Hi I am new here so a introduction is necessary.
I am Helmuth.Lageschaar from de Netherlands.
I work as assistant at engineering department of a manufacturer from electronic ballast. I do stuff as UL approval and prototype building.
The start of my electronic career was triggered by my the hobby of my father and my fascination for audio equipment.
And then the focus on speakers and amplifiers. I often design virtual speakers when I got a idea. Now I have got a college how is interested in a quality speaker designed by me.
I want to post the evolution of this project.
His request was a bass reflex and attractive design by using aluminium cone speakers.
My goal to make the best possible design for a low budget price with professional appearance.
I started al ready but register on DIY today so here the design.
This drawing is already modified but good for to get a impression.
I am Helmuth.Lageschaar from de Netherlands.
I work as assistant at engineering department of a manufacturer from electronic ballast. I do stuff as UL approval and prototype building.
The start of my electronic career was triggered by my the hobby of my father and my fascination for audio equipment.
And then the focus on speakers and amplifiers. I often design virtual speakers when I got a idea. Now I have got a college how is interested in a quality speaker designed by me.
I want to post the evolution of this project.
His request was a bass reflex and attractive design by using aluminium cone speakers.
My goal to make the best possible design for a low budget price with professional appearance.
I started al ready but register on DIY today so here the design.

This drawing is already modified but good for to get a impression.
Seems ok...sure hope thats a 12" woofer 
btw, I would make a seperate room behind the mids to house the xo
As fore the matrix stucture in the midrange...much better to make round holes in the structure instead of squared holes
I reckon you are aware that MTM deappolito asks fore small mids and low xo point...theoretically
btw, I would make a seperate room behind the mids to house the xo
As fore the matrix stucture in the midrange...much better to make round holes in the structure instead of squared holes
I reckon you are aware that MTM deappolito asks fore small mids and low xo point...theoretically
http://www.audiocomponents.nl/speakers/scanspeak/reference/scanspeak-reference_eng.htm
See Maxima at the bottom. Not aluminium though, at least someone else has had the same idea.
http://www.audiocomponents.nl/speakers/scanspeak/reference/tekening/Maxima_1.htm
See Maxima at the bottom. Not aluminium though, at least someone else has had the same idea.
http://www.audiocomponents.nl/speakers/scanspeak/reference/tekening/Maxima_1.htm
@tinitus
I understand your comment (round holes). But with the wave length of the sub this is no point.
The tip for creating a room for de XO I will implement good idea.
It is a 10"woofer here the predicted response. -3dB 26Hz
The pipe will be place 15cm from the ground and there by lift the level round from 18-35Hz. So -3db would be a possibility when the prediction is correct.
Impedance and cone extrusion.
I have used core plywood. This is the most cost effective way to create a professional finish.
Because you don't have to paint.
The part were saw form one plate to maintain the wood structure.
See the line's in the wood.
Used glue red dry transparent the green one is super strong and foams up used inside the box.
To mount them perfect use tape.
Then turn the part 90 degrees and put on the red glue.
fold the part to gather to get a perfect fit use the back plane without glue to fix the 3 parts.
hold it with two clamps to dry.
I understand your comment (round holes). But with the wave length of the sub this is no point.
The tip for creating a room for de XO I will implement good idea.
It is a 10"woofer here the predicted response. -3dB 26Hz
An externally hosted image should be here but it was not working when we last tested it.
The pipe will be place 15cm from the ground and there by lift the level round from 18-35Hz. So -3db would be a possibility when the prediction is correct.
Impedance and cone extrusion.
An externally hosted image should be here but it was not working when we last tested it.
I have used core plywood. This is the most cost effective way to create a professional finish.
Because you don't have to paint.
The part were saw form one plate to maintain the wood structure.
An externally hosted image should be here but it was not working when we last tested it.
See the line's in the wood.
An externally hosted image should be here but it was not working when we last tested it.
Used glue red dry transparent the green one is super strong and foams up used inside the box.
An externally hosted image should be here but it was not working when we last tested it.
To mount them perfect use tape.
An externally hosted image should be here but it was not working when we last tested it.
Then turn the part 90 degrees and put on the red glue.
fold the part to gather to get a perfect fit use the back plane without glue to fix the 3 parts.
An externally hosted image should be here but it was not working when we last tested it.
hold it with two clamps to dry.
An externally hosted image should be here but it was not working when we last tested it.
I love your design, great professional quality work, it begs the question, Why are some of the X-over componants mounted outside the inclosure? Just curious. still very very nice.
I just noticed that may not be your work as I clicked the link just below your first post. Sorry about that
I just noticed that may not be your work as I clicked the link just below your first post. Sorry about that
dublin78 said:http://www.audiocomponents.nl/speakers/scanspeak/reference/scanspeak-reference_eng.htm
See Maxima at the bottom. Not aluminium though, at least someone else has had the same idea.
http://www.audiocomponents.nl/speakers/scanspeak/reference/tekening/Maxima_1.htm
This setup is not new see visaton vox visaton voxexist for about 10 year now. Price kit 1600euro.
I will make a same quality speaker for 700-1000 euro.
The example with active sub that you have posted will also be more expensive. Than the passive version I design. A good alternative for active layout is adding a Bi-wiring connector
Alcone drivers?
Alcone has great drivers and nice price.
But still more expensive then necessary and to early breakup around 5000Hz like almost al aluminium mid drivers.
The glue is dry
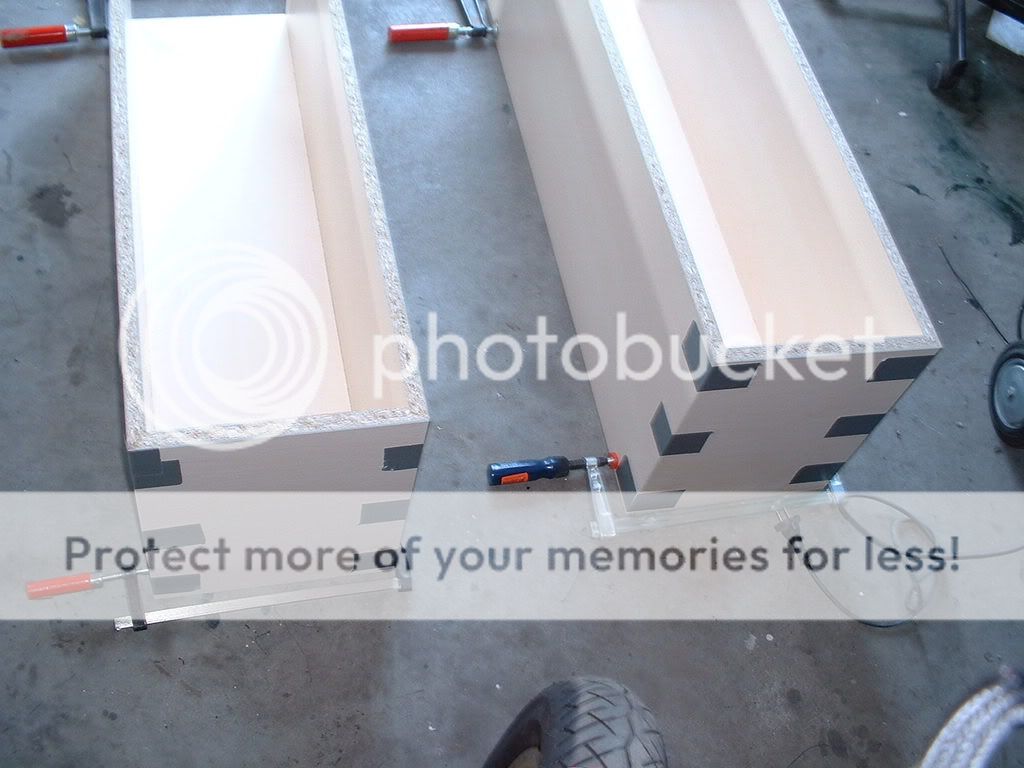
now I will glue the backplane. To get a good contact with the Formica first sand it.
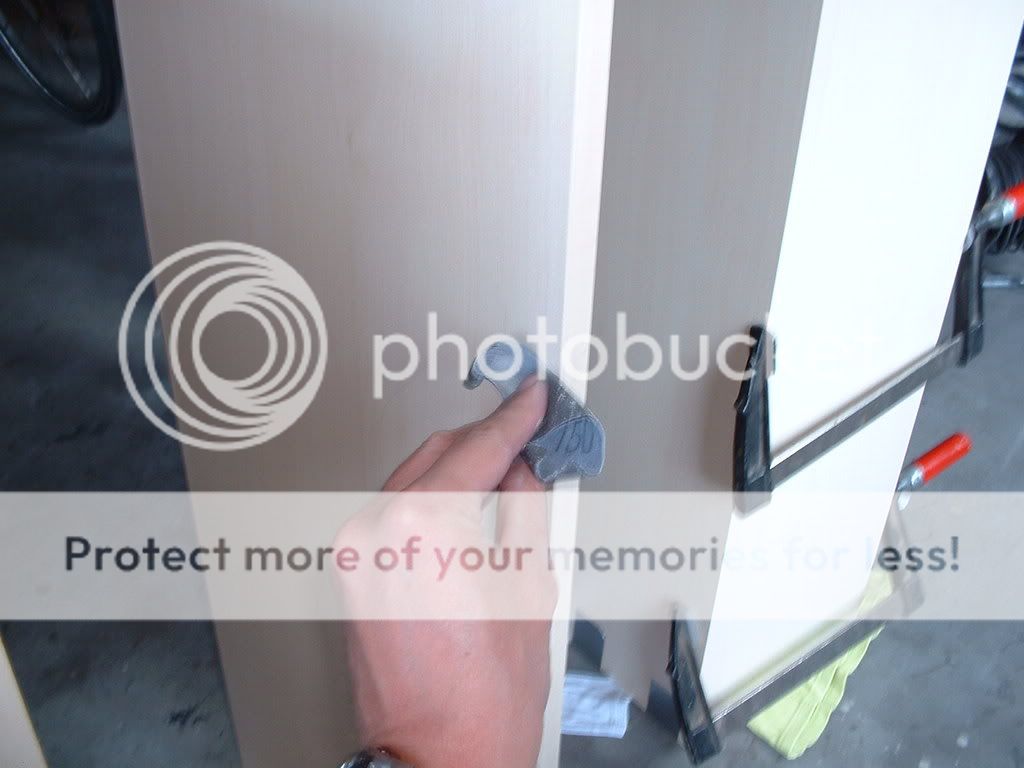
here you see the foam off the bizon construction gleu.
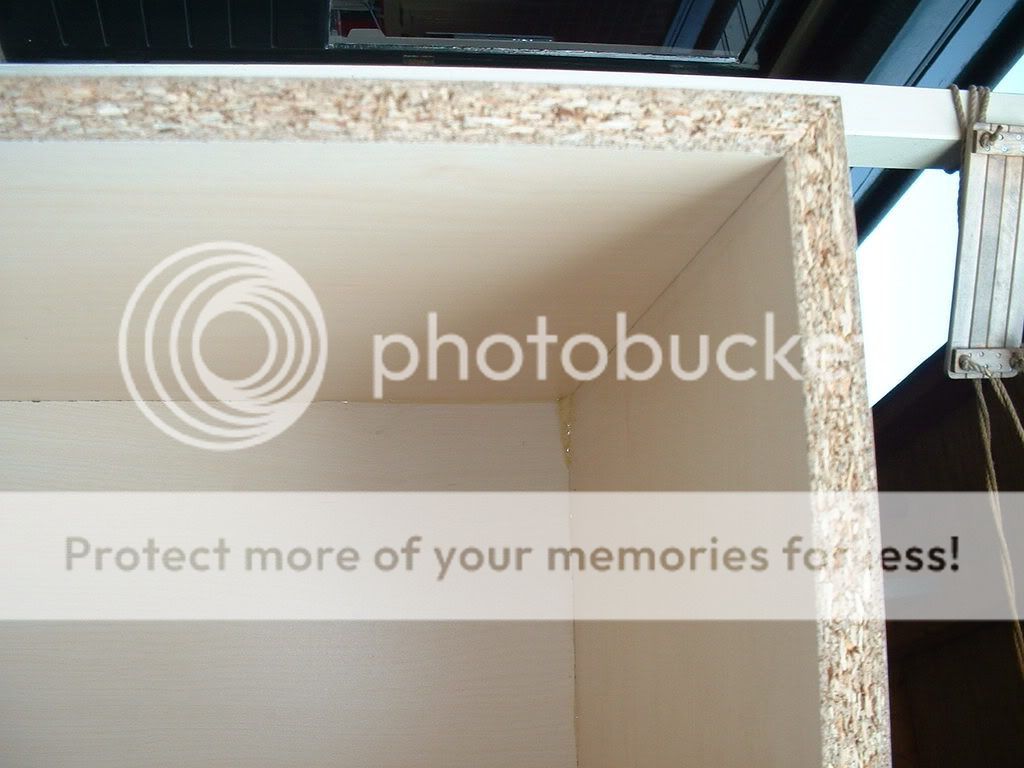
The excess glue can by scraped with a paint remover tool.
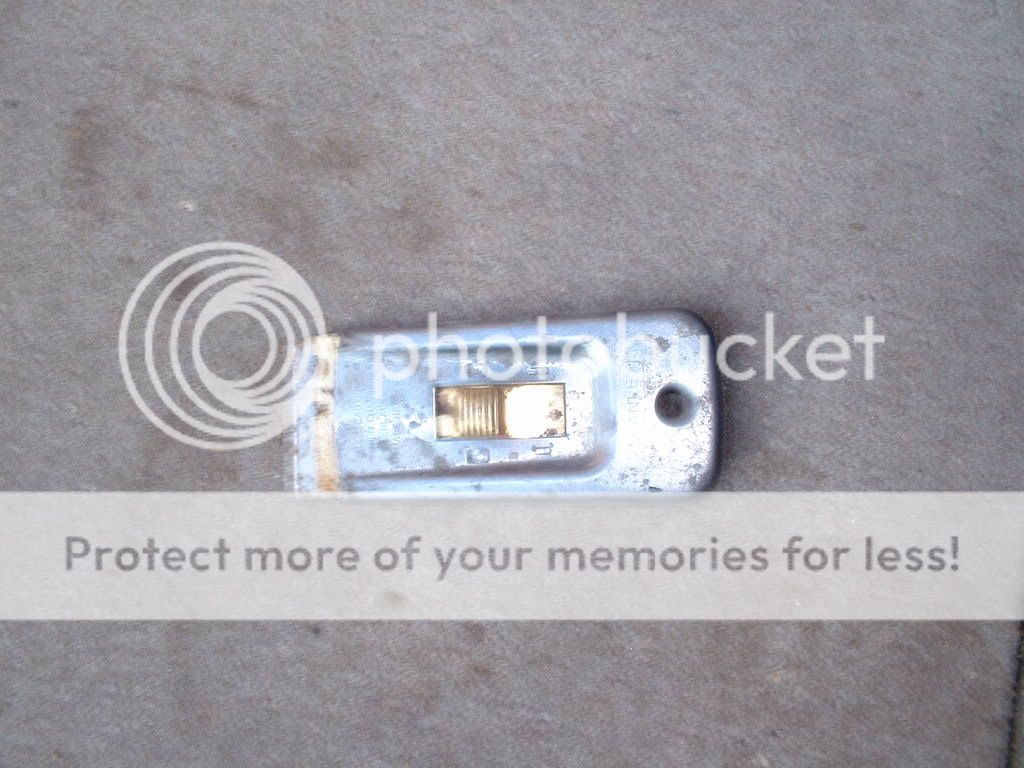
Dry result. This perfect finish can only be archived with care full sawing the parts. So look for a good hobby market with professional saw machine.
Then in two day's you have this result.
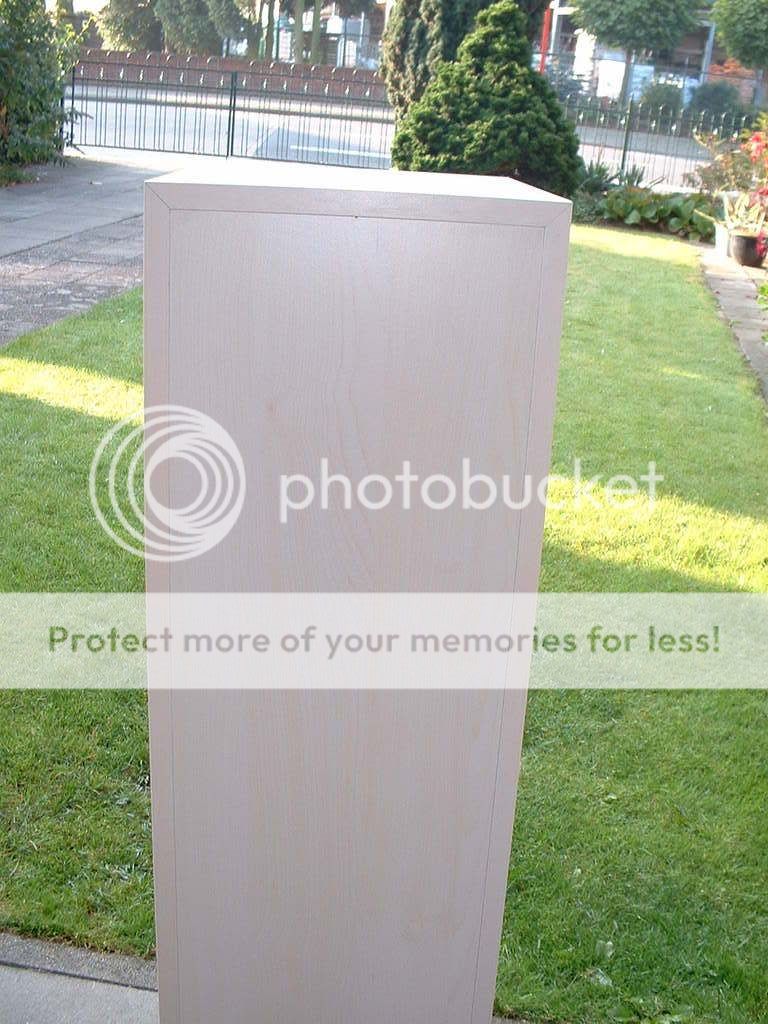
close look
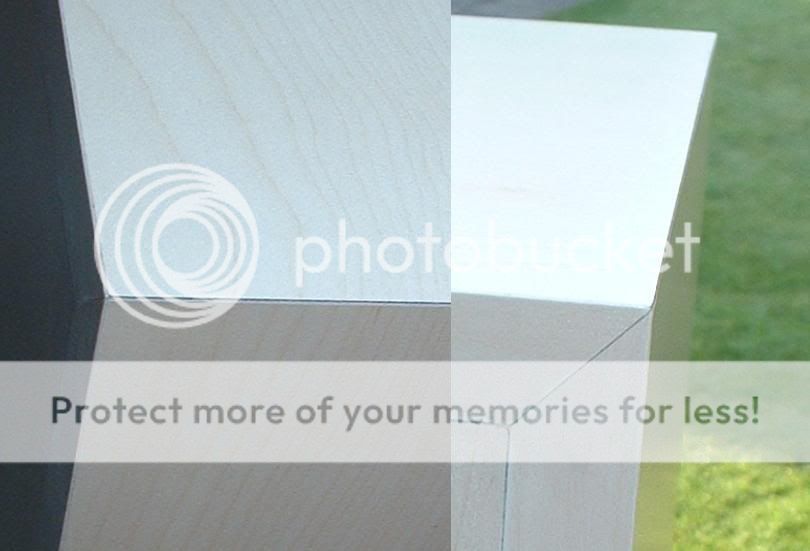
I love your design, great professional quality work, it begs the question, Why are some of the X-over componants mounted outside the inclosure? Just curious. still very very nice.
When you mount them outside the box it is easy to tweak the part great for hobby. Not useful for normal users.
Graetz Helmuth
man, that was fast
This is the result of the last two weeks so not this weekend
Now the bracing.
The parts are made out of 12mm MDF. This will form the bracing off the top part of the box.
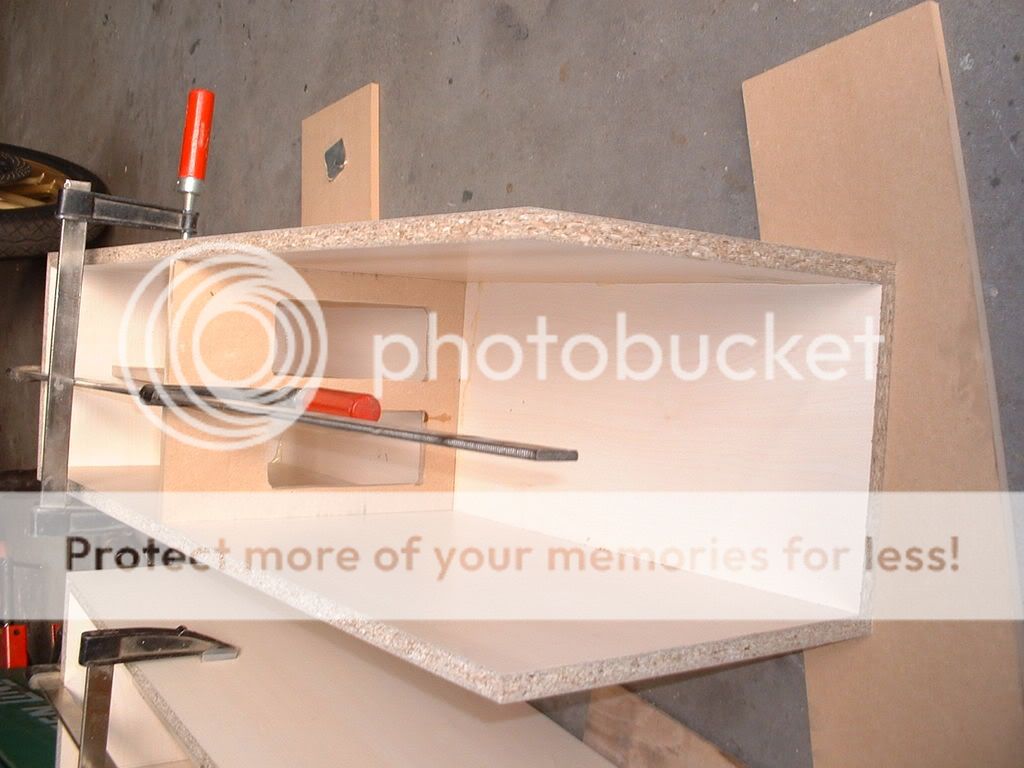
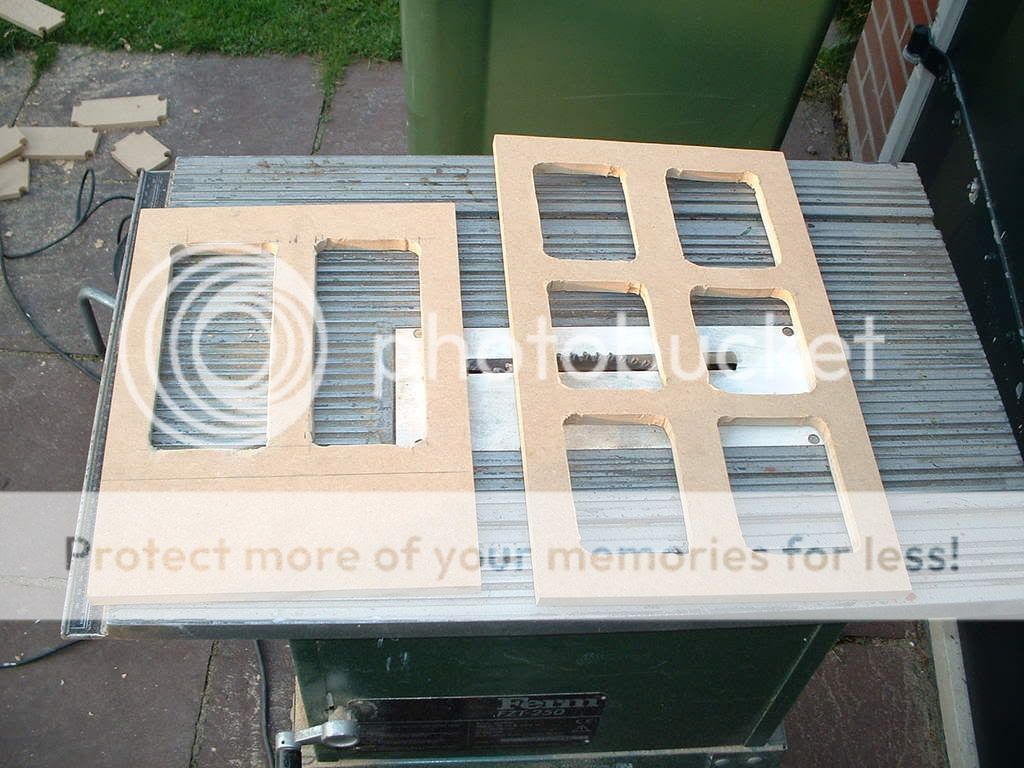
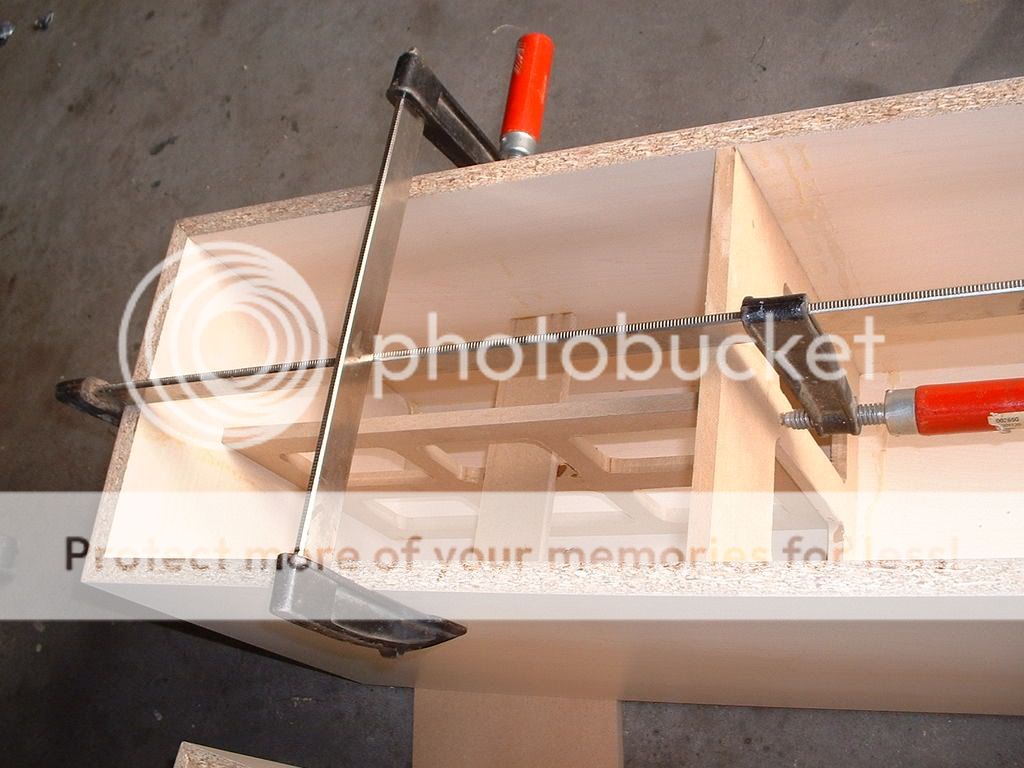
These excess strips are great for bracing the box behind the woofer.
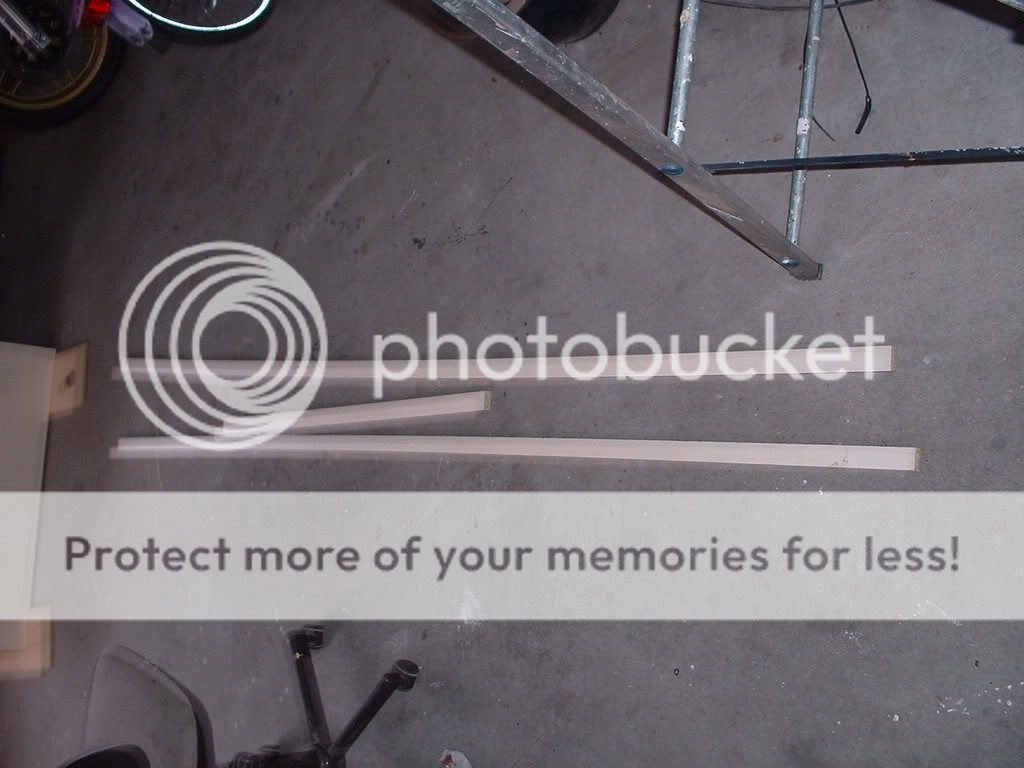
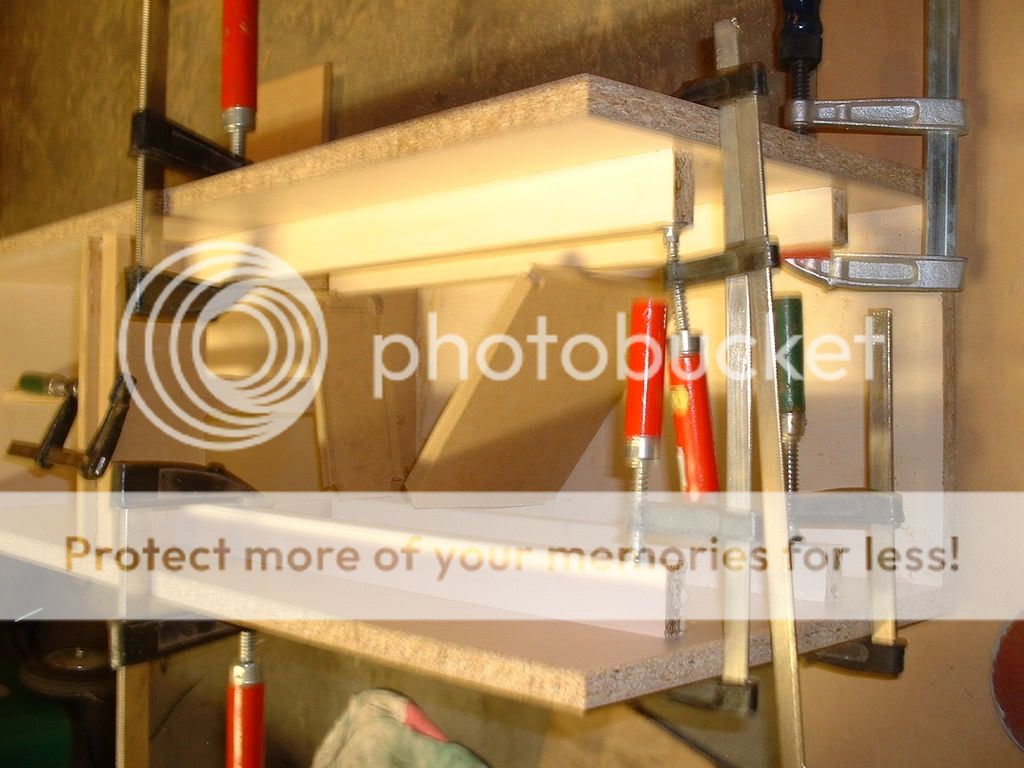
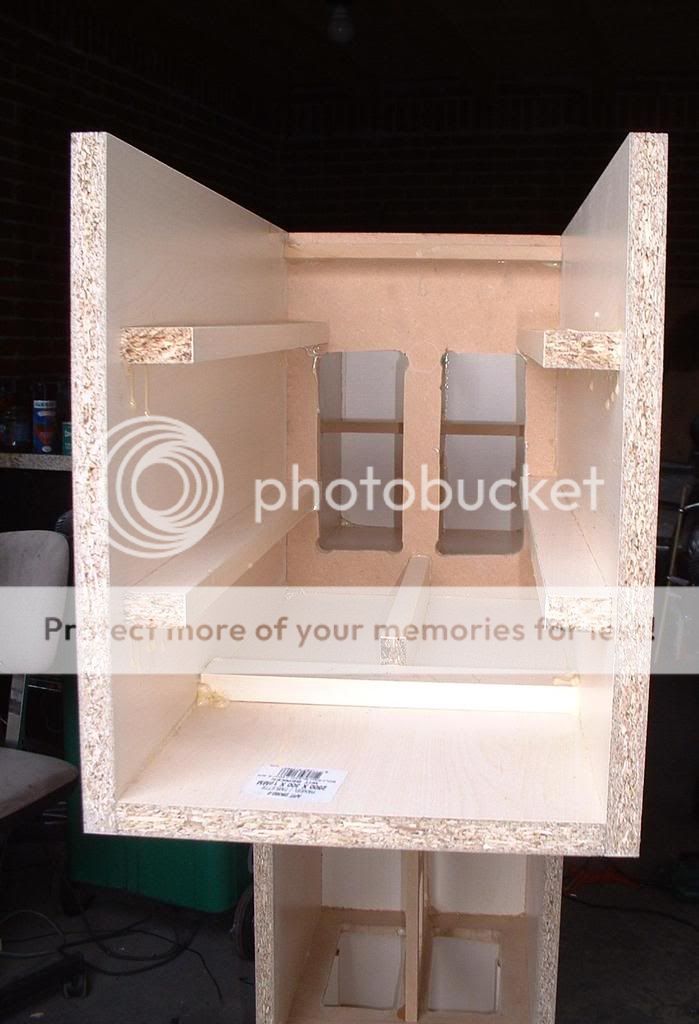
The bottom part will be accessible by removing the cover, mounted with m5 bolds and nuts how can be hammered in I have also glued them.
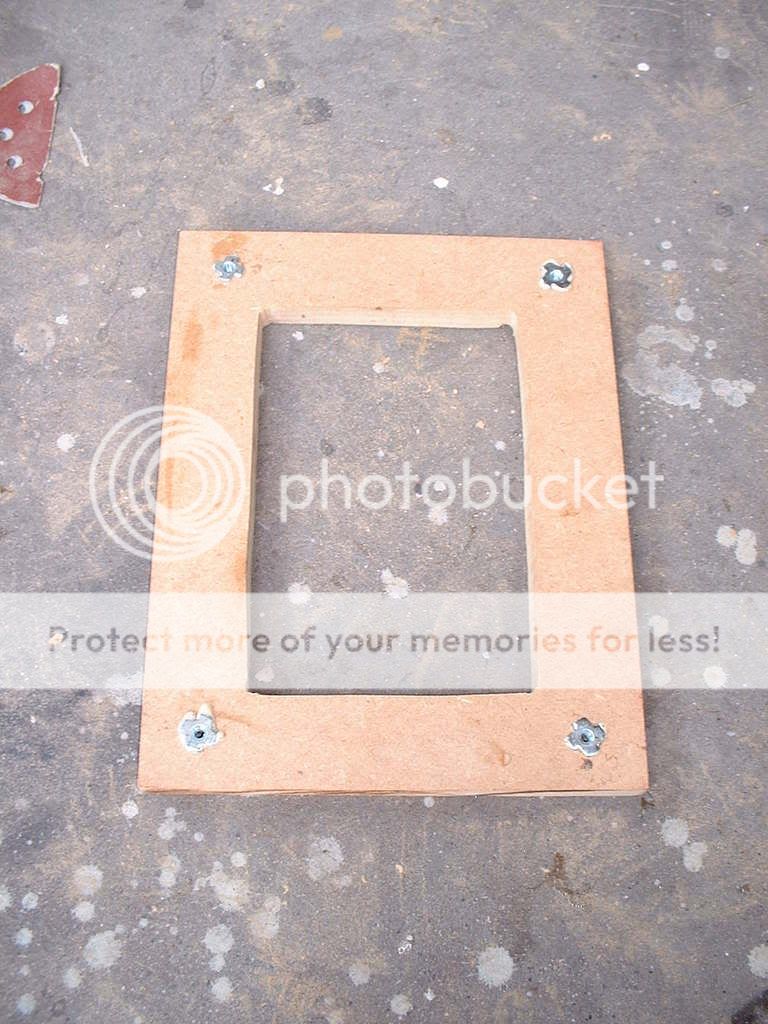
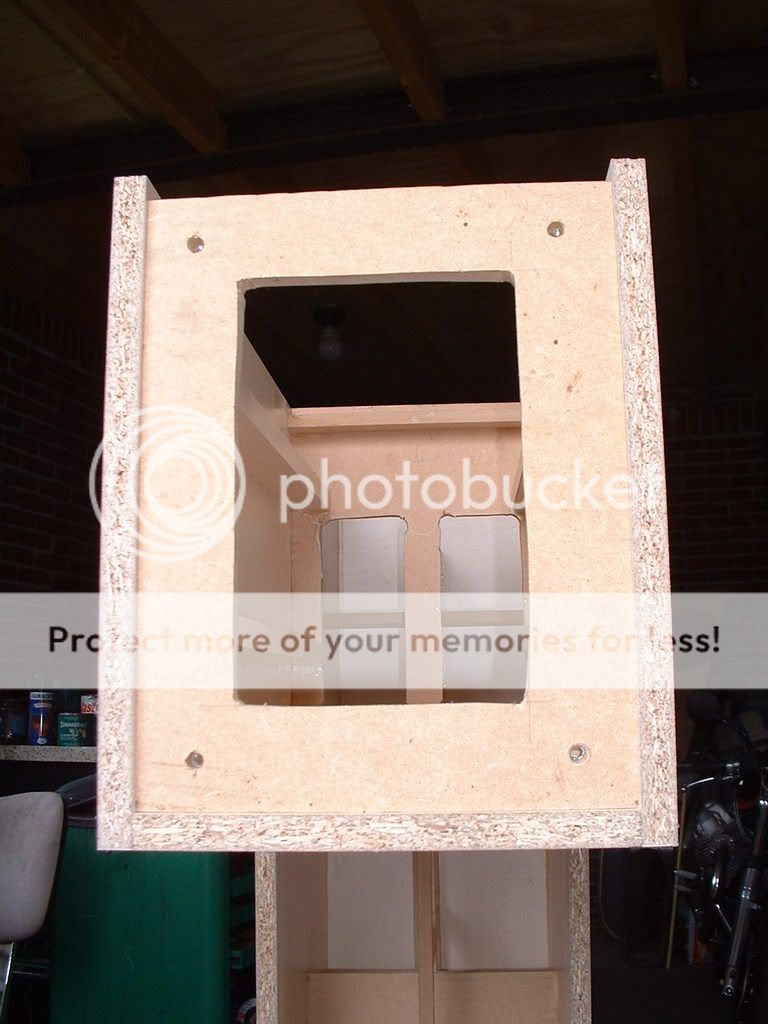
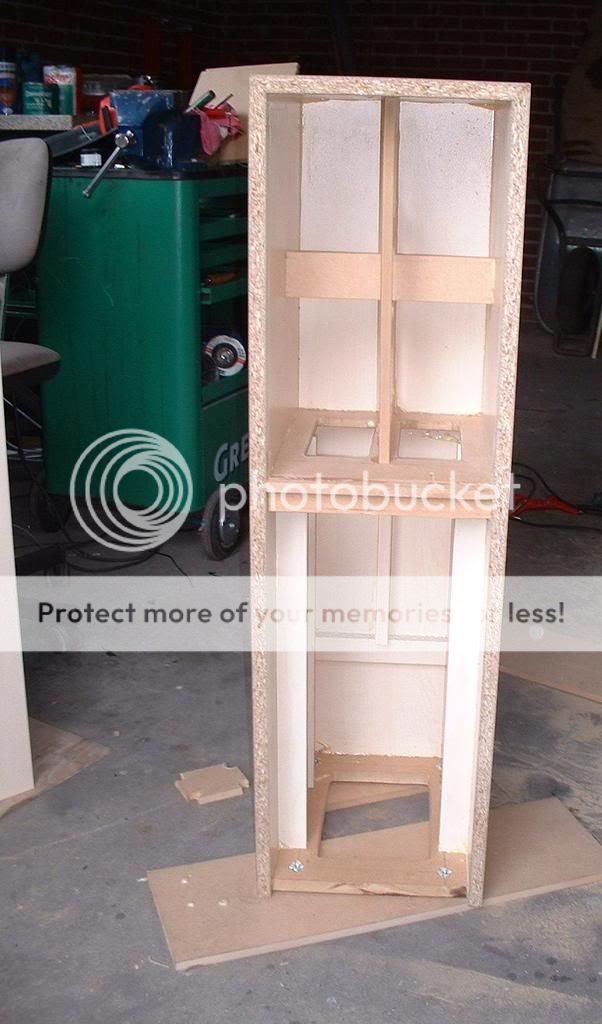
very nice design...
but I do have a few comments, and they are my standard ones:
minuses:
some pluses:
Because I am not completely aware of what may be available to you for materials, I am trying not to be typically me and be overly critical. I understand that many build with what they know or what they have available to them. As I noted above, they do look very good. I hope you and your client love the sound.
Ken Lyons, the maker of the Neuance shelving suggested that the British brand "Target"(makers of hi-fi racks and stands) uses a similar material that you used for your enclosure for their shelves and that the shelves are fairly good anti-resonant wise and in terms of energy dissipation.
And you have done all of this in a very short period of time. For that I am impressed (and I can't build anything anyways, I have two left hands...)
for some interesting projects from the Netherlands one might look here:
Regardless, you are doing what we all state we do--DIY, and that is worth the voyage in and of itself.
stew
but I do have a few comments, and they are my standard ones:
minuses:
- enclosure is made with what we in Canada call "chip board", only used in the lowest quality anything here
- the panels most likely will resonate
- both the interior and exterior should use the same finish. Eg: if polyurethane top coat on the outside, do the same on the inside
- MDF does not have the stiffness of solid lumber in the longitudinal (with the grain) direction. I would have made the bracing out of solid wood or plywood rather than MDF
some pluses:
- energy storage will not be much of an issue.
- another possible plus in your construction: the finish layer laminated to the core should be well bonded and stop typical MDF air losses
- they look very good thus far
Because I am not completely aware of what may be available to you for materials, I am trying not to be typically me and be overly critical. I understand that many build with what they know or what they have available to them. As I noted above, they do look very good. I hope you and your client love the sound.
Ken Lyons, the maker of the Neuance shelving suggested that the British brand "Target"(makers of hi-fi racks and stands) uses a similar material that you used for your enclosure for their shelves and that the shelves are fairly good anti-resonant wise and in terms of energy dissipation.
And you have done all of this in a very short period of time. For that I am impressed (and I can't build anything anyways, I have two left hands...)
for some interesting projects from the Netherlands one might look here:
Regardless, you are doing what we all state we do--DIY, and that is worth the voyage in and of itself.
stew
Re: very nice design...
These resonances will be eliminated with vibraflex.vibraflex product sheet
To mine opinion you are over estimating the influence of de wood to the quality of the box. On the a dutch forum one told me he read a test where chipboard had less panel resonances than MDF.
But this doesn't bother me because the vibraflex kills any resonance direct. The distances are so short and the panels so hard they almost cant bent so this isn't a issue in this case.
Stew when you are so sure about the use of massive lumber . Or maybe concrete.
Do you have measurements witch can proof this claim. I would like to see that.
I think the sound is made by the used chassis. When panel resonances are killed properly with hydrocarbon.
With regards Helmuth
chipboard that is the word. The chip board is laminated with formica. This give high pull strength. It gives there by high resonaces.enclosure is made with what we in Canada call "chip board", only used in the lowest quality anything here
These resonances will be eliminated with vibraflex.vibraflex product sheet
MDF does not have the stiffness of solid lumber in the longitudinal (with the grain) direction. I would have made the bracing out of solid wood or plywood rather than MDF
To mine opinion you are over estimating the influence of de wood to the quality of the box. On the a dutch forum one told me he read a test where chipboard had less panel resonances than MDF.
But this doesn't bother me because the vibraflex kills any resonance direct. The distances are so short and the panels so hard they almost cant bent so this isn't a issue in this case.
Because I am not completely aware of what may be available to you for materials, I am trying not to be typically me and be overly critical.
Stew when you are so sure about the use of massive lumber . Or maybe concrete.
Do you have measurements witch can proof this claim. I would like to see that.
I think the sound is made by the used chassis. When panel resonances are killed properly with hydrocarbon.
With regards Helmuth
Helmuth...
well chip board if used with a good adhesive, can sound very good and on it's own, superior to MDF. Enough work has been done on this by people who I trust and whose experience and comments have been documented enough times. So using chip board in my estimation is superior to MDF. Using additional dampening material is a positive of course.
Sorry I don't have any published reports, but with a little work I probably can come up with something.
You also fail to recognize that regardless what you do, the energy dissipation and storage within MDF is larger than most any other material used for loudspeaker construction.
Now as far as over-estimating the influence of the quality of the wood on the sound, again, based on personal experience, I suggest that BB or similar is superior, but your choice "chip board " is actually a good choice, and using prefinished laminate sheets is also a good choice. Very quick cabinet finishing, and good looking results with the apparent care that you have taken.
I am not a proponent of massively built loudspeaker enclosures, because they suffer many of the same problems that MDF does, namely energy storage and reflection. And yes the chassis of the loudspeaker driver itself can have a profound effect.
Helmuth, I was actually complimenting you, not tying to antagonize you. If I have, I am sorry. And yes, I do have fairly strong convictions regarding materials suitable for loudspeaker enclosures. Now if I had some Aerolam laying around, I'd try that, but alas I do not.
stew
well chip board if used with a good adhesive, can sound very good and on it's own, superior to MDF. Enough work has been done on this by people who I trust and whose experience and comments have been documented enough times. So using chip board in my estimation is superior to MDF. Using additional dampening material is a positive of course.
Sorry I don't have any published reports, but with a little work I probably can come up with something.
You also fail to recognize that regardless what you do, the energy dissipation and storage within MDF is larger than most any other material used for loudspeaker construction.
Now as far as over-estimating the influence of the quality of the wood on the sound, again, based on personal experience, I suggest that BB or similar is superior, but your choice "chip board " is actually a good choice, and using prefinished laminate sheets is also a good choice. Very quick cabinet finishing, and good looking results with the apparent care that you have taken.
I am not a proponent of massively built loudspeaker enclosures, because they suffer many of the same problems that MDF does, namely energy storage and reflection. And yes the chassis of the loudspeaker driver itself can have a profound effect.
Helmuth, I was actually complimenting you, not tying to antagonize you. If I have, I am sorry. And yes, I do have fairly strong convictions regarding materials suitable for loudspeaker enclosures. Now if I had some Aerolam laying around, I'd try that, but alas I do not.
stew
tinitus said:I reckon you are aware that MTM deappolito asks fore small mids and low xo point...theoretically
Historically i haven't been much enthused with MTMs (i did build my first one in 1975 -- Harbeth 8" + philips tweeter), but since i have recently found a mid-tweeter that lets me XO as low as 350 Hz or so, i'm going to play with them again.
dave
Re: very nice design...
Reputedly better than MDF (i haven't used it since the 70s)
dave
Nanook said:[*]enclosure is made with what we in Canada call "chip board", only used in the lowest quality anything here
Reputedly better than MDF (i haven't used it since the 70s)
dave
Re: Helmuth...
That is a shame Stew. I haven't any about this either. And with out this discussion is useless.
My college met a man how made his loudspeaker from steel.
Wait till I post my choice. but this will take a while so keep reading
Right and it resonates there by also.
@Dave
Whait till I post my choise Dave. This will take a while, firts the sub is tested for SPL so keep reading
Sorry I don't have any published reports, but with a little work I probably can come up with something.
That is a shame Stew. I haven't any about this either. And with out this discussion is useless.
This will make a great new topic every one has a opinion about it but know one seems to know data about resonance behaviour off the used materials.Sorry I don't have any published reports, but with a little work I probably can come up with something.
My college met a man how made his loudspeaker from steel.
The vibraflex works really great.Using additional dampening material is a positive of course.
You also fail to recognize that regardless what you do, the energy dissipation and storage within MDF is larger than most any other material used for loudspeaker construction.
Wait till I post my choice. but this will take a while so keep reading
Right and it resonates there by also.
I know, I make short sentences it may appear irritated to the reader. Don't bother.Helmuth, I was actually complimenting you
@Dave
Historically i haven't been much enthused with MTMs (i did build my first one in 1975 -- Harbeth 8" + philips tweeter), but since i have recently found a mid-tweeter that lets me XO as low as 350 Hz or so, i'm going to play with them again.
Whait till I post my choise Dave. This will take a while, firts the sub is tested for SPL so keep reading
Original link (dutch)
wood choise
18mm mdf
18mm chipboard
meranti plywood 18mm
birchplywood 18mm
sandwich brichplywood
wood choise
18mm mdf
18mm chipboard
An externally hosted image should be here but it was not working when we last tested it.
An externally hosted image should be here but it was not working when we last tested it.
meranti plywood 18mm
An externally hosted image should be here but it was not working when we last tested it.
birchplywood 18mm
An externally hosted image should be here but it was not working when we last tested it.
sandwich brichplywood
An externally hosted image should be here but it was not working when we last tested it.
Helmuth... testing...
as I do not read anything but English I had to rely on "Babelfish" to translate for me. I have saved the translated page and will make comments once I read it. Thank you for finding the page. I know there is a huge Dutch and German DIY community, and I only wish I could read in German or Dutch to ba able to access much of it.
I need to read the methodology used. It would also make an interesting study for someone in grad school or a technical college to perform , and also an AES study, that I had suggested some time ago.
stew.
as I do not read anything but English I had to rely on "Babelfish" to translate for me. I have saved the translated page and will make comments once I read it. Thank you for finding the page. I know there is a huge Dutch and German DIY community, and I only wish I could read in German or Dutch to ba able to access much of it.
I need to read the methodology used. It would also make an interesting study for someone in grad school or a technical college to perform , and also an AES study, that I had suggested some time ago.
stew.
So a got my some damping material to day.
2,5mm= 0,1" thick bitumen product name Vibraflex it is heavy and obstinate against vibration. The yellow paper can be removed to glue it on the wood like a sticker.
And two pyramid foam sheets to damp standing waves inside the box.
These will be processed to morrow.
Regards Helmuth
2,5mm= 0,1" thick bitumen product name Vibraflex it is heavy and obstinate against vibration. The yellow paper can be removed to glue it on the wood like a sticker.
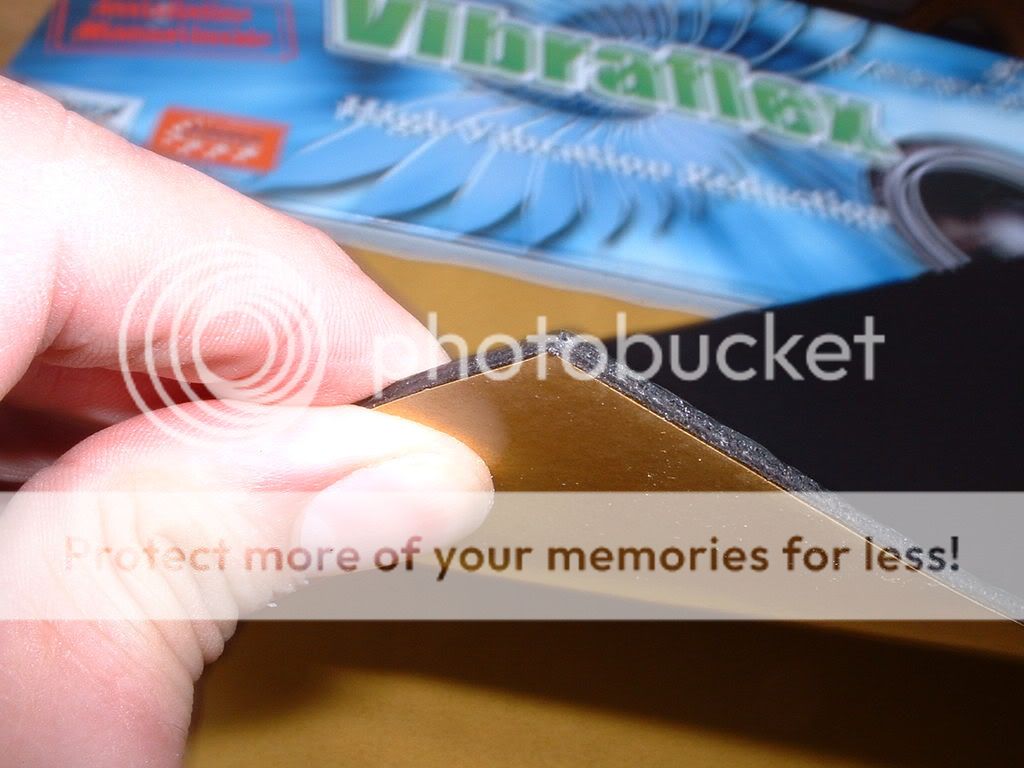
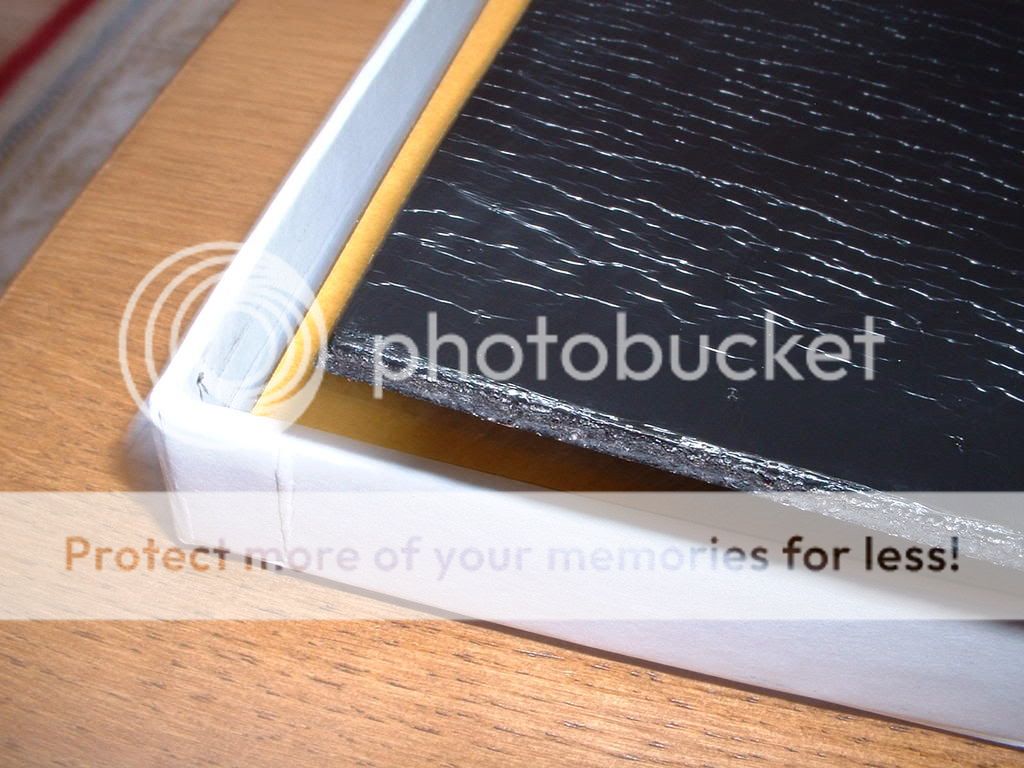
And two pyramid foam sheets to damp standing waves inside the box.
These will be processed to morrow.
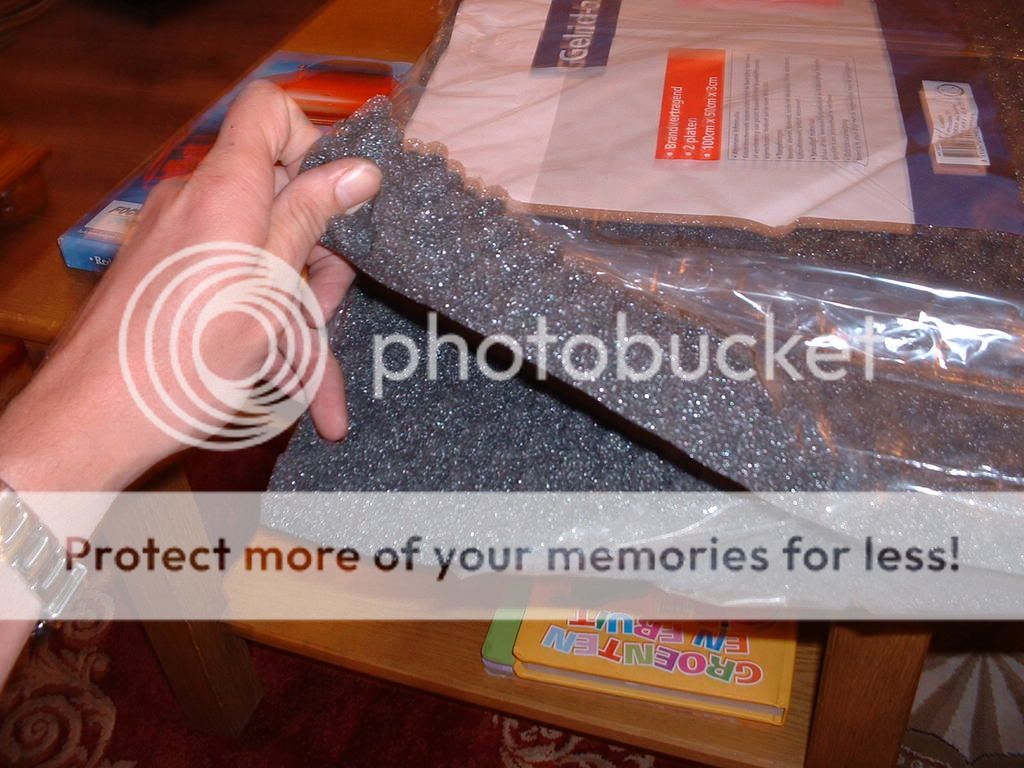
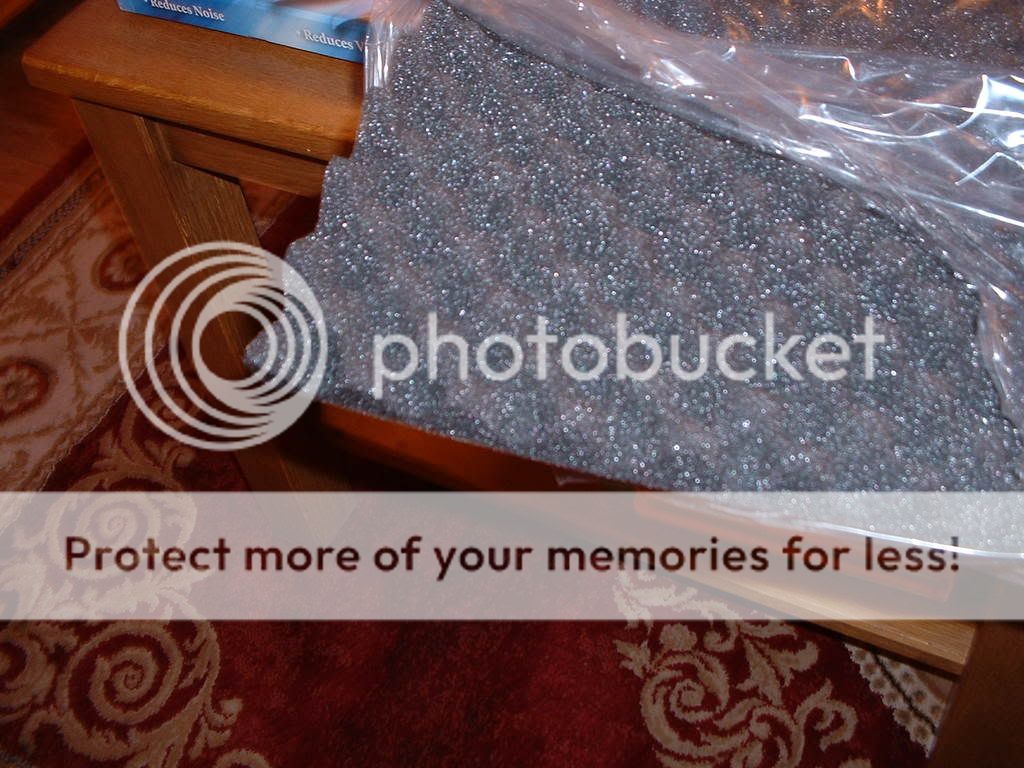
Regards Helmuth
- Status
- This old topic is closed. If you want to reopen this topic, contact a moderator using the "Report Post" button.
- Home
- Loudspeakers
- Multi-Way
- High-end 3 way dáppolito with aluminiumcone