I was hoping since all the ribbons are moving in sync in a strong magnetic field with no corrugation there would be no mechanical waves.AND the "motor" (the arms) are will be sending mechanical waves into the center from all directions where they will meet and ether cancel or add likely resulting in a ragged freq. response.
I was planning on using a tiny bit of slack in the tautness to allow it to move.
I was thinking the magnetic field would have enough horizontal hold along the ribbon under these circumstances to prevent flapping and thus prevent mechanical waves?
Maybe it needs some sort of springy suspension on the edges instead of slack or corrugation to avoid this?
I was thinking about suspension for a while actually. My idea was to sandwich the ribbon between two thin sheets of rubber and then sandwich the rubber between two sheets of spongy material. That way the rubber damps mechanical vibrations and the sponge allows the ribbon to move without corrugation.
What do you think?
I'm not sure what kind of sponge I would use. Maybe instead of sponges and rubber i could use a solid slab of "ninjaflex" the 3D printing material. That stuff's pretty bouncy.
I have developed a few ribbon "suspension" systems. The largest issue IMO is mass. No matter how flexy the suspension, if its mass is not very close to the ribbons mass then it looks like a termination and will reflect energy back into ribbon. AND just because you have a suspension to take up slak it will have very little if any effect at mid frequencys and the ribbon will behave basically the same as no suspension within its peak operating range of motion. There will always be "waves" to deal with 
In the end I incorporated a suspension in one design mostly just to avoid a changing Fs with excursion. This ribbon is a smallish (6-7) inch ribbon that is used to 500 hz. Without the suspension there can be a hump in response right about at the 500 hz crossover point and the suspension makes it easy for production to assemble and get it right. This ribbon is fairly stiff ( but not quite) in the long direction similar to a flat uncorrugated ribbon.
A good ribbon suspension to look at is the Celestion ribbon that I think Grahm Bank designed. Foam and silicone tape. I suspect however this suspension is not so much to move up and down much but sinply to keep good tension on ribbon. Smaller shorter ribbons may need a suspension that moves more easily and here mass will be a factor.
The bigger problem with a truly "FLAT" ribbon is that there not perfectly flat. This means you have what some call the "oil can resonance" problem. In other words the diaphragm has little warps/bends that can "oil can" and make noise. They can be very resonant at certain freqs. SO what some are doing is embossing the foil with a pattern of some kind. Good example are the RAALs. This basically quiets the diaphragm and in my experience just about any embossing will work. It may not look great but it will quiet things down. Heck even just crinkling the foil up recklessly then flattening it out will work BUT it wont be very reliable. Trick is to find a pattern and method that quiets and doesn't crack.
In the end I incorporated a suspension in one design mostly just to avoid a changing Fs with excursion. This ribbon is a smallish (6-7) inch ribbon that is used to 500 hz. Without the suspension there can be a hump in response right about at the 500 hz crossover point and the suspension makes it easy for production to assemble and get it right. This ribbon is fairly stiff ( but not quite) in the long direction similar to a flat uncorrugated ribbon.
A good ribbon suspension to look at is the Celestion ribbon that I think Grahm Bank designed. Foam and silicone tape. I suspect however this suspension is not so much to move up and down much but sinply to keep good tension on ribbon. Smaller shorter ribbons may need a suspension that moves more easily and here mass will be a factor.
The bigger problem with a truly "FLAT" ribbon is that there not perfectly flat. This means you have what some call the "oil can resonance" problem. In other words the diaphragm has little warps/bends that can "oil can" and make noise. They can be very resonant at certain freqs. SO what some are doing is embossing the foil with a pattern of some kind. Good example are the RAALs. This basically quiets the diaphragm and in my experience just about any embossing will work. It may not look great but it will quiet things down. Heck even just crinkling the foil up recklessly then flattening it out will work BUT it wont be very reliable. Trick is to find a pattern and method that quiets and doesn't crack.
That's why I was going to sandwich a solid rubber layer in the middle to absorb vibrations and a flexy outer layer to allow for the actual movement. That's a double layer shock absorber. with opposing consistencies. That's still not enough?The largest issue IMO is mass. No matter how flexy the suspension, if its mass is not very close to the ribbons mass then it looks like a termination and will reflect energy back into ribbon.
Surely there's a point where the vibration dampening and flexibility makes up for the mass.
Last edited:
That's why I was going to sandwich a solid rubber layer in the middle to absorb vibrations and a flexy outer layer to allow for the actual movement. That's a double layer shock absorber. with opposing consistencies. That's still not enough?
Surely there's a point where the vibration dampening and flexibility makes up for the mass.
not sure your construction. need a drawing
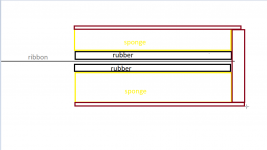
Replace "sponge" with any bouncy flexy springy thing.
Rubber should do a pretty good job absorbing vibrational energy and any untransfered energy would go into the "sponge" material as it moves.
I think the contrast of hard rubber and squishy springy material would do a huge number on absorbing vibrational energy that either of them could not do alone.
Last edited:
Hmm well maybe.
I would get rid of the heavy rubber, use about a 2 lb density urathane foam where your sponge is, and constrain the urathane only over 1/2 the distance you now have(the red lines). This to make a better "impedance match" between ribbon and damper, and by moving the constraint (red lines) back a bit we create a sort of lossy transmission line termination. Maybe even stagger the ends of the urathane foam (one piece extends farther out on ribbon than other.
In the end I find most "suspensions" to be ineffective at ribbon damping unless the suspension / termination is very long and very graded. By the time its trully absorbing enough to make a measurable difference the whole thing ends up very long and theres a lot of wasted energy in the ribbon under the foam. This is an issue for smaller ribbons.
Most if not all of my suspension designs have two functions. 1- keeping ribbon tight. 2- providing a strain relief to avoid ribbon cracking at the clamp.
I would get rid of the heavy rubber, use about a 2 lb density urathane foam where your sponge is, and constrain the urathane only over 1/2 the distance you now have(the red lines). This to make a better "impedance match" between ribbon and damper, and by moving the constraint (red lines) back a bit we create a sort of lossy transmission line termination. Maybe even stagger the ends of the urathane foam (one piece extends farther out on ribbon than other.
In the end I find most "suspensions" to be ineffective at ribbon damping unless the suspension / termination is very long and very graded. By the time its trully absorbing enough to make a measurable difference the whole thing ends up very long and theres a lot of wasted energy in the ribbon under the foam. This is an issue for smaller ribbons.
Most if not all of my suspension designs have two functions. 1- keeping ribbon tight. 2- providing a strain relief to avoid ribbon cracking at the clamp.
I'm having a difficult time understanding your description.
You mean like this?
Well the concept of the rubber would be to absorb most of the initial "shock" energy as the ribbon moves up or down, and then the remaining energy would go into actually moving the ribbon through the "sponge" leaving nothing left to reflect back into the ribbon. At least that's how I see it in my head.
You mean like this?
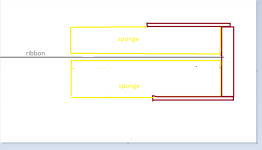
I don't understand. What does this mean in mechanical terms?This to make a better "impedance match" between ribbon and damper,
I would get rid of the heavy rubber
Well the concept of the rubber would be to absorb most of the initial "shock" energy as the ribbon moves up or down, and then the remaining energy would go into actually moving the ribbon through the "sponge" leaving nothing left to reflect back into the ribbon. At least that's how I see it in my head.
yes just like that.
I would do a little reading on mechanical impedance . Sorry dont have a good link for ya but I will give it a crude shot...
to maximize energy transfer you want the mechanical impedance's to match. An example is a baseball and a bat. Say the baseball is a standard base ball and the bat is not a standard bat but one of those hollow plastic light weight bats. You can swing as hard as u want but there is such a mismatch between bat and ball that you just cannot transfer the energy of your swing into the ball. Now use the heavy wood bat and you got a much better match between bat and ball.
Another example is damping matt used on car sheet metal to quiet the interior. Yes the matt has a damping effect ( look up mechanical hysteresis) BUT you have to put a matt on there that is close to same mass as the steel or it will not be very effective.
So anyway mass matching to some extent has something to do with it. In your case the rubber may work ok if it was thin and light enough but the urethane foam has proven to work better in my experience with arraignments like you have there.
I would do a little reading on mechanical impedance . Sorry dont have a good link for ya but I will give it a crude shot...
to maximize energy transfer you want the mechanical impedance's to match. An example is a baseball and a bat. Say the baseball is a standard base ball and the bat is not a standard bat but one of those hollow plastic light weight bats. You can swing as hard as u want but there is such a mismatch between bat and ball that you just cannot transfer the energy of your swing into the ball. Now use the heavy wood bat and you got a much better match between bat and ball.
Another example is damping matt used on car sheet metal to quiet the interior. Yes the matt has a damping effect ( look up mechanical hysteresis) BUT you have to put a matt on there that is close to same mass as the steel or it will not be very effective.
So anyway mass matching to some extent has something to do with it. In your case the rubber may work ok if it was thin and light enough but the urethane foam has proven to work better in my experience with arraignments like you have there.
I'm thinking about what you said here
and drawing a parallel to my version
If I were to do the same to mine it would end up like this
So if we draw the same parallel to yours
it would make sense that you said your method must be long in order to function well because there is no hard structure to dissipate the energy, so it must be long to compensate.
The more flexible the front end is the less energy gets transfered into the suspension structure. The less flexible it is the more energy gets transfered into the suspension structure. That is where the advantage of my version lies, in that is it both flexible and inflexible inside the structure so we get the advantages of both worlds.
I think if you used a more sensitive suspension it would counteract the need for an elongated suspension. My version requires the suspension to be inside the entire structure by conceptual design in order to maximize energy transfer into the suspension.
At least this is the way it plays in my head.
I'm not saying my version is better than yours or anything, I'm just spitting out my thoughts.
The more I think about my balloon idea the more I'm starting to like it.
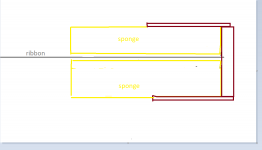
and drawing a parallel to my version
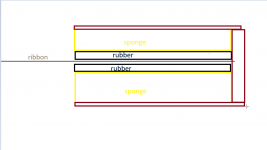
If I were to do the same to mine it would end up like this
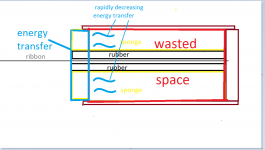
So if we draw the same parallel to yours
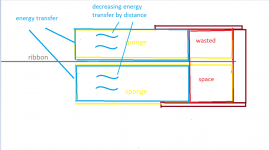
it would make sense that you said your method must be long in order to function well because there is no hard structure to dissipate the energy, so it must be long to compensate.
The more flexible the front end is the less energy gets transfered into the suspension structure. The less flexible it is the more energy gets transfered into the suspension structure. That is where the advantage of my version lies, in that is it both flexible and inflexible inside the structure so we get the advantages of both worlds.
I think if you used a more sensitive suspension it would counteract the need for an elongated suspension. My version requires the suspension to be inside the entire structure by conceptual design in order to maximize energy transfer into the suspension.
At least this is the way it plays in my head.
I'm not saying my version is better than yours or anything, I'm just spitting out my thoughts.
The more I think about my balloon idea the more I'm starting to like it.
Last edited:
I have another question for you, how did your ribbon headphone experiments go? How was the sound compared to other technologies?
I dont have much experience with other manufactures headphones so do not have a way to compare, but, I built both ribbon and planer headphones.
That said it always surprised me how good a pr of simple ribbons strapped to your head in the crudest fashion sounded. The ones I built were 1 inch wide ribbons about 2 inches long. No transformer, just put a series 4 ohm resistor on them and hook them straight up to the amp. The most transparent sound I have ever heard. Deep fast clean exciting dynamic etc etc...
The headphone built this way also gives another way to judge different ribbon designs. IMO its a very transparent method that allows you to more easily hear the subtle differences between different diaphragms.
I remember at one point working to reduce the metallic artifacts from the sound so I was comparing foil only ribbons and laminated plastic backed ribbons. Eventually I wanted a reference that minimized the contribution of metal to the sound so I took apart a metal film capacitor and use that film to make a ribbon. The film was around 3 micron polyester film with a vapor deposited coating of aluminum so thin you could see through it. The 1 inch wide by 2 inch long ribbon was 5 ohms! no resistor needed. It could not handle any power as it would simply heat up and melt, BUT, there was still enough volume for headphone. I was shocked by how different it sounded than all the other ribbons. Even quite different than the 4 micron foil only ribbon diaphragms similar to what Raven and RAAL uses. The capacitor diaphragm was truly an "immaterial" sound and the pulse response showed this.
I also built planer headphones. These to my ears did not sound quite as convincing as the free swing ribbon. IMO this is largely to do with two things..
1- the damn drum-skin resonances are very difficult to control in a small diaphragm. The bass was louder and more power than the smaller ribbon , BUT not as believable. In fact the best one for bass was a heavy diaphragm with NO tension at all. This compared well to the ribbon but played louder and had more bass dynamic.
2- the free swing ribbon is a truly "open" construction. No magnet structure behind the ribbon. No matter how you taylor the FR, any structure behind the diaphragm seems to impacts the sound making it "brighter" even when EQed to flat.
Eventually I used a film that doesn't have a high tensile strength like mylar. It was a stretch packaging film so it had much higher internal loss than mylar AND it was much stretcher so it didn't build resonances the way the mylar can when its stretched. This diaphragm sounded very close to the no tension Mylar versions in the bass and had a smoother mid range as well.
Last edited:
- Status
- This old topic is closed. If you want to reopen this topic, contact a moderator using the "Report Post" button.
- Home
- Loudspeakers
- Planars & Exotics
- Ribbon question