
Any more thoughts?
Again, thanks båndsei/Bernt for this treat.
You are really the
of AMTs.
Great way of learning things.
I will now listen to the fourth membrane...
You are really the

Great way of learning things.
I will now listen to the fourth membrane...
Sounds great
.
Still some vibration though, but far less than from my membranes.
Hmm, now I have a lot to think about...

Still some vibration though, but far less than from my membranes.
Hmm, now I have a lot to think about...
Combing?
Did a quick with my membrane and narrowed the effective area from 120 mm to 30 mm too see if the low hf response was due to combing.
No, it wasn´t. But the lf went up 100 Hz.
I guess to get better hf response the pleats has to be less apart than my 2 mm.
1,5 mm is a good start.
Did a quick with my membrane and narrowed the effective area from 120 mm to 30 mm too see if the low hf response was due to combing.
No, it wasn´t. But the lf went up 100 Hz.
I guess to get better hf response the pleats has to be less apart than my 2 mm.
1,5 mm is a good start.
Just a wild idea:
Would it be totally impossible to find an open-cell reticulated foam with very compliant characteristics, have it cut into slightly V-shaped strips and then fit them into the pleats?
Or maybe even use a full sheet of thin foam (like the "baby-wipes" or washboard type sheets, available here in Sweden) and then glue the full membrane? Not the entire area of course, I mean laying the folded membrane down on to a flat piece of foam, bonding only the tips of the pleat ridges.
Wouldn't that stop the buzzing?
Would it be totally impossible to find an open-cell reticulated foam with very compliant characteristics, have it cut into slightly V-shaped strips and then fit them into the pleats?
Or maybe even use a full sheet of thin foam (like the "baby-wipes" or washboard type sheets, available here in Sweden) and then glue the full membrane? Not the entire area of course, I mean laying the folded membrane down on to a flat piece of foam, bonding only the tips of the pleat ridges.
Wouldn't that stop the buzzing?
First idea sounds (sorry) good. I´ve been trying to get the right material for such a suspension of the ends. Problem is that I want it firm in one direction (forward/backward) so it will hold the membrane centered in the gap but soft enough it the up/down direction in order not to couple the membrane to its frame. Perhaps some sort of filament structure or small springs.
I don´t think the second idea will get rid of the buzz, the energy is too high on these resonance frequencies. I´ve tested with a piece of cloth between the membrane and the grid, no improvement.
What I really need in to come up with a test rigg where ideas could be evaluated quickly.
I don´t think the second idea will get rid of the buzz, the energy is too high on these resonance frequencies. I´ve tested with a piece of cloth between the membrane and the grid, no improvement.
What I really need in to come up with a test rigg where ideas could be evaluated quickly.
The second one looks strange to me.
I don`t remember all my models,but I made one with small traces and it might be this one.It had much distortion.
I think you are right regarding Width of pleats. 1-1.5mm.And maybe 60-70mm Width of diaphragm.
I glue ends with silicone .
I see you use frames now.It might be easier to make the frame same hight as the "motor"
Good luck
Bernt
I don`t remember all my models,but I made one with small traces and it might be this one.It had much distortion.
I think you are right regarding Width of pleats. 1-1.5mm.And maybe 60-70mm Width of diaphragm.
I glue ends with silicone .
I see you use frames now.It might be easier to make the frame same hight as the "motor"
Good luck
Bernt
Thanks for your advice, Bernt.
The problem with 1 or 1,5 mm width is that it is hard to get rigid enough rods for the folding tool. Do you have any suggestions?
Your frames are very good, I shall see if I can incorporate any of it in my frames.
I´ll share here when I´m done.
Silicone is good, problem is that it takes too long for my patience to cure.
Or are you using a two component silicone?
I´ll make a 60 mm wide membrane with 1,5 mm wide pleats, it would still fit in the motor, but I think that I´ll stick with having the horisontal strips outside.
The problem with 1 or 1,5 mm width is that it is hard to get rigid enough rods for the folding tool. Do you have any suggestions?
Your frames are very good, I shall see if I can incorporate any of it in my frames.
I´ll share here when I´m done.
Silicone is good, problem is that it takes too long for my patience to cure.
Or are you using a two component silicone?
I´ll make a 60 mm wide membrane with 1,5 mm wide pleats, it would still fit in the motor, but I think that I´ll stick with having the horisontal strips outside.
Take a look at these Horns for TPL 150:Beyma TPL 150 - horn trials
I use one component silicone and patience.
Bernt
I use one component silicone and patience.
Bernt
Thanks for the link, those horns look really nice.
Something like that, it is really more of a wave guide, is brewing in my work shop. First try will be in XPS. They will 70 cm wide/high.
BTW, strange to see the same dip in hf response as my membranes.
I will try to get the rods from a local supplier; cutting out 15 mm wide strips from a 1,5 mm steel or aluminium sheet shouldn´t take that long/cost much.
Especially when I can do the un-critical cuts into 200 mm long rods myself.
I will use this two component silicone rubber.
Something like that, it is really more of a wave guide, is brewing in my work shop. First try will be in XPS. They will 70 cm wide/high.
BTW, strange to see the same dip in hf response as my membranes.
I will try to get the rods from a local supplier; cutting out 15 mm wide strips from a 1,5 mm steel or aluminium sheet shouldn´t take that long/cost much.
Especially when I can do the un-critical cuts into 200 mm long rods myself.
I will use this two component silicone rubber.
Last edited:
Guiding the waves
The first serious attempt at a wave guide:
Frequency response and THD @ 2,2 meters:
The first serious attempt at a wave guide:
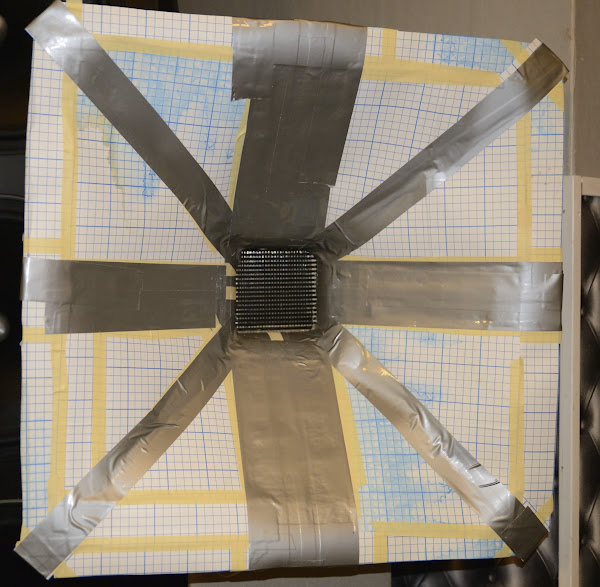
Frequency response and THD @ 2,2 meters:
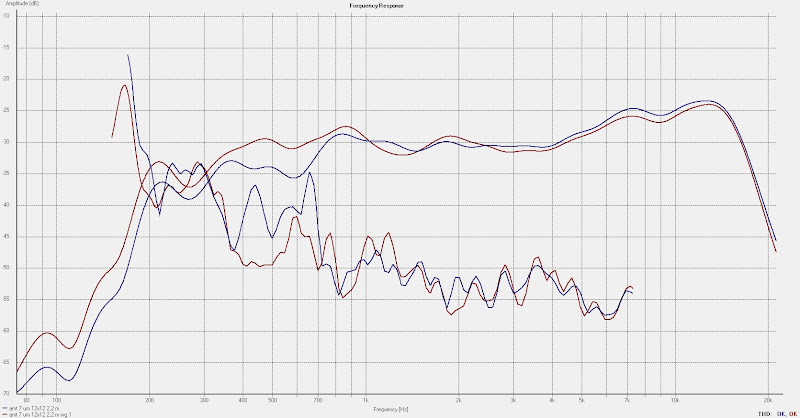
Or maybe even use a full sheet of thin foam (like the "baby-wipes" or washboard type sheets, available here in Sweden) and then glue the full membrane? Not the entire area of course, I mean laying the folded membrane down on to a flat piece of foam, bonding only the tips of the pleat ridges.
Wouldn't that stop the buzzing?
This kind of non-woven cloth?
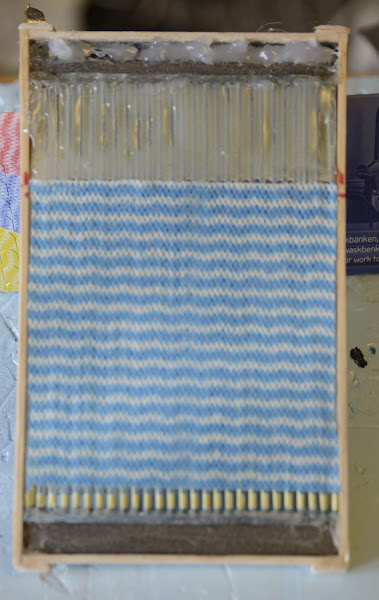
This is how it measured on 7 um membrane (cloth):
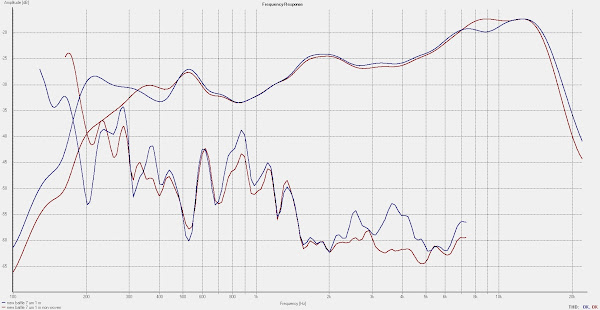
And on a 10 um membrane (cloth):
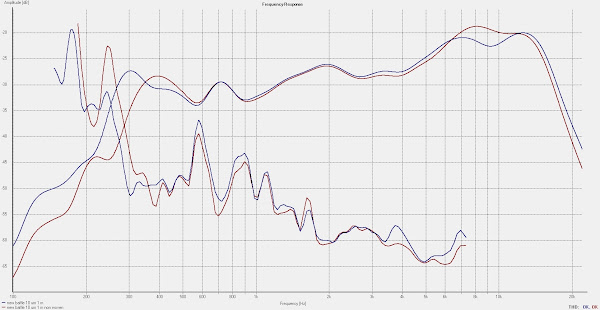
Conclusion: Lower THD in general, lower SPL in the lf area. And..
Yes, the vibrations/buzz is much less

Thank you, theSuede
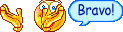
Thanks for your advice, Bernt.
I´ll make a 60 mm wide membrane with 1,5 mm wide pleats, it would still fit in the motor, but I think that I´ll stick with having the horisontal strips outside.
Well, that didn´t turn out well. Apart from being very hard to make (I actually made it full size, 120 mm), the membrane showed exactly the same frequency response as the other 2 mm wide pleat ones.
Next try will be with a little less mass, that is narrower alu-strips.
Folding will be the old 8/2 mm but the alu/space ratio will be 5/5 mm.
I´ll be using 10 um alu on paper.
Actually something good happened, but in the lf (blue fold 8,5/1,5 alu 7/3 ; red fold 8/2, alu 7/3):
Little high distortion around 270 Hz. Perhaps the remedy is a larger baffle/wave guide.
If a alu 5/5 membrane cures the low hf response, perhaps a membrane with a fold ratio of 8,5/1,5 and alu 5/5 is the solution.

Little high distortion around 270 Hz. Perhaps the remedy is a larger baffle/wave guide.
If a alu 5/5 membrane cures the low hf response, perhaps a membrane with a fold ratio of 8,5/1,5 and alu 5/5 is the solution.
The felt is dampening the unwanted vibrations but not enough.
It is the fastening of the membrane on the sides that are the main problem.
The first and last pleats doesn´t adhere to the motor enough.
If I could get some glue between the iron rods the vibrations will probably get away.
I removed the felt and the plastic back from my Beyma TPL-150 and now run it dipole. It is possible I lost some midrange depth doing this, but it was worth it. StigErik says the TPL-150 is bad at dipole because of its size, and that I should try the smaller Mundorf if I want to run it dipole. There might be some resonanses, but I have not measured it yet. He suggested to get a big baffle for it.
So since your speaker is much larger, maybe you should try a large baffle around it.
This kind of non-woven cloth?
![]()
This is how it measured on 7 um membrane (cloth):
![]()
And on a 10 um membrane (cloth):
![]()
Conclusion: Lower THD in general, lower SPL in the lf area. And..
Yes, the vibrations/buzz is much less.
Thank you, theSuedeAn externally hosted image should be here but it was not working when we last tested it.
What would happen with 2um alu foil? I have a lot of leftovers from a ribbon mic project. Impossible to handle though. The foil with a pealable paperback would save me a weekend of swearing.
Last edited:
- Status
- Not open for further replies.
- Home
- Loudspeakers
- Planars & Exotics
- Yet another DIY AMT