Guys,
I see a lot of people don't like to coat the diaphragm with graphite powder. Beside it being messy, what are other disadvantages that make it inferior than other material? I have tried only liquid soap and graphite powder. The liquid soap would attract humidity in the air and make the diaphragm wet. I don't get that problem with graphite powder.
Wachara C.
I see a lot of people don't like to coat the diaphragm with graphite powder. Beside it being messy, what are other disadvantages that make it inferior than other material? I have tried only liquid soap and graphite powder. The liquid soap would attract humidity in the air and make the diaphragm wet. I don't get that problem with graphite powder.
Wachara C.
Wachara,
How many electrostatic headphones I made ? I don't know exactly, maybe 30 or 40 (or more) of different types.
Acrylic varnish are used by painters and maybe you can find it in shops for artists. Use it with an antistatic fluid and water and, after drying, try my diaphragm testing method (with safety precautions !) with 200-300 VDC and a 10 Mohms resistor.
Maybe, I tested in the past a conductive coating made of acrylic varnish and a few amount of liquid soap, I didn't wrote down all my tests.
Philippe

How many electrostatic headphones I made ? I don't know exactly, maybe 30 or 40 (or more) of different types.
Acrylic varnish are used by painters and maybe you can find it in shops for artists. Use it with an antistatic fluid and water and, after drying, try my diaphragm testing method (with safety precautions !) with 200-300 VDC and a 10 Mohms resistor.
Maybe, I tested in the past a conductive coating made of acrylic varnish and a few amount of liquid soap, I didn't wrote down all my tests.
Philippe
chinsettawong said:Vaughn,
Make yourself a pair. You won't regret it. If you need any help at all, let me know.
Wachara C.
Thank you Wachara, that is very generous of you!
I have to admit the lack of a cnc machine to make all of the parts so perfectly is what is
holding me back. I know I could make the parts with my drill press, a hand held "nibbler", files
sanding etc. They just wouldn't be as nice as yours and Philippe's work.
Still, this is something I have been thinking about for a few years now and I think it is time to get to work doing some actual experimenting.
vaughn said:
Thank you Wachara, that is very generous of you!
I have to admit the lack of a cnc machine to make all of the parts so perfectly is what is
holding me back. I know I could make the parts with my drill press, a hand held "nibbler", files
sanding etc. They just wouldn't be as nice as yours and Philippe's work.
Still, this is something I have been thinking about for a few years now and I think it is time to get to work doing some actual experimenting.
Dear Vaughn,
All you have to do is ask me for the kits.
I can make them this weekend and send them to you next week. Let me know your address.
All I ask for is that you really have to make them work. I hate to give to those who say who will do, but do not really care to finish the project.
Wachara C.
arend-jan said:Wachara, that's is such a nice offer! Can I apply for such a kit as well?
I guarantee you I will make the headphones and post pictures here.
Hi Arend-jan,
Since you ask me for it, I'll make you one set as well. Please let me know your address.
Please make sure you finish the project and post a lot pictures here.
Wachara C.
Hello,
The electrostatic cells made with rods electrodes sounds better (to my mind) but are very hard to make. I used brass, iron and copper rods. These electrostatic cells have the same dimensions and electrodes spacing, same diaphragm and polarizing voltage as the cells with perforated epoxy electrodes. Measurement also gives a bit better square waves and frequency response. The capacitance of the cell is 27 pF.
With a 500 VDC voltage applied to the the center of a diaphragm and the copper frame connected to ground, I measured a current of 0.2 µA which gives a 2.5 gigaohms resistance.
Thank you all,
Philippe
The electrostatic cells made with rods electrodes sounds better (to my mind) but are very hard to make. I used brass, iron and copper rods. These electrostatic cells have the same dimensions and electrodes spacing, same diaphragm and polarizing voltage as the cells with perforated epoxy electrodes. Measurement also gives a bit better square waves and frequency response. The capacitance of the cell is 27 pF.
With a 500 VDC voltage applied to the the center of a diaphragm and the copper frame connected to ground, I measured a current of 0.2 µA which gives a 2.5 gigaohms resistance.
Thank you all,
Philippe
Phil47 said:Hello,
The electrostatic cells made with rods electrodes sounds better (to my mind) but are very hard to make. I used brass, iron and copper rods. These electrostatic cells have the same dimensions and electrodes spacing, same diaphragm and polarizing voltage as the cells with perforated epoxy electrodes. Measurement also gives a bit better square waves and frequency response. The capacitance of the cell is 27 pF.
With a 500 VDC voltage applied to the the center of a diaphragm and the copper frame connected to ground, I measured a current of 0.2 µA which gives a 2.5 gigaohms resistance.
Thank you all,
Philippe
Hi Philippe,
That's is very interesting. Maybe I will give this kind of stator a try in the future. Thanks a lot for your information.
Wow, the resistance is so high and yet it works. Thanks for sharing.
Of all the headphones you have made, may you show us your favorite? How about your favorite ES headphone amplifier?
Wachara C.


Wachara you are a credit to this community, I have sent you a pm regarding the parts.
I promise that I will build them into a working headphone or die trying!
It make take a bit as I would also have to build the energizer, but I have made a few tube amps, preamps and headphone amps so this should not be overly difficult.
Hi Wachara and all,
I don't have favorite. It all sounds good.
Photo of an epoxy frame and an electrode plate made with "piano wires" :
I don't have favorite. It all sounds good.
Photo of an epoxy frame and an electrode plate made with "piano wires" :
An externally hosted image should be here but it was not working when we last tested it.
If I had to guess I would say that stator is milled from a sheet
of material then electroplated, not from piano wires. Since Philippe says
it is from piano wires I assume it must be. I suppose you could braze them(hard silver
solder used in jewelry making) but this would heat up the piano wire to a point that it
would change it's properties. I think they could also be wound around a stator plate like
a bobbin and then plated but it doesn't look like this is what has been done here.
I have begun preparing some copper and selecting some wood for building an energizer
after the design Wachara posted. I am also keeping an eye out for some nice quality ribbon
cable to construct the headphone cable out of. I am wondering which connector you guys are
using for your plug and jack connections on the headphone cable?
of material then electroplated, not from piano wires. Since Philippe says
it is from piano wires I assume it must be. I suppose you could braze them(hard silver
solder used in jewelry making) but this would heat up the piano wire to a point that it
would change it's properties. I think they could also be wound around a stator plate like
a bobbin and then plated but it doesn't look like this is what has been done here.
I have begun preparing some copper and selecting some wood for building an energizer
after the design Wachara posted. I am also keeping an eye out for some nice quality ribbon
cable to construct the headphone cable out of. I am wondering which connector you guys are
using for your plug and jack connections on the headphone cable?
Last night I had a chance to try the 0.9 microns mylar which I bought from the USA. Interestingly, I didn't find the diaphragm to be more efficient than the 6 microns one. Overall, the mid and high sounded about the same as the 6 microns. But the low frequency wasn't as good.
I'll try the 1.4 micron mylar tonight, and will report soon.
I also tried a can of graphite lube spray last night. The stuff was meant for lubrication on machinery. Once sprayed, it left a very thin layer of dried graphite on the surface. The graphite was dried and adhered to the membrane very well - I couldn't rub the graphite off with my fingers. I checked the resistance and I measured around 2 meg ohm. It was really easy to apply. But one thing that I didn't like it was that it left the diaphragm with very dark color. What do you guys think about this stuff?
Wachara C.
I'll try the 1.4 micron mylar tonight, and will report soon.
I also tried a can of graphite lube spray last night. The stuff was meant for lubrication on machinery. Once sprayed, it left a very thin layer of dried graphite on the surface. The graphite was dried and adhered to the membrane very well - I couldn't rub the graphite off with my fingers. I checked the resistance and I measured around 2 meg ohm. It was really easy to apply. But one thing that I didn't like it was that it left the diaphragm with very dark color. What do you guys think about this stuff?
Wachara C.
chinsettawong said:Last night I had a chance to try the 0.9 microns mylar which I bought from the USA. Interestingly, I didn't find the diaphragm to be more efficient than the 6 microns one. Overall, the mid and high sounded about the same as the 6 microns. But the low frequency wasn't as good.
I'll try the 1.4 micron mylar tonight, and will report soon.
I also tried a can of graphite lube spray last night. The stuff was meant for lubrication on machinery. Once sprayed, it left a very thin layer of dried graphite on the surface. The graphite was dried and adhered to the membrane very well - I couldn't rub the graphite off with my fingers. I checked the resistance and I measured around 2 meg ohm. It was really easy to apply. But one thing that I didn't like it was that it left the diaphragm with very dark color. What do you guys think about this stuff?
Wachara C.
I could personally live with the dark color if it is doing everything else right. Maybe you
could try them in a test rig and let us know how it sounds?
vaughn said:
I could personally live with the dark color if it is doing everything else right. Maybe you
could try them in a test rig and let us know how it sounds?
Hi Vaughn,
I actually applied the stuff on the 0.9 microns diaphragm and tried last night. Like I said, the sound was alright except that the low frequencies were not as good as the 6 microns one.
The picture shows how the diaphragm looks like after one pass coating of this stuff.
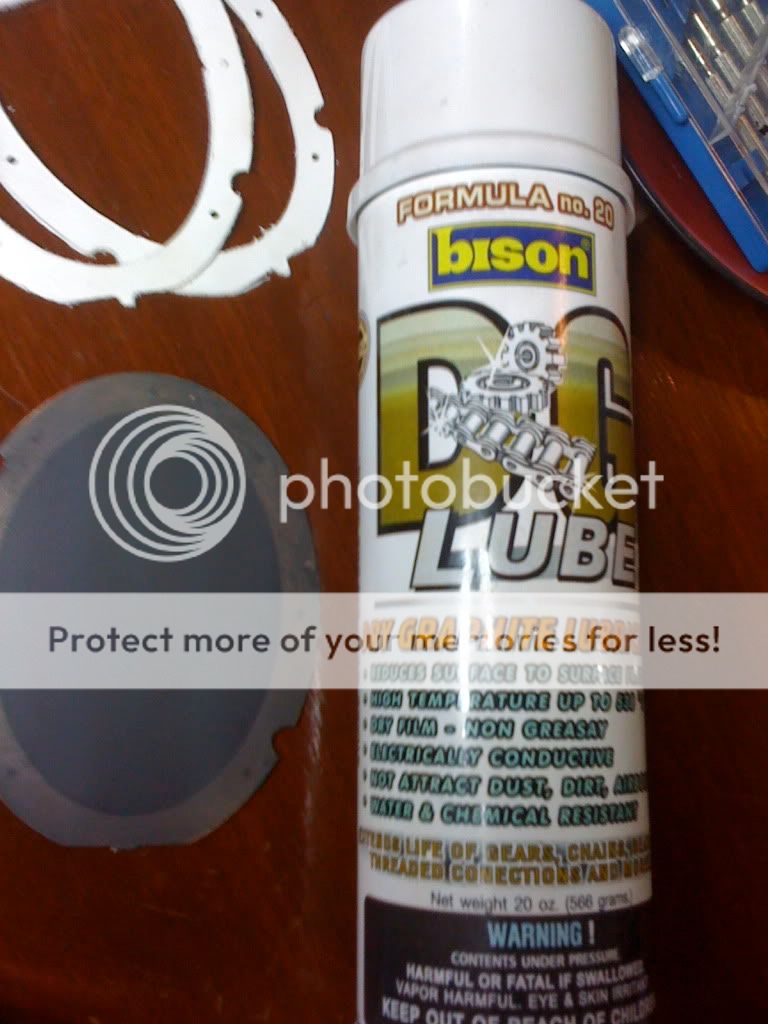
Wachara C.
As you have found out, this kind of coating works. But theoretically the higher the resistance of the coating, the lower the distortion (constant charge operation).
Some people like to use the formula (I believe first postulated by Hunt) where the minimum surface resistance is calculated by looking at the lowest frequency to be reproduced and choosing the SR such, that the voltage on the diaphragm can't change significantly within (half) a period of that signal.
For a full range speaker it is commonly recommended to use a coating with a resistance between 10E9 and 10E12 Ohms per square.
In my opinion, an ESL does indeed sound better with high SR coating even if it is not full range.
I suppose for a headphone this could be less problematic if the deflection of the diaphragm is small compared to the stator spacing.
Some people like to use the formula (I believe first postulated by Hunt) where the minimum surface resistance is calculated by looking at the lowest frequency to be reproduced and choosing the SR such, that the voltage on the diaphragm can't change significantly within (half) a period of that signal.
For a full range speaker it is commonly recommended to use a coating with a resistance between 10E9 and 10E12 Ohms per square.
In my opinion, an ESL does indeed sound better with high SR coating even if it is not full range.
I suppose for a headphone this could be less problematic if the deflection of the diaphragm is small compared to the stator spacing.
- Status
- This old topic is closed. If you want to reopen this topic, contact a moderator using the "Report Post" button.
- Home
- Amplifiers
- Headphone Systems
- Has anybody made an ELS headphone?