Yes, the magnets can be loaded into the back, but it will likely be much tricker to get them to line up.
Not really Dave. It was pretty easy. See the picture. I just bored little holes and stuck the magnet in there with an epoxy glue. I did this for all the speakers I built and then veneered on top of the magnets.
The grill had corresponding metal tabs that aligned with the magnets. This was about 3 years ago. So far it has held well.
The whole thread is here.
Pictures of Selah designed Tempesta Extreme and RC4 (no subwoofer)
Attachments
Wayne - yup the choices in true "acoustic" speaker cloth are much reduced over what I can remember from the late 60's early 70's, which was long before I started building. One of the local shops carried at least half a dozen patterns on a bulk roll rack.
Take a look at Parts Express? That could be the most inconvenient part of this build for you.
Speaker Grill Cloth & Fabric in the Speaker Components Department at Parts Express | 319
Sunday would be better - and who needs more fish? Oh, yah, I remember now
Take a look at Parts Express? That could be the most inconvenient part of this build for you.
Speaker Grill Cloth & Fabric in the Speaker Components Department at Parts Express | 319
Sunday would be better - and who needs more fish? Oh, yah, I remember now
This is a hybrid between transmission-line and a "karlsson-speaker". Author of this speakers - Alexander Rogozhin![]()
Mr. Rogozhin
Please, is this the plans? Folded paper or in .pdf?
Any further stuffing directions?
Rogozhin Labyrinth for Fullrange Loudspeaker Sonido SFR 175F A | eBay
Thanks
Dear Dave (Planet 10),
I am planning to build the nScan-Ken 0v9. I have the design you posted, but the cut plan is not very clear. Also I do not understand from the drawing how is the front vent made.
Additionally I have in the back of my mind to build them drilling a solid block of wood. This would be to build a very nice one. For an easy probably not so beautiful one, has somebody ever tried to 3D print the chassis ?
Thanks,
Davide
I am planning to build the nScan-Ken 0v9. I have the design you posted, but the cut plan is not very clear. Also I do not understand from the drawing how is the front vent made.
Additionally I have in the back of my mind to build them drilling a solid block of wood. This would be to build a very nice one. For an easy probably not so beautiful one, has somebody ever tried to 3D print the chassis ?
Thanks,
Davide
I am planning to build the nScan-Ken 0v9. I have the design you posted, but the cut plan is not very clear. Also I do not understand from the drawing how is the front vent made.
Here is the link to the updated plans which are finished enuff for release. It has a cut-plan and a visualization which should answer your questions.
http://www.planet10-hifi.com/downloads/nScan-Ken-1v0-071115.pdf
Additionally I have in the back of my mind to build them drilling a solid block of wood. This would be to build a very nice one. For an easy probably not so beautiful one, has somebody ever tried to 3D print the chassis ?
Might be possible. Carved from solid would require at least 1 removable panel i expect, and would have a greater tendency to crack than if made from panels.
It certainly could be 3D printed.
dave
I was thinking of making the internal surfaces of the speaker in a beehive structure.
Additionally to have an angle (5 degrees) between the side walls. Not sure what would be worth for the back panel.
It will have to be printed in two pieces, basically all the box in one piece and the back panel in a second piece, otherwise it will be very difficult to remove the filling that the printer add from the inside.
This should replace the wool lining inside. I don't think it make sense to have both a structure on the wall and the wool lining. Is it correct ?
Thanks,
Davide
Additionally to have an angle (5 degrees) between the side walls. Not sure what would be worth for the back panel.
It will have to be printed in two pieces, basically all the box in one piece and the back panel in a second piece, otherwise it will be very difficult to remove the filling that the printer add from the inside.
This should replace the wool lining inside. I don't think it make sense to have both a structure on the wall and the wool lining. Is it correct ?
Thanks,
Davide
To achieve a rapid room modes decay [AKA 'slap' echo], expand parallel walls to a >12 deg [included] angle, so some form of trapezoid shape like used in a 'LEDE' room design is desirable for a speaker also. With a bit of damping at the closed end [if vented], otherwise at the big end or along one side, top and back, I see no reason to get carried away adding any time consuming resonant 'traps': https://www.google.com/webhp?sourceid=chrome-instant&ion=1&espv=2&ie=UTF-8#q=LEDE+room
GM
GM
3D organic shape linearray
Building speakers using plane panels was no longer satisfying to me.
So I built my own CNC mill.
Here is my first 3D organic shaped design:
Front is solid birch.
Rear is MDF covered with black leather.
Chasis are PEERLESS TC9FD-18-08 wired two parallel and then in series.
The shape follows the B&W Nautilus idea:
Narrow baffle prevents early reflections.
Tappered sidewalls guides the rear membrane energy into something like an acoustic trap.
The result is an almost flat response from 200Hz to 16kHz without any equalization or filter. Between the chasis and my Aleph-X is only the wire.
OK, I use active crossover (Thel Audio) at 200Hz.
Another design feature is the linearray arrangement. This reduces the reflections from bottom and ceiling.
Sitting at the sweet spot is like entering the holo deck in terms of 3-dimensional soundstaging.
You will find some videos here showing my progress on CNC and milling this enclosure:
https://www.youtube.com/channel/UCfz4LGcU-UtLWpBZuPdCNgA
Hope you like my design.
Any comments are welcome.
Building speakers using plane panels was no longer satisfying to me.
So I built my own CNC mill.
Here is my first 3D organic shaped design:
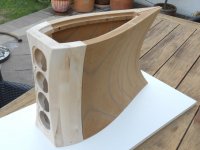
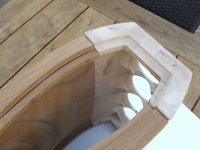
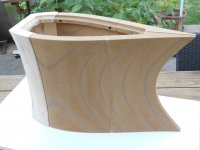

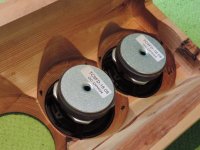
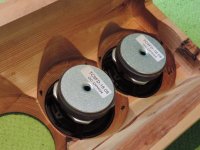
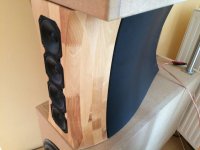
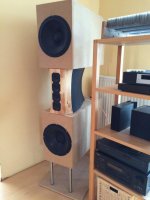
Front is solid birch.
Rear is MDF covered with black leather.
Chasis are PEERLESS TC9FD-18-08 wired two parallel and then in series.
The shape follows the B&W Nautilus idea:
Narrow baffle prevents early reflections.
Tappered sidewalls guides the rear membrane energy into something like an acoustic trap.
The result is an almost flat response from 200Hz to 16kHz without any equalization or filter. Between the chasis and my Aleph-X is only the wire.
OK, I use active crossover (Thel Audio) at 200Hz.
Another design feature is the linearray arrangement. This reduces the reflections from bottom and ceiling.
Sitting at the sweet spot is like entering the holo deck in terms of 3-dimensional soundstaging.
You will find some videos here showing my progress on CNC and milling this enclosure:
https://www.youtube.com/channel/UCfz4LGcU-UtLWpBZuPdCNgA
Hope you like my design.
Any comments are welcome.
Here is my first 3D organic shaped design:
Very nice shape. Marvelous. Bravo!!!
Sorta ruined by sandwiching it between the 2 monkey coffin bass boxes … there is your next project.
I wouldn't have used MDF, and they probably deserve a better driver than the TC9, our pr were quite disappointing. But if you are happy that is all that counts.
dave
I'd have used quality plywood… MDF has too much energy storage, emitting a time delayed ooz that masks low level detail.
Here it has the advantages of easy maching and it looks like a sort of plywood made with thick plies of MDF was used, plus the TC9 does not have very good DDR and since that detail is already missing, the MDF is not as likely to be a big deal.
dave
Here it has the advantages of easy maching and it looks like a sort of plywood made with thick plies of MDF was used, plus the TC9 does not have very good DDR and since that detail is already missing, the MDF is not as likely to be a big deal.
dave
Building speakers using plane panels was no longer satisfying to me.
So I built my own CNC mill.
Wow! That is serious DIY, very cool and with great result.
R.
- Home
- Loudspeakers
- Full Range
- Full Range Speaker Photo Gallery