Or at least I will...
I made the one have when I was 15, but my metal and woodworking skills have drastically improved over the past five years...
I am building it out of four shelves(haven't decided whether I want white oak or mahogany), and rather than constructing the whole thing out of wood, I have four "four-foot" lengths of 6061 aluminum roundstock which will act as the support poles. each corner of every shelf will have a hole drilled in it, and the shelves will be supported on the Al poles with a steel collar under every corner.
Instead of setting the whole thing on heavy feet w/carpet-piercing spikes, I'm going to machine a spike on the end of each pole.
Which wood is better for vibration isolation? I have heard claims that air-dryed maple is the absolute best(since they use it to make musical insturments), but it is not readily available, and is outrageously expensive.
Has anybody else made their own rack?
-Trevor
PS- I would like to use brass roundstock, but it's considerably more expensive than aluminum
I made the one have when I was 15, but my metal and woodworking skills have drastically improved over the past five years...
I am building it out of four shelves(haven't decided whether I want white oak or mahogany), and rather than constructing the whole thing out of wood, I have four "four-foot" lengths of 6061 aluminum roundstock which will act as the support poles. each corner of every shelf will have a hole drilled in it, and the shelves will be supported on the Al poles with a steel collar under every corner.
Instead of setting the whole thing on heavy feet w/carpet-piercing spikes, I'm going to machine a spike on the end of each pole.
Which wood is better for vibration isolation? I have heard claims that air-dryed maple is the absolute best(since they use it to make musical insturments), but it is not readily available, and is outrageously expensive.
Has anybody else made their own rack?
-Trevor
PS- I would like to use brass roundstock, but it's considerably more expensive than aluminum
I did a rack 4 years ago to hold my gear. It's designed to be strong whitout being to "heavy" to look at. Here's a bit more info: http://kofoedmejer.squarespace.com/display/ShowGallery?moduleId=364576&galleryId=20186
Regards TroelsM
Regards TroelsM
Attachments
Trevor, I'm planning to make a rack sometime over the next few months as well ...
I don't see how timber is going to help with vibration in any way. You want something more springy than timber.
I'm also planning to run cables through some columns out the back to try to avoid having them visible (speaker, power and interconnects). Also I plan to have an adjustable system, more readily adjustable than a flexirack, yet one that doesn't look as adjustable - possibly some capscrews. So there will be a few spines carrying cables and acting as structure with some rods allowing adjustment. I mention this just in case you want some ideas 😉
I don't see how timber is going to help with vibration in any way. You want something more springy than timber.
I'm also planning to run cables through some columns out the back to try to avoid having them visible (speaker, power and interconnects). Also I plan to have an adjustable system, more readily adjustable than a flexirack, yet one that doesn't look as adjustable - possibly some capscrews. So there will be a few spines carrying cables and acting as structure with some rods allowing adjustment. I mention this just in case you want some ideas 😉
Go HERE, a lot of what this guy claims is cr@p, but I buy some of it. It seems to make sense to me that minute vibrations could get dispersed throughout dense wood(though ther must be a limit; ebony is about as hard as rock), thereby eliminating them.paulspencer said:
I don't see how timber is going to help with vibration in any way. You want something more springy than timber.
but PS- I rest my turntable on a bed of bubble wrap.
But then they wouldn't be easily accesible... Though if you plan on having the same components on the same shelve permenantly, then it's actually quite a nice idea. I like tinkering with my stuff, though, which means a lot of uninstallation.paulspencer said:
I'm also planning to run cables through some columns out the back to try to avoid having them visible
Sir Trefor said:Go HERE, a lot of what this guy claims is cr@p, but I buy some of it.
I'm putting a restraining order on myself here. I will not mention words like "snake oil" or "myth" or phrases like "waste of money", I won't! The order will also prevent me from ranting in any form on this thread ... *holds breath* ... I think I can, I think I can, I think I can ....
Sir Trefor said:It seems to make sense to me that minute vibrations could get dispersed throughout dense wood(though ther must be a limit; ebony is about as hard as rock), thereby eliminating them.
What is your goal here? If you want to isolate audio equipment on the rack from any vibrations of the floor, then wood is clearly not the way to go. There may be some infantessimally small damping going on but it will pass the energy through - solid things will move! You want something with some spring to dampen vibrations.
You may like the result of using wood - perhaps there is some coloration added that you like. With a turntable its almost like looking at a mirror looking at a mirror looking at a mirror ... it picks up the vibration that it originally caused then amplifies it again ...
If you like the result go with it. But I wouldn't call this "isolation."
Now off on another tangent ... in a way he has done you a psycho acoustic favour. He has given you enough for your brain to believe that there is a sonic benefit to using wood. I actually think the brain is very very powerful in influencing our perception of what we hear. In this case, going with the maple is going to be cheap. It wouldn't surprise me if a thing like this is enough for your brain to create a sensation you perceive as more musical. Whether or not an actual objectively audible (ie in a blind AB comparison) difference is needed for this to work is another question.
Sir Trefor said:But then they wouldn't be easily accesible... Though if you plan on having the same components on the same shelve permenantly, then it's actually quite a nice idea. I like tinkering with my stuff, though, which means a lot of uninstallation.
I've been living with a "work in progress" system for a while, no purpose-built rack. This summer I want to get it into a state that looks finished! ...
Not really the solution for someone who wants to take it apart and tweak all the time. But then, having designed to allow for hiding cables doesn't mean you have to use the facility. The left column can carry power cable, interconnects on the right, and speaker cable hmmmmmmm ... undecided so far, don't really want a third column!
Wow, can't believe I got into this kind of discussion over an audio rack *chuckles* ... what a bizarre hobby this is ...
Then why is concrete such an excellent damper?paulspencer said:
If you want to isolate audio equipment on the rack from any vibrations of the floor, then wood is clearly not the way to go. There may be some infantessimally small damping going on but it will pass the energy through - solid things will move! You want something with some spring to dampen vibrations.
What if you have the TT sitting on spiked feet; wouldn't vibration be drawn away from it? If your turntable generates that vibration that we all hate, and it sits on some sort of damping "pad" or sorbothane feet (etc.), all of your other components will most certainly be isolated from it. But any vibration caused by the TT motor will stay in the turntable.You may like the result of using wood - perhaps there is some coloration added that you like. With a turntable its almost like looking at a mirror looking at a mirror looking at a mirror ... it picks up the vibration that it originally caused then amplifies it again ...
Shouldn't a good rack design incorporate isolation from both outside sources and internally generated vibration?
Then again, I know a guy who has a rack made entirely out of 3/8" thick plate steel. His "big thing" is electromagnetic isolation...
Wow, can't believe I got into this kind of discussion over an audio rack *chuckles* ... what a bizarre hobby this is ...
Maybe I'm overanalyzing this whole thing; or maybe, just like every other component of your system, a different rack design offers a different advantage.
Alright, then. I'll buy that.If you like the result go with it. But I wouldn't call this "isolation."
going with the maple is going to be cheap.
Actually, maple costs roughly twice as much as pine, it's a hardwood; denser than mahogany or oak(depending on what variety).
What if you have the TT sitting on spiked feet; wouldn't vibration be drawn away from it? If your turntable generates that vibration that we all hate, and it sits on some sort of damping "pad" or sorbothane feet (etc.), all of your other components will most certainly be isolated from it. But any vibration caused by the TT motor will stay in the turntable.
I know of no evidence that spikes act directionally, and 'draw away' vibration. Whilst the points may well improve coupling to the shelf etc., energy transfer is the same both ways. (Note that some manufacturers / users prefer their spikes 'upside down', and still claim good results.) Therefore energy stored in the shelf can be reflected back into the t/t.
Sorbothane is so-called for a good reason - it absorbs vibrational energy (more accurately, converts it to heat), as do all such resilient materials.
I find it interesting that so many people recommend (correctly, IMHO) damping material on equipment cases, but also prefer 'open' shelves to closed housings. My gear fits snugly int 'cubbyholes', with high density foam linings - because it sounds better to me that way.
Good results are claimed for the TNT racks - easy to build and 'dress up', simple to level, and inexpensive (depending on your chosen materials).
Then why is concrete such an excellent damper?
It isn't. Its just very heavy and solid. Put anything on it that is vibrating, say a subwoofer for example, and the mass of the concrete means it has a strong resistance to movement. Say that subwoofer is on a slab of concrete, the sub if it is vibrating might jump around on top of it, but the concrete is so heavy, it probably won't perceptibly move. The subwoofer may make noise as it jumps up and down hitting the concrete, but probably not much will transfer.
Now put a jack hammer onto the concrete and you will find out how much damping you get from the concrete. Now the force will either break up the concrete or transfer the vibrations through.
What if you have the TT sitting on spiked feet; wouldn't vibration be drawn away from it? If your turntable generates that vibration that we all hate, and it sits on some sort of damping "pad" or sorbothane feet (etc.), all of your other components will most certainly be isolated from it. But any vibration caused by the TT motor will stay in the turntable.
I was not referring to vibrations from the turntable actually in that way. The turntable is the source causing the speakers to make vibrations. If the turntable then picks up those vibrations from the speakers, it will then amplify those vibrations and cause coloration. If this is happening, this is when the material of the wood may have some effect. My point was not so much to get into that side of things, but merely to point out that with this approach, accuracy is obviously not the goal. I don't disagree with that, you are welcome to do your thing your way.
So what I'm saying is be aware of what you are aiming for and sure that what you are doing will actually achieve it.
Shouldn't a good rack design incorporate isolation from both outside sources and internally generated vibration?
Yes, if accuracy is your goal. This is why I wouldn't bother with wood for isolation. You want damping, some kind of system with spring. Perhaps a spring system, or just something like foam. There are a lot of ways you could do it.
Maybe I'm overanalyzing this whole thing; or maybe, just like every other component of your system, a different rack design offers a different advantage.
Well, if you can't over-analise your hobby, what can you over-analyse!!!
Actually, maple costs roughly twice as much as pine, it's a hardwood; denser than mahogany or oak(depending on what variety).
Aren't we talking about a few tiny 'lil bits of wood maybe turned on a lathe? If it even just creates an illusion of improvement for a few dollars, then who cares? It's cheap! There are a lot of things no better than this which could set you back thousands and some might even do more harm than good!
IMO spikes have no real acoustic function. They look good. They don't isolate anything or provide damping (unless they have pads, but then its the pad and not the spike). I have spikes (cones actually) because they look good, that's all. They could make things worse. On a timber floor they could couple the speakers to the floor. Say you have carpet, which will provide damping. Now what you do with speakers for example, is provide a more solid path for vibration to be coupled to the floor, so it will vibrate and act as a secondary transducer. This will colour the sound, and I suppose you could even call it distortion, although its not one normally measured, but its going to be audible. You may like it, you may not.
Again I marvel at the scope of this discussion for something as "simple" as a rack!
The main reason why suspending or decoupling your turntable from the floor works so well is as Paul said: positive feedback from the speakers, through the floor and air into your turntable, and back to the stylus, colours the sound. In the worst case, at high volume levels, the feedback will be so bad that howling is set up. Try turning the turntable off, rest the stylus on the record, turn the volume up, and give the record a slight tap, to see what feedback causes. That’s why a number of turntable manufacturers back in the 1970’s, such as Linn, Thorens and AR had better sounding turntables than ones with no suspension, because their suspension cancelled out most of the vibration from the speakers getting back to the stylus of the turntable. Coupling your turntable back to the speakers by solid supports, whether they are spikes or not, is not good. The way to stop turntable motor vibration from getting back to the stylus is by having the tonearm and platter decoupled from the motor on their own floating base, by a suspension system, like Linn (Sondek) or other belt drive turntables often do; or decoupling the motor via rubber mountings, as Rega (Planar 3) and many other manufacturers, including many Japanese belt drives, used to do; or making the motor relatively vibrationless, as Rega (P3/5/7) do now, or as the Japanese (like Technics) do with their low (platter) speed, direct drive motors (e.g. Technics SL-1200). Manufacturers also often make their more expensive turntables from materials which don’t resonate much, which is why acrylic and glass platters are often used these days, and acrylic plinths, and combinations of plinth materials.
The reason why maple may be used for instruments like violins could be because it resonates well, in which case it may not necessarily be the best material for a hi-fi rack. My expertise isn’t music, but I have a brother who plays the violin in an orchestra, as well as collecting and repairing them, so I’ll ask him when I see him at Christmas, if I remember. In fact, I did a quick search on violin making, and the first one I came to, http://www.centrum.is/hansi/construction.html , mentioned that the front and back of the violin have to be very thin, and resonate very well! So I certainly wouldn’t pay too much attention to what the chap from Mapleshaderecords says. It sounds as if he likes the colouration that resonating woods like maple introduce. His rubbish about how if you don’t have his miraculous speaker cables, your $2000 speakers can sound like $100 ones is just that – rubbish which is designed to part wealthy, gullible people from their money. They may very well make your speakers sound better, but the difference wouldn’t be equivalent to spending $1900 more on your speakers, as he seems to imply! No doubt if he gave the cables to a hi-fi reviewer and promised to advertise with them, they’d say how much different they make speakers sound, but then they’re hardly impartial, are they? He also says that long speaker cables are better than short ones. Obviously the electrical engineering that I was taught about making wires as short as possible to minimise resistance was wrong! And directional wires?? Obviously they wouldn’t be any good at passing AC signals then – maybe they’re for DC power supplies? Don’t waste your time looking at his site. It looks to me as though he’s got little in the way of engineering knowledge, so he resorts to making things up to try and sound knowledgeable. His website is a combination of truths, half-truths, sheer rubbish, and advertising. Sometimes all in the one sentence! It would be funny if it wasn’t so misleading to hi-fi buffs who have little engineering knowledge.
Alright, I’ve had my rant and I feel better – now back to practicalities. Many hi-fi rack manufacturers isolate their racks by sitting the shelves on vibration isolating pads, such as rubber, foam or other materials. It helps to also have a relatively non-resonant material to make it out of – many make them out of glass, which resonates at a quite high frequency, or out of MDF, which is less resonant than most natural wood. That’s why virtually all speaker manufacturers make speakers out of MDF or similar materials. The MDF is less resonant because it is wood that’s been broken up into very small woodchips, then glued and compressed back together, rather than having a nice naturally resonant grain running through it, like maple, oak, eucalypt or any other tree wood! Whether it makes much difference to an amplifier is debatable, but under an electro-mechanical turntable, non-resonant and de-coupled from the environment is best. Resting your turntable on bubble wrap is probably good, if it’s several layers of bubble wrap. Using two bicycle tubes, inflated to a very low pressure, under a shelf resting on them, is another idea I’ve heard, and there is a commercial anti-vibration shelf using that idea being marketed, although it’d be cheaper to make your own.
And dnsey, the reason why many people prefer open racks rather than closed racks is probably to provide good cooling for electronic equipment, particularly high power amps, which get hot when working hard. It may make sense to keep sound waves away from things like turntables, but most electronic equipment is more reliable if it's kept relatively cool.
The reason why maple may be used for instruments like violins could be because it resonates well, in which case it may not necessarily be the best material for a hi-fi rack. My expertise isn’t music, but I have a brother who plays the violin in an orchestra, as well as collecting and repairing them, so I’ll ask him when I see him at Christmas, if I remember. In fact, I did a quick search on violin making, and the first one I came to, http://www.centrum.is/hansi/construction.html , mentioned that the front and back of the violin have to be very thin, and resonate very well! So I certainly wouldn’t pay too much attention to what the chap from Mapleshaderecords says. It sounds as if he likes the colouration that resonating woods like maple introduce. His rubbish about how if you don’t have his miraculous speaker cables, your $2000 speakers can sound like $100 ones is just that – rubbish which is designed to part wealthy, gullible people from their money. They may very well make your speakers sound better, but the difference wouldn’t be equivalent to spending $1900 more on your speakers, as he seems to imply! No doubt if he gave the cables to a hi-fi reviewer and promised to advertise with them, they’d say how much different they make speakers sound, but then they’re hardly impartial, are they? He also says that long speaker cables are better than short ones. Obviously the electrical engineering that I was taught about making wires as short as possible to minimise resistance was wrong! And directional wires?? Obviously they wouldn’t be any good at passing AC signals then – maybe they’re for DC power supplies? Don’t waste your time looking at his site. It looks to me as though he’s got little in the way of engineering knowledge, so he resorts to making things up to try and sound knowledgeable. His website is a combination of truths, half-truths, sheer rubbish, and advertising. Sometimes all in the one sentence! It would be funny if it wasn’t so misleading to hi-fi buffs who have little engineering knowledge.
Alright, I’ve had my rant and I feel better – now back to practicalities. Many hi-fi rack manufacturers isolate their racks by sitting the shelves on vibration isolating pads, such as rubber, foam or other materials. It helps to also have a relatively non-resonant material to make it out of – many make them out of glass, which resonates at a quite high frequency, or out of MDF, which is less resonant than most natural wood. That’s why virtually all speaker manufacturers make speakers out of MDF or similar materials. The MDF is less resonant because it is wood that’s been broken up into very small woodchips, then glued and compressed back together, rather than having a nice naturally resonant grain running through it, like maple, oak, eucalypt or any other tree wood! Whether it makes much difference to an amplifier is debatable, but under an electro-mechanical turntable, non-resonant and de-coupled from the environment is best. Resting your turntable on bubble wrap is probably good, if it’s several layers of bubble wrap. Using two bicycle tubes, inflated to a very low pressure, under a shelf resting on them, is another idea I’ve heard, and there is a commercial anti-vibration shelf using that idea being marketed, although it’d be cheaper to make your own.
And dnsey, the reason why many people prefer open racks rather than closed racks is probably to provide good cooling for electronic equipment, particularly high power amps, which get hot when working hard. It may make sense to keep sound waves away from things like turntables, but most electronic equipment is more reliable if it's kept relatively cool.
*applause for mosfet!* ... some common sense! I agree. You said much of what I was thinking but managed (this time) to restrain myself from ranting about!
the reason why many people prefer open racks rather than closed racks is probably to provide good cooling for electronic equipment
That certainly makes sense, but it's often purportedly for the sake of the sound - certainly a number of rack manufacturers (naturally) suggest that an open rack sounds better.
I'm as sure as it's possible to be about such things that I can hear the difference when some amplifiers are used on various supports, but to me an open rack sounds worse than a closed arrangement.
My system is well ventilated by a 'shaft' at the back of the cabinet, which vents indirectly at top and bottom, so cooling isn't a problem (the exception is the CD player (a TEAC) which works better warm, so it's more or less totally enclosed.
dnsey said:
I'm as sure as it's possible to be about such things that I can hear the difference when some amplifiers are used on various supports, but to me an open rack sounds worse than a closed arrangement.
I remember seeing an interview with an engineer who was a designer with NAD, who said that suspension was desirable in CD players, and he could prove it by showing spectrum analysis, which showed a distortion component when the suspension was jammed, which disappeared when it was floating. I can believe that, but I don't know why an amplifier would improve when it was isolated from vibration. I'm not discounting it - maybe the vibration has an effect at the molecular (electron) level? It doesn't hurt to have things isolated from vibration, and it's relatively cheap and easy to do.
dnsey said:
I'm as sure as it's possible to be about such things that I can hear the difference when some amplifiers are used on various supports, but to me an open rack sounds worse than a closed arrangement.
After a sleep, I thought of the reasons an amplifier, or other electronic audio gear, may perform differently when isolated from vibration, without thinking about the molecular level. Wiring, including that in inductors, point to point wiring, component leads, or even maybe PCB’s, may change inductance and capacitance very slightly when moved around. It may only be subtle, but it could have some effect on the sound.
The other thing I thought of was valve amplifiers. I should have thought of them, as someone with a part time hobby collecting, restoring and servicing vintage radios, but I only thought of solid state amps. Valve amplifiers will definitely change sound, due to microphonic effects in the valves. Some valves are more prone to it than others, but it is something that often gets worse with age. A former colleague of mine when I worked for an electrical engineering company used to be a fellow hi-fi enthusiast, and was a valve amplifier lover. He used to run them in another room away from his speakers to lessen the effects of microphonic changes to the valves when subjected to vibration.
So there are some reasons to have racks free of vibration, and possibly enclosed, as long as cooling is OK. However, enclosing a rack totally can mean that the rack structure is subjected to more vibration, due to an increased surface area being acted upon by direct sound waves! That may be why some rack manufacturers say open racks sound better than totally enclosed ones.
Capacitors at least have some amount of microphony, some ceramics are actually piezo-electric. Even plastic film caps make noise if you knock them on very sensitive preamp. And same goes for coaxial cable, moving or tapping cable makes noise, altough vvvvery low level. (something like -150dbV)MosfetOwner said:
Wiring, including that in inductors, point to point wiring, component leads, or even maybe PCB’s, may change inductance and capacitance very slightly when moved around. It may only be subtle, but it could have some effect on the sound.
There are actually "low noise" cables intented for instrumentation purposes and so on.
Vibration isolation.
I like the float it over rare earth magnet approach, use ropes to hold it in place over them.
I like the float it over rare earth magnet approach, use ropes to hold it in place over them.
Hello all,
If you put an isolation platform under a component like a cd player, and said isolation platform was one designed for use with an electon microscope, and then experimented with different types of feet between the component and the iso platform, you'd get one tonality per type of foot... So even a stupidly expensive isolation platform isn't going to stop the effects of the vibrations the equipment is designed to foster in the first place (music).
There are several energy paths for the vibrations to get into the equipment other than through the feet. The interconnects, the power cord, and the air.
You can't stop vibrations from getting to the quipment, period. Any attempt to do so is doomed to failure. If you must consider vibrations to be like sewage, consider this. What is the difference between pouring a cup of sewage into a barrel of apple cider, or pouring in a quart of sewage? I'd say it didn't make a diference. So if you reduce by 25% the "sewage" you pour into the barrel, you still wind up with a barrel of sewage, diluted, but still sewage.
There are many great sounding systems that don't have spikes or cones or isolation devices. No sewage there. For this reason I don't consider vibrations to be a "problem" unless it's the classic case of a turntable needing better isolation.
Stands certainly affect the tone of the system. Every stand I've ever used or made did, in a big way. Right now I'm using 1" allthread with painted MDF shelves. The MDF sucks out highs, and the allthread is a bit bright/harsh sounding. The two almost balance but I had to dampen some to the threads with some black cloth wound around the exposed allthread. It isn't the prettiest solution I could have found, but it was quick and cheap.
FWIW, I wrote a white paper some years ago about the sound of different feet. (I don't sell feet or shelves.) It was even published once or twice. http://www.vansevers.com/tweak.html
If you put an isolation platform under a component like a cd player, and said isolation platform was one designed for use with an electon microscope, and then experimented with different types of feet between the component and the iso platform, you'd get one tonality per type of foot... So even a stupidly expensive isolation platform isn't going to stop the effects of the vibrations the equipment is designed to foster in the first place (music).
There are several energy paths for the vibrations to get into the equipment other than through the feet. The interconnects, the power cord, and the air.
You can't stop vibrations from getting to the quipment, period. Any attempt to do so is doomed to failure. If you must consider vibrations to be like sewage, consider this. What is the difference between pouring a cup of sewage into a barrel of apple cider, or pouring in a quart of sewage? I'd say it didn't make a diference. So if you reduce by 25% the "sewage" you pour into the barrel, you still wind up with a barrel of sewage, diluted, but still sewage.
There are many great sounding systems that don't have spikes or cones or isolation devices. No sewage there. For this reason I don't consider vibrations to be a "problem" unless it's the classic case of a turntable needing better isolation.
Stands certainly affect the tone of the system. Every stand I've ever used or made did, in a big way. Right now I'm using 1" allthread with painted MDF shelves. The MDF sucks out highs, and the allthread is a bit bright/harsh sounding. The two almost balance but I had to dampen some to the threads with some black cloth wound around the exposed allthread. It isn't the prettiest solution I could have found, but it was quick and cheap.
FWIW, I wrote a white paper some years ago about the sound of different feet. (I don't sell feet or shelves.) It was even published once or twice. http://www.vansevers.com/tweak.html
... That’s why a number of turntable manufacturers back in the 1970’s, such as Linn, Thorens and AR had better sounding turntables than ones with no suspension, because their suspension cancelled out most of the vibration from the speakers getting back to the stylus of the turntable. ... The way to stop turntable motor vibration from getting back to the stylus is by having the tonearm and platter decoupled from the motor on their own floating base, by a suspension system, like Linn (Sondek) or other belt drive turntables often do; or decoupling the motor via rubber mountings, as Rega (Planar 3) and many other manufacturers, including many Japanese belt drives, used to do; or making the motor relatively vibrationless, as Rega (P3/5/7) do now, or as the Japanese (like Technics) do with their low (platter) speed, direct drive motors (e.g. Technics SL-1200).
Technics SL-1200 (and all the SL-series tables;eg SL-1100, ~1300, ~1350, ~1400, ~1500) were/are floating suspension turntables.
With reference to the AR turntable, we used to demonstrate them at our store thusly:
Place record on turntable. Select handy preamp. Fire up the Bryston 4B plugged into Klipsh LaScalas, and gently drop the stylus into the groove. Replace the dust cover on the AR (it was a lift-on, lift-off affair of some kind of clear plastic). Rotate the big knob on the preamp until the customer is visibly alarmed at the volume level.
Take 22 ounce framing hammer, which was hidden nearby. Invite customer to hit the dust cover while the music is playing at stadium volume level.
Note: there is little danger you will not reach the volume level where the customer is visibly alarmed ... 250 watts per channel into LaScalas won't quit before your ears will, guaranteed, and I've never known a driver in those babies to be damaged by the application of power ... we did replace a few crossovers, though, but not more than about five, and we sold HUNDREDS of LaScalas, some for sound reinforcement).
Customer is suitably amazed. We are not.
Take hammer from customer, and replacing his gingerly applied taps with multiple solid hits just under the level, from experience, we know will break the dust cover; roughly equal an amount that is greater than the level you would use to set a 3 1/2 inch coated nail into the new stud wall you are framing, but less than you would use to set it home with the third (sometimes fourth, if you were hung over that day on the framing crew) whack. If it takes you five or more whacks to drive such a nail, yeah, about that hard.
Not a peep from the speakers, save for the continuation of the selected track at the previously set ridiculous volume level. You can hear the idler wheel on the rim of the platter between tracks, but you can't get that thing to jump.
Smile at customer.
You (not the customer ... too much expensive stuff too close by) could also lower the volume, remove the dustcover, reset the volume, and tap about the table with said hammer, carefully, of course, but only to protect the spinning platter, tonearm, and the usual things in danger of damage with a hammer swinging about. No need to take care whacking the plinth, however. Have at 'er.
Now, the AR had a tonearm that you could probably use as a hammer, and the low-mass tonearm/high compliance cartridge that appeared in the mid 70's starting with, in my experience, the original ADC XLM, presented problems with this kind of vibration that the AR never had to worry about, but still ... it was pretty effective isolation.
Last edited:
" ... You can hear the idler wheel on the rim of the platter between tracks, but you can't get that thing to jump. ..."
My bad. But you could hear something coming from the drive. Maybe bearing noise.
And, of course, apologies for the Lazarus. i was searching "audio racks".
My bad. But you could hear something coming from the drive. Maybe bearing noise.
And, of course, apologies for the Lazarus. i was searching "audio racks".
Last edited:
Isolating vibrations from equipment
I built a cabinet that is completely non-resonant (the cabinet is filled with sand and rests on a separate
concrete foundation. The lower the frequencies produced by subwoofers the more difficult it is to
get complete isolation. I have a Eminent Technology
rotary subwoofer that goes down to below 1 hz and this method works extremely well.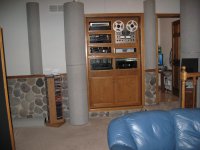
Or at least I will...
I made the one have when I was 15, but my metal and woodworking skills have drastically improved over the past five years...
I am building it out of four shelves(haven't decided whether I want white oak or mahogany), and rather than constructing the whole thing out of wood, I have four "four-foot" lengths of 6061 aluminum roundstock which will act as the support poles. each corner of every shelf will have a hole drilled in it, and the shelves will be supported on the Al poles with a steel collar under every corner.
Instead of setting the whole thing on heavy feet w/carpet-piercing spikes, I'm going to machine a spike on the end of each pole.
Which wood is better for vibration isolation? I have heard claims that air-dryed maple is the absolute best(since they use it to make musical insturments), but it is not readily available, and is outrageously expensive.
Has anybody else made their own rack?
-Trevor
PS- I would like to use brass roundstock, but it's considerably more expensive than aluminum
I built a cabinet that is completely non-resonant (the cabinet is filled with sand and rests on a separate
concrete foundation. The lower the frequencies produced by subwoofers the more difficult it is to
get complete isolation. I have a Eminent Technology
rotary subwoofer that goes down to below 1 hz and this method works extremely well.
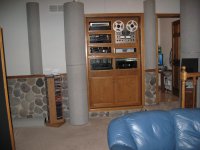
Made for my need's
Hi guy's i had this rack made for my need's so this is not for everyone i wanted something strong heavy & good looking and it had to be small all i have is two pieces for audio & two pieces for tv here is what my friend came up with he usualy uses wood for his shelves i wanted granite total weight is 300 pounds and it is on a cement floor.
Hi guy's i had this rack made for my need's so this is not for everyone i wanted something strong heavy & good looking and it had to be small all i have is two pieces for audio & two pieces for tv here is what my friend came up with he usualy uses wood for his shelves i wanted granite total weight is 300 pounds and it is on a cement floor.




Last edited:
- Status
- Not open for further replies.
- Home
- Design & Build
- Construction Tips
- Build your own stereo rack!