I have been working with Corian counter top material for a few days now, cutting out pieces for my turntable project. So far I’ve learned a few things I can share.
First off, not all Corian is created equally…I discovered the more solid the color, the denser the material. Of the pieces I have to play with, the solid cream color is the densest, and the “granite” is the least dense. I assume this is due to the “texturing” bits mixed in isn’t as dense as the base material…just a guess.
As anybody who has priced it knows, Corian is freakin’ expensive!! The shop I got mine from originally quoted my brother (who works there) $70.00 a square foot for ½ inch thick stock. Fortunately there is an alternative for table builders…sink cutouts. Any shop that works with Corian ends up with a stack of oval pieces left over from the sink holes. This stuff is unusable to the shop for a couple of reasons 1) the odd shape and sizes, and 2) as the stuff is so expensive, the stock is ordered as the job comes in…the odds of having more than a couple of pieces the same color is astronomical.
Bottom line, you can probably find a shop that will either give it to you, or sell it for a song. My total cost was $0.00 J
This stuff is heavier than MDF and acoustically more inert. I think it holds a lot of promise as a table material.
Below is a couple pictures of the table pieces I’ve cut out for the platter and top plinth. Its rough cut, I’ll finish it up after the pieces are laminated. The patter consists of four Corian pieces interleaved with three sheets of lead (weighs around 25-30 lb), and the plinth is Corian, lead, extruded aluminum plate, lead, Corian.
I will be test laminating this weekend with some scraps by gluing with epoxy under clamped pressure.
As always.. comments are solicited.
Casey
First off, not all Corian is created equally…I discovered the more solid the color, the denser the material. Of the pieces I have to play with, the solid cream color is the densest, and the “granite” is the least dense. I assume this is due to the “texturing” bits mixed in isn’t as dense as the base material…just a guess.
As anybody who has priced it knows, Corian is freakin’ expensive!! The shop I got mine from originally quoted my brother (who works there) $70.00 a square foot for ½ inch thick stock. Fortunately there is an alternative for table builders…sink cutouts. Any shop that works with Corian ends up with a stack of oval pieces left over from the sink holes. This stuff is unusable to the shop for a couple of reasons 1) the odd shape and sizes, and 2) as the stuff is so expensive, the stock is ordered as the job comes in…the odds of having more than a couple of pieces the same color is astronomical.
Bottom line, you can probably find a shop that will either give it to you, or sell it for a song. My total cost was $0.00 J
This stuff is heavier than MDF and acoustically more inert. I think it holds a lot of promise as a table material.
Below is a couple pictures of the table pieces I’ve cut out for the platter and top plinth. Its rough cut, I’ll finish it up after the pieces are laminated. The patter consists of four Corian pieces interleaved with three sheets of lead (weighs around 25-30 lb), and the plinth is Corian, lead, extruded aluminum plate, lead, Corian.
I will be test laminating this weekend with some scraps by gluing with epoxy under clamped pressure.
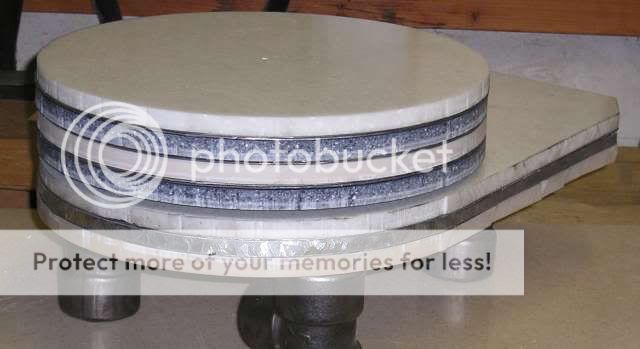
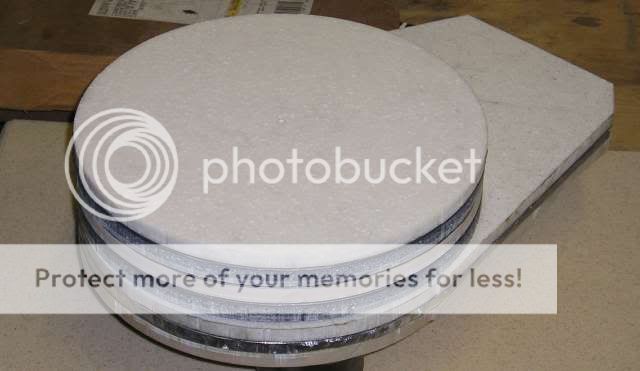
As always.. comments are solicited.
Casey
A more complete mockup with 2 of the base pieces I cut out tonight..the "Clover" can is of course standing in for the motor housing...
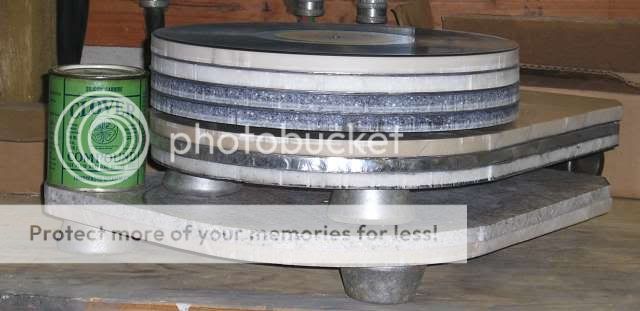
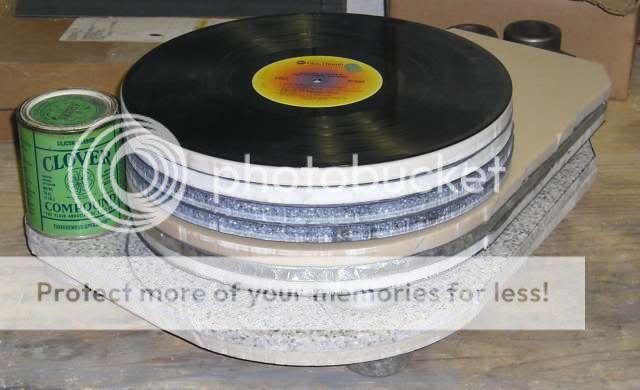
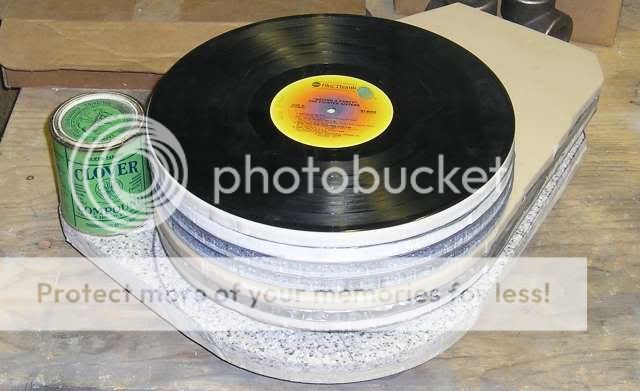
Very nice work.😉
What are you using for a bearing? What did you end up using for glue?
Looks like it is going to be fantastic.
Dave
What are you using for a bearing? What did you end up using for glue?
Looks like it is going to be fantastic.
Dave
Very nice work.
Thank you

What are you using for a bearing?
I'm still working on the design. It will be an inverted bearing designed around this Tungsten Carbide ball and this Moybdenum filled Nylon as the thrust plate. I plan to run a dry graphite for the sleeve lubrication.
What did you end up using for glue?
I'm still testing the epoxy...looks good so far. See herefor the details..
http://www.diyaudio.com/forums/showthread.php?postid=757103#post757103
Casey
Cool project.
I made a corian plynth by gluing two pieces of corian together. I am happy with the results. I did not make a corian platter though, don't think I could have made it nice and round like you did.
Randy
I made a corian plynth by gluing two pieces of corian together. I am happy with the results. I did not make a corian platter though, don't think I could have made it nice and round like you did.
Randy
I made a corian plynth by gluing two pieces of corian together. I am happy with the results.
I checked out your table..nice job..I really wish I had consistently colored Corian. I have no less than five different colors/shades. Beggers can't be choosers though. I'll have to cover it when I'm done..to bad..Corian finishes out great.
Did you have a chance to listen before and after the Corian plinth..if so how did the Corian change the sound?
I did not make a corian platter though, don't think I could have made it nice and round like you did.
It's actually pretty rough right now. I cut the discs out with a Dremel tool with the circle cutting attachment and a spiral cut blade..slow going. The trick will be getting a precision edge. I have a good idea how to do it though and will cover it when I get to that point.
Casey
Hi
I never did listen to it in it's original form, as an Empire 208 with an aluminum plinth. I would have had to drill out a new hole in the aluminum to mount my rega arm, which I never did. I decided to make the corian plinth instead.
Randy
I never did listen to it in it's original form, as an Empire 208 with an aluminum plinth. I would have had to drill out a new hole in the aluminum to mount my rega arm, which I never did. I decided to make the corian plinth instead.
Randy
Weekend Progress report…
First up is a piece I call “The Joy Of Chain Drilling”…..
…man I need a band saw. The pieces have a sheet of lead between them and go between the Corian on the bottom plinth.
I made some parts to my bearing…
… if you want to see micro scratches in a metal surface, hit it with a camera flash. The spindle has a mirror finish to the naked eye. The bearing bronze sleeve has a clearance of .0005”, and spins freely on the spindle. I machined the spindle out of a ¾” drive socket extension, then press fit it (with a touch of JB Weld) into the aluminum flange.
Here it is sitting in the top plinth…
…you can also see the aluminum I cut out for the bottom plinth.
I am scheduled to receive my ¼” Tungsten Carbide ball and the self-lubricating nylon later this week, I’ll be finishing up the bearing assembly then.
I’m tired…going to bed.
Casey
First up is a piece I call “The Joy Of Chain Drilling”…..
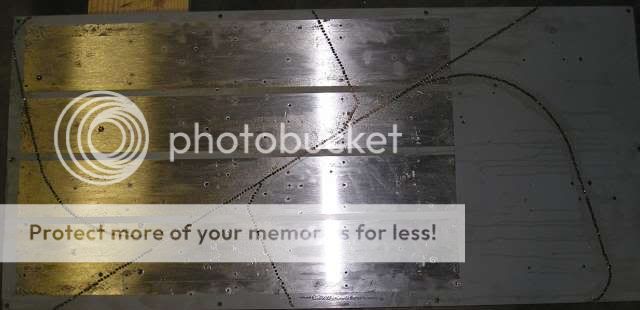
…man I need a band saw. The pieces have a sheet of lead between them and go between the Corian on the bottom plinth.
I made some parts to my bearing…
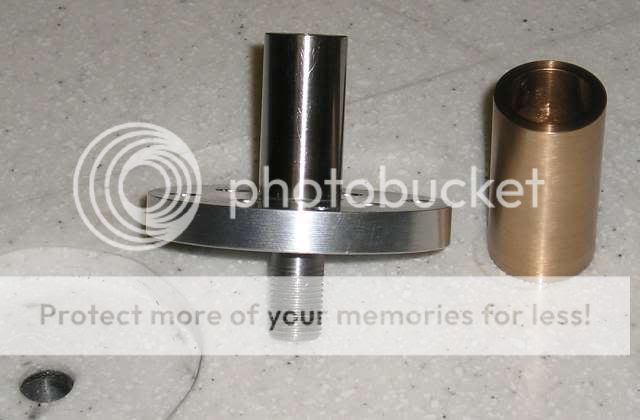
… if you want to see micro scratches in a metal surface, hit it with a camera flash. The spindle has a mirror finish to the naked eye. The bearing bronze sleeve has a clearance of .0005”, and spins freely on the spindle. I machined the spindle out of a ¾” drive socket extension, then press fit it (with a touch of JB Weld) into the aluminum flange.
Here it is sitting in the top plinth…
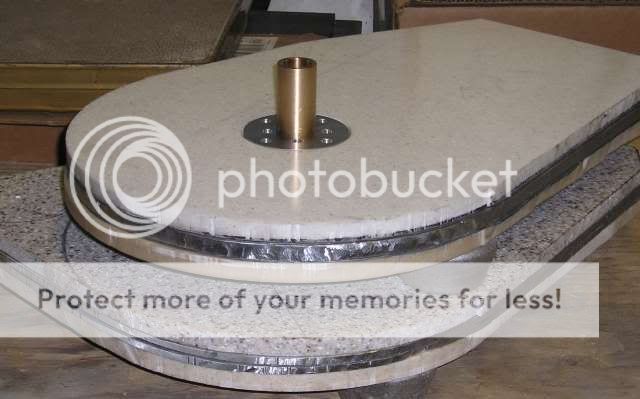
…you can also see the aluminum I cut out for the bottom plinth.
I am scheduled to receive my ¼” Tungsten Carbide ball and the self-lubricating nylon later this week, I’ll be finishing up the bearing assembly then.
I’m tired…going to bed.
Casey
The bearing is finished …
…the piece at the bottom of the top photo is the alignment jig I used to center the ball on the spindle during gluing. I machined a hole .27” in dia. And .135” deep in the top of the spindle. I set the jig on my bench and dropped the ball in so that it set in the center hole, I then filled the hole in the spindle ½ way with J-B Weld and pushed it in the jig on top of the ball. I then inverted the two pieces and clamped till dry…perfectly centered.
The bottom photo shows the bearing assembly over the spindle with the cap off. The black disc in the center of the cap is a .125” thick piece of Molybdenum impregnated Nylon. The Tungsten Carbide ball rides on this.
The platter is mostly assembled…
…the top photo shows the basic construction of the platter in more detail. The bearing housing was wrapped in lead sheeting, and the individual discs that make up the platter were fitted until I could just tap the pieces down.
The second picture shows the whole assembly clamped while curing. I actually did this in two steps. I laminated the bottom two pieces and its lead discs first, I then tapped out the housing and cleaned up any epoxy ooze and let it cure. I re-greased the housing, tapped it back in and finished the lamination.
The top plinth is also laminated and curing as I type this.
The action shot…
…as smooth and quite as anybody could hope for. Unleveled (sitting on a piece sitting on a garbage can) , unbalanced, and with a heavy oil consisting of a 50-50 mix of 30wt motor oil and Marvel Mystery Oil, it spun for over two minutes after spinning it up to around 78 rpm. The real (pleasant) surprise was when it stopped, it then spun backwards a quarter turn…it found the heavy spot on around a 2 deg. angle!! I repeated this a few times and it came to rest at approx. the same point each time. Once the bearing is ran in, with the proper light oil I expect it to do much better.
I decided to go with 5 layers instead of 4 on the platter. I will be working on the top section with the record spindle next.
Casey
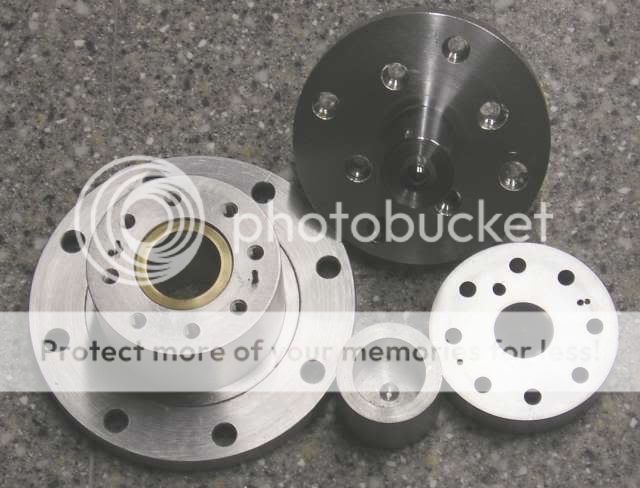
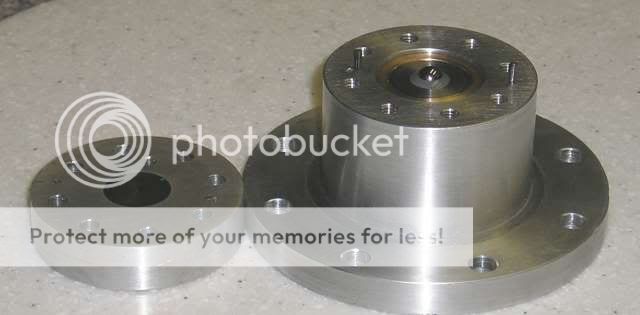
…the piece at the bottom of the top photo is the alignment jig I used to center the ball on the spindle during gluing. I machined a hole .27” in dia. And .135” deep in the top of the spindle. I set the jig on my bench and dropped the ball in so that it set in the center hole, I then filled the hole in the spindle ½ way with J-B Weld and pushed it in the jig on top of the ball. I then inverted the two pieces and clamped till dry…perfectly centered.
The bottom photo shows the bearing assembly over the spindle with the cap off. The black disc in the center of the cap is a .125” thick piece of Molybdenum impregnated Nylon. The Tungsten Carbide ball rides on this.
The platter is mostly assembled…
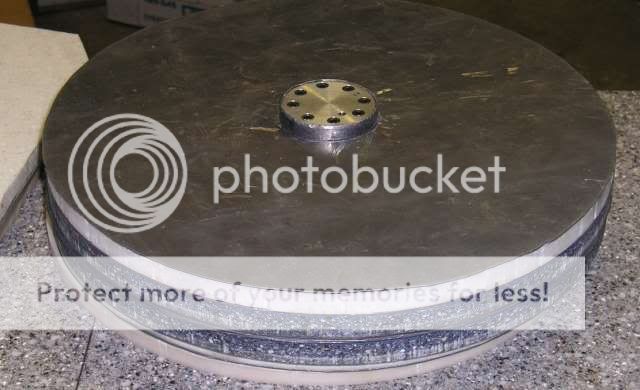
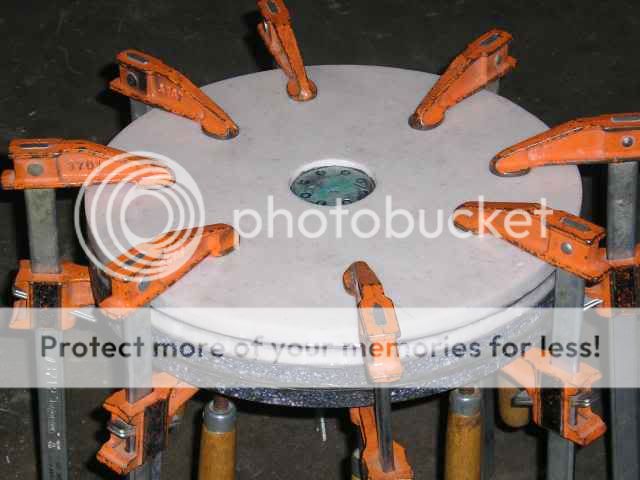
…the top photo shows the basic construction of the platter in more detail. The bearing housing was wrapped in lead sheeting, and the individual discs that make up the platter were fitted until I could just tap the pieces down.
The second picture shows the whole assembly clamped while curing. I actually did this in two steps. I laminated the bottom two pieces and its lead discs first, I then tapped out the housing and cleaned up any epoxy ooze and let it cure. I re-greased the housing, tapped it back in and finished the lamination.
The top plinth is also laminated and curing as I type this.
The action shot…
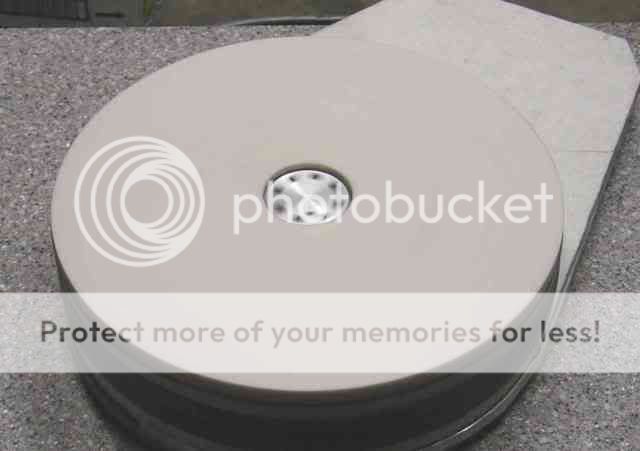
…as smooth and quite as anybody could hope for. Unleveled (sitting on a piece sitting on a garbage can) , unbalanced, and with a heavy oil consisting of a 50-50 mix of 30wt motor oil and Marvel Mystery Oil, it spun for over two minutes after spinning it up to around 78 rpm. The real (pleasant) surprise was when it stopped, it then spun backwards a quarter turn…it found the heavy spot on around a 2 deg. angle!! I repeated this a few times and it came to rest at approx. the same point each time. Once the bearing is ran in, with the proper light oil I expect it to do much better.
I decided to go with 5 layers instead of 4 on the platter. I will be working on the top section with the record spindle next.
Casey
Another weekend workin’ on the table.
First I drilled and tapped the holes to secure the bearing, and laminated the last lead/Corian layer to the platter. The rest of my time was spent on the record spindle assembly…
…you may wonder why all the trouble of separating the record spindle from the bearing assembly, after all it is a heck of a lot easier to have the spindle simply extend off the bearing. Well, first and most importantly, it isolates the spindle (the first contact to the album) from any residual bearing noise. Secondly, by having the spindle removable, I have service access to the bearing for oiling, ect.. Finally, it provides an adjustable air break/trap to the bearing. By removing it, it relieves the vacuum that occurs when taking off the platter, and when installing the platter it will be a nice control for adjusting the descent onto the bearing spindle. It also provides a vacuum lock to keep the oil in the bearing. I install the platter with the bearing more or less dry, put a few drops of oil in the oil hole, spin it a little to spread the oil then screw the spindle in. This vapor locks the oil into the bearing, preventing it from running out.
It’s starting to look real…
… the record “mat” is in fact a record. I am working on a method to sand it true flat, and to get a gloss surface…we’ll see.
Next up..tooling up my milling machine converted from a drill press to do the final platter diminsioning. Good thing I have a long weekend coming up 🙂
Casey
…
First I drilled and tapped the holes to secure the bearing, and laminated the last lead/Corian layer to the platter. The rest of my time was spent on the record spindle assembly…
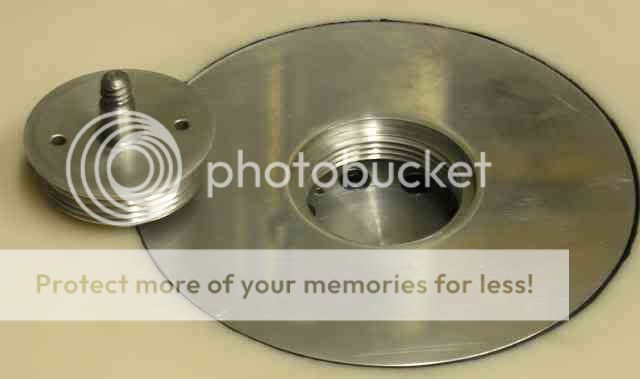
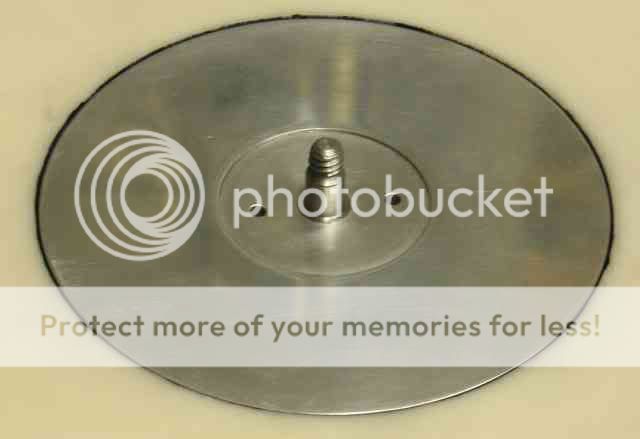
…you may wonder why all the trouble of separating the record spindle from the bearing assembly, after all it is a heck of a lot easier to have the spindle simply extend off the bearing. Well, first and most importantly, it isolates the spindle (the first contact to the album) from any residual bearing noise. Secondly, by having the spindle removable, I have service access to the bearing for oiling, ect.. Finally, it provides an adjustable air break/trap to the bearing. By removing it, it relieves the vacuum that occurs when taking off the platter, and when installing the platter it will be a nice control for adjusting the descent onto the bearing spindle. It also provides a vacuum lock to keep the oil in the bearing. I install the platter with the bearing more or less dry, put a few drops of oil in the oil hole, spin it a little to spread the oil then screw the spindle in. This vapor locks the oil into the bearing, preventing it from running out.
It’s starting to look real…
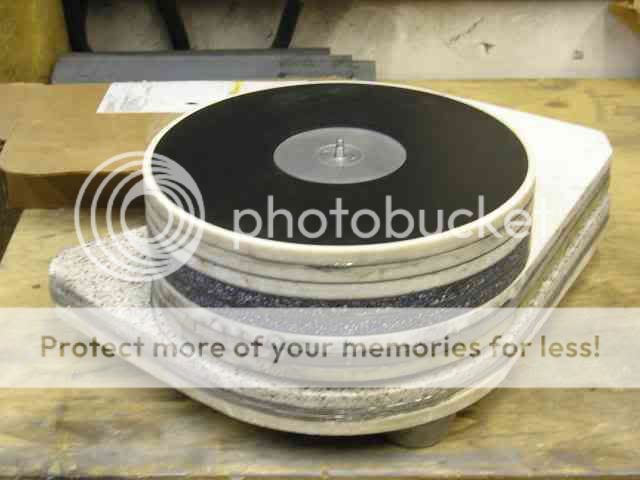
… the record “mat” is in fact a record. I am working on a method to sand it true flat, and to get a gloss surface…we’ll see.
Next up..tooling up my milling machine converted from a drill press to do the final platter diminsioning. Good thing I have a long weekend coming up 🙂
Casey
…
The load time is getting to long..I'm bumping to get to the next page so I can post my latest progress.
Well I guess the bump wasn't needed 🙂
We’ll, I took full advantage of my long weekend and made the tools I needed to machine my platter. If I had access to a lathe large enough to swing a 12” platter it would have been a simple matter to true it up..I don’t, and it wasn’t. All operations were done using its own bearing on my modified drill press. DO NOT try any of this with a stock press and a chuck, not only would the results stink, you’ll end up being fed thru a tube.
First I cludged together a base to mount my spindle to the X-Y table on my press…
…it’s not pretty, but it is functional. Next I epoxied a stack of Corion discs together and made a precision sanding drum with a jacobs taper to match my press spindle for mounting. I glued 80 grit sand paper to it and trued up the edge…
…I also made a sander to grind my belt groove. Next up was the top. I surfaced the patter with a .375 end mill in a collet chuck I made for my press…
…I wasn’t sure my bearing would be sturdy enough for this, I shouldn’t have worried…this is not your fathers turntable bearing. I was amazed at just how little the platter vibrated during this. I do believe my lead/Corion lamination would go in the “good idea” column.
Next was chamfering the top edge, as well as the belt groove edges…
…this wasn’t absolutely necessary but it sure looks nice. Here is the fruits of my labor…
…you can see the groove grinder to the right of the platter. As luck would have it, the lead in the groove loaded up the sand paper, causing the groove to be slightly curved, so I skinned it with epoxy and will do a final grind with 220 grit sand paper as soon as it cures (tomorrow).
I have been inspecting and cleaning the bearing through the course of this work. The only effect I can see is the apparent accelerating of the break-in period. Whether it’s the ran-in bearing, or the balancing effect of truing up the platter, the thing is spinning amazingly now. I haven’t timed it, but I’m sure it’s spinning longer. The most noticeable improvement is the slow spinning. It just creeps along .
Next Up…the reflex clamp. Stay Tuned.
Casey
We’ll, I took full advantage of my long weekend and made the tools I needed to machine my platter. If I had access to a lathe large enough to swing a 12” platter it would have been a simple matter to true it up..I don’t, and it wasn’t. All operations were done using its own bearing on my modified drill press. DO NOT try any of this with a stock press and a chuck, not only would the results stink, you’ll end up being fed thru a tube.
First I cludged together a base to mount my spindle to the X-Y table on my press…
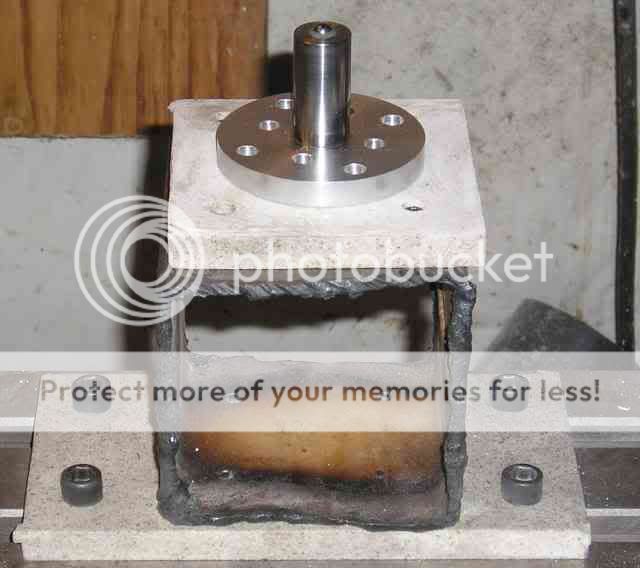
…it’s not pretty, but it is functional. Next I epoxied a stack of Corion discs together and made a precision sanding drum with a jacobs taper to match my press spindle for mounting. I glued 80 grit sand paper to it and trued up the edge…
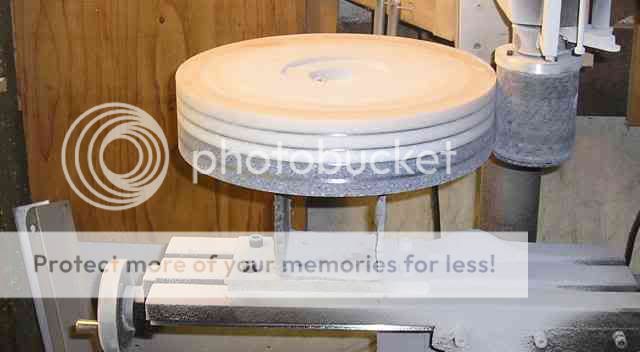
…I also made a sander to grind my belt groove. Next up was the top. I surfaced the patter with a .375 end mill in a collet chuck I made for my press…
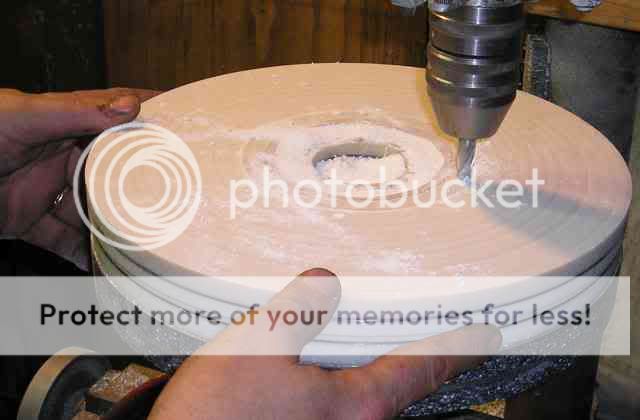
…I wasn’t sure my bearing would be sturdy enough for this, I shouldn’t have worried…this is not your fathers turntable bearing. I was amazed at just how little the platter vibrated during this. I do believe my lead/Corion lamination would go in the “good idea” column.
Next was chamfering the top edge, as well as the belt groove edges…
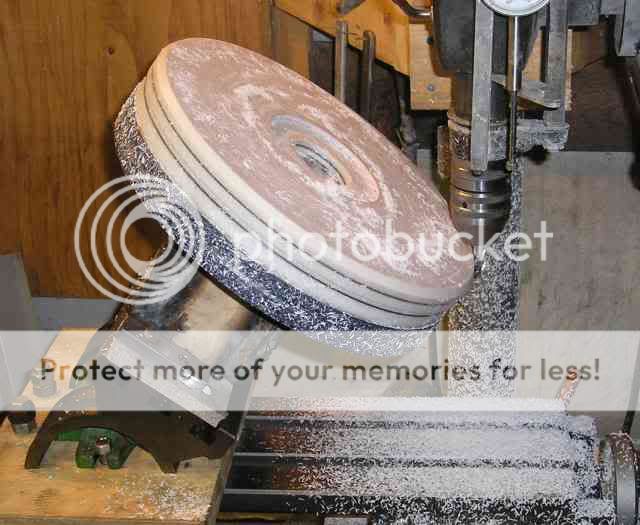
…this wasn’t absolutely necessary but it sure looks nice. Here is the fruits of my labor…
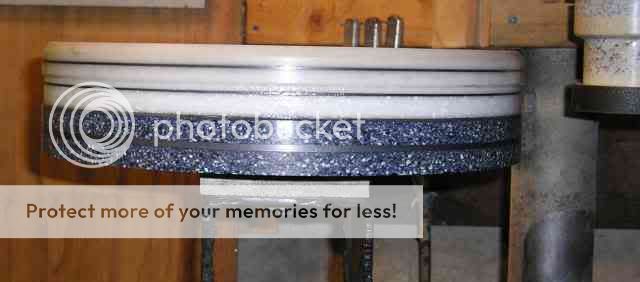
…you can see the groove grinder to the right of the platter. As luck would have it, the lead in the groove loaded up the sand paper, causing the groove to be slightly curved, so I skinned it with epoxy and will do a final grind with 220 grit sand paper as soon as it cures (tomorrow).
I have been inspecting and cleaning the bearing through the course of this work. The only effect I can see is the apparent accelerating of the break-in period. Whether it’s the ran-in bearing, or the balancing effect of truing up the platter, the thing is spinning amazingly now. I haven’t timed it, but I’m sure it’s spinning longer. The most noticeable improvement is the slow spinning. It just creeps along .
Next Up…the reflex clamp. Stay Tuned.
Casey
I finished up the belt groove, and learned a lesson I won’t soon forget…Don’t use epoxy as a filler!! I thought the lead loaded up the sandpaper quickly, compared to epoxy it’s a joy to work with. I wasn’t grinding for more than 10 sec. before the paper was useless. So after several paper changes I finally got back down to the base materials, once the epoxy was removed I was able to get a flat surface by alternating between light pressure on my grind wheel,and lightly running a file a couple times around the groove to knock off the lead ridge. This worked out great. The groove is ruler flat with a run-out of .00075”. On a 11.7” circle (the diameter of the belt groove) this works out to .0064% off of perfect…I’ll take it. Now, this number will get better or worse after I repeat the groove sanding after I paint it, but I’m in the zone.
Onward thru the fog…
Casey
Onward thru the fog…
Casey
Very impressive! You want to make me one? Give ya $20!
😉
Are you going to DIY a tonearm for it? Some of the unipivot types are quite appealing to DY, with exotic tubing available in the form of arrow shafts.
😉
Are you going to DIY a tonearm for it? Some of the unipivot types are quite appealing to DY, with exotic tubing available in the form of arrow shafts.
Very impressive! You want to make me one? Give ya $20!
Tempting offer, let me think for a moment...uhhhhhh...NO! 😀
Are you going to DIY a tonearm for it?
Yup..a air bearing linear tracker design I've been working on, sort of a Ladegaard/Rockport love child. The need for a serious test bed was the actual motivation for this project ( well, that and a serious desire for some sweet, sweet analog).
Thank you for the response Mr. badman, in spite of the considerable volume of views of this thread, I've had very few comments...kind of a lonely fishbowl feeling here.
Casey
Indeed, I wanted to reply BECAUSE nobody else was. Normally such work gets a lot of replies, but in your case... what's to say without getting one's nose all brown?
The whole durned thing looks like what I'd do..... if I had a couple months and all the tooling..... that you did some of it by hand or adapted existing tooling to the project makes it all the more impressive. Please post your results with your tonearm, and with your listening, I'm mighty impressed.
Btw, I'll up the offer to $40 🙂

The whole durned thing looks like what I'd do..... if I had a couple months and all the tooling..... that you did some of it by hand or adapted existing tooling to the project makes it all the more impressive. Please post your results with your tonearm, and with your listening, I'm mighty impressed.
Btw, I'll up the offer to $40 🙂
I decided to post a better picture of the platter. It was just to visually disjointed with the different colors and lines to really see the machined profile, so I hit it with a quick coat of sandable primer to get this picture....
...ahhh, thats better 🙂
Casey
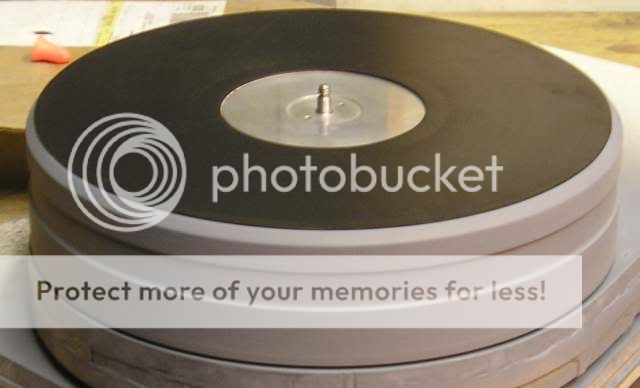
...ahhh, thats better 🙂
Casey
valveitude said:...ahhh, that's better 🙂
Yesm... lookin' more of a who;e now, and the beauty is showing thru....
dave
Hi Dave,
Thank you, I think so to. I said I was going to do the reflex clamp next, but I may just work on the plinth first. It would be quicker gratification to see it take physical shape...I guess I'll just have to see how the wind blows next weekend.
Casey
and the beauty is showing thru
Thank you, I think so to. I said I was going to do the reflex clamp next, but I may just work on the plinth first. It would be quicker gratification to see it take physical shape...I guess I'll just have to see how the wind blows next weekend.
Casey
Did you get a big ol floor standing drill press and put on an ebay chinese slide table to make it a milling machine? i did the exact same thing, works pretty good but it could be better, my drill is a delta and when i apply too much side force it "jumps" up and sideways, almost as if the 2 main bearings are not preloaded properly. can they even be adjusted?
thats beutiful work by the way.
thats beutiful work by the way.
- Status
- Not open for further replies.
- Home
- Source & Line
- Analogue Source
- Corian Turntable Fun