C2, C4, C6 just change them, you can't really measure with what you have.
I use Panasonic FC 12uF 100 V part no. EEUFC2A120
Dave
Thanks. I'll check to make certain they already have not been replaced and then order replacements.
-Steve
A great looking project. I am sure it will sound great. And it should be useful as a TOOL, as you suggested it is to become. Somewhat skeletal such as those plinths built by Terry Cain.
As the original poster of the Chadwick mods to your site (via aa) years ago, (and my continuing developments from my own experiences) may I suggest something that will kill fewer trees? If making from BB, please glue strips up to make the perimeter frames, as this will minimize waste (you probably have lots of scraps and off-cuts). Else I might suggest the use of hickory. It is very hard, quite dense and is very stable dimensionally if finished (and can be free if you can re-cycle old hockey sticks if anyone is still using the wooden ones).
re: plinth design. Baltic Birch in a layered glue-up. some of the pieces can be made from remnants I already have. re: carbon footprint and killing trees. these are Russian trees and I'm not certain if the Russians farm their timber the way it is done in North America. In NA commonly used timber, fir trees for example, are farmed by large corporations and can be thought of as a renewable resource.
fwiw I do avoid exotic woods which are known to be prohibited by one country or another. Example; ebony from India, Rosewood from Brazil. However, Ebony from Gabon, Africa is not yet prohibited. Same for cocobolo from Costa Rica. The cost of ebony restricts the amount that I use down to small and few pieces. I'm not really that crazy about cocobolo so I tend not to use it.
re: hickory versus baltic birch multi-ply. I like the constrained layer and grain organization within the birch ply. It is a product that tends to work well in audio related projects. And the cost is reasonable. In my area there is a plywood store a few blocks away from me that sells the Baltic Birch multi-ply. they recognize me when I walk in
-Stever
Last edited:
efficient use of resources...
Steve.
Great to see that you are not against creating a plinth with offcuts or otherwise useless pieces of scrap BB ply (I too like BB ply, but if truely sold as Baltic Birch ply, the Scandinavians have the lock on that).
I am sure you will find the BB plinth to sound very good indeed. I may take my chances on the hickory/hockey stick style if I decide to build another plinth for an idler.
If you avoid the use of all exotic woods, you help reduce the market for them, thus helping to conserve he resource (sorry if it seems I/m getting "preachy" here).
Steve.
Great to see that you are not against creating a plinth with offcuts or otherwise useless pieces of scrap BB ply (I too like BB ply, but if truely sold as Baltic Birch ply, the Scandinavians have the lock on that).
I am sure you will find the BB plinth to sound very good indeed. I may take my chances on the hickory/hockey stick style if I decide to build another plinth for an idler.
If you avoid the use of all exotic woods, you help reduce the market for them, thus helping to conserve he resource (sorry if it seems I/m getting "preachy" here).
Steve.
Great to see that you are not against creating a plinth with offcuts or otherwise useless pieces of scrap BB ply (I too like BB ply, but if truely sold as Baltic Birch ply, the Scandinavians have the lock on that).
I am sure you will find the BB plinth to sound very good indeed. I may take my chances on the hickory/hockey stick style if I decide to build another plinth for an idler.
If you avoid the use of all exotic woods, you help reduce the market for them, thus helping to conserve he resource (sorry if it seems I/m getting "preachy" here).
If I were living far enough north to be witness to the melting down of the polar ice cap, (say in the Northwest Territories) I might become very concerned about global warming. And part of this, afaik, is a result of the deforesting of planet earth. In particular, Amazon rain forest.
Even living at the latitude that I do, Seattle area, I must say the weather is getting pretty screwy in recent years. global warming? I dunno but evidence is mounting to support the notion.
Anyway, a carbon footprint can't be too large if utilizing wood products that are farmed in a responsible manner. Example, lumber taken from fir trees that are constantly being re-planted after harvest. Life cycle around 20 to 30 years. Not old growth timber.
I can't say about the Baltic Birch. Whether it be from Finland or Russia. I think the Baltic Birch region we are talking of includes timber from both of those countries. The stuff I see, I presume, is mainly exported from Russia. I would hope that these exporters are being good stewards to planet earth.
-Steve
user 501
My experience - as I think I said - was from some years ago. My arm was, I seem to remember, a 1.5 (or maybe the model before that) and it was on that basis that I made my remarks as above. From most points of view a well designed unipivot has to be preferable to any traditional ball race/multi-pivot design.
I am pleased that the 2.2 is more tunable; I had to make a Zeta style counter weight with various discs all of which were necessary to balance out the Io!
My experience - as I think I said - was from some years ago. My arm was, I seem to remember, a 1.5 (or maybe the model before that) and it was on that basis that I made my remarks as above. From most points of view a well designed unipivot has to be preferable to any traditional ball race/multi-pivot design.
I am pleased that the 2.2 is more tunable; I had to make a Zeta style counter weight with various discs all of which were necessary to balance out the Io!
user 501
My experience - as I think I said - was from some years ago. My arm was, I seem to remember, a 1.5 (or maybe the model before that) and it was on that basis that I made my remarks as above. From most points of view a well designed unipivot has to be preferable to any traditional ball race/multi-pivot design.
I am pleased that the 2.2 is more tunable; I had to make a Zeta style counter weight with various discs all of which were necessary to balance out the Io!
we can mass tune a tonearm heavier than it is but not lighter. So a medium mass arm can accept headweights and larger counterweights. Although for the Graham, we want to use the counterweights Bob Graham makes. Or at least I do. I think the Grahams we are talking about were offered for sale in two different configurations. Standard and deluxe. The deluxe kit came with some extras like the little plastic spindle pin that allowed us a really simple way to find pivot to spindle. And the overhang/zenith jig, and the auxiliary CW. Considering how I'm always moving the arm from one TT to another, I really value those extra pieces.
Anyway, it's harder to go the other direction (lower mass) except for those tonearms that offer plug in arm wands in various weights. Like some of the Moerch models.
I recall trying a Shure V15VxMR on my Graham for a while. The arm was too heavy for the Shure. Even with the "dynamic stabilizer" deployed on the Shure, it just did not seem appropriate.
On the Moerch, I wonder why some of us have not already tried a Moerch on various vintage turntables, including some idler models as well as some of the more interesting DD. Example, a Moerch DP6. Interesting about the Moerch is that their armwands are offered in two different lengths as well as various weights. So we could have a 12 inch Moerch on an SP10.
I haven't heard a Moerch, but they are very well regarded all over. If the price were right on a lightly used one.........
-Steve
I would hope that these exporters are being good stewards to planet earth.
Take a look at Ikea. They seem to be awfully efficient in the way they consume wood fibre. The Fin's are no slouches either, when it comes to processing fibre. The Russian's, maybe not so much.
jeff
Last edited:
Hi all,
I have been following this thread with great interest. It is great to see so many people with a keen interest in these old record players!
The thread inspired me to bring down my old SP-10 from the attic where it has been sitting for at least 5 years. I now want to get it up and running.
I thought I would spend an hour to clean the bearing and to get some new oil into it, and then start to play some music.
But unfortunately I discovered that the plastic thing on top of the bearing is worn down to such degree that the bare metal of the bearing shaft top is just visible
Is there anyone who has advice how to replace the worn cap (thrust plate?), and what material to use?
Nils
I have been following this thread with great interest. It is great to see so many people with a keen interest in these old record players!
The thread inspired me to bring down my old SP-10 from the attic where it has been sitting for at least 5 years. I now want to get it up and running.
I thought I would spend an hour to clean the bearing and to get some new oil into it, and then start to play some music.
But unfortunately I discovered that the plastic thing on top of the bearing is worn down to such degree that the bare metal of the bearing shaft top is just visible
Is there anyone who has advice how to replace the worn cap (thrust plate?), and what material to use?
Nils
Hi all,
I have been following this thread with great interest. It is great to see so many people with a keen interest in these old record players!
The thread inspired me to bring down my old SP-10 from the attic where it has been sitting for at least 5 years. I now want to get it up and running.
I thought I would spend an hour to clean the bearing and to get some new oil into it, and then start to play some music.
But unfortunately I discovered that the plastic thing on top of the bearing is worn down to such degree that the bare metal of the bearing shaft top is just visible
Is there anyone who has advice how to replace the worn cap (thrust plate?), and what material to use?
Nils
Hi Nils.
Can you take a photo that will give us a view of what you mean and post that to this thread?
-Steve
Hi
I made som photos of bearing shaft.
First picture shows shaft with cap. You can see how the cap has been worn through so the metal is actually showing:
http://i754.photobucket.com/albums/xx190/Myter01/2013-10-06b003_zps93a8bd16.jpg
The cap has overall approx dimensions: 2,6 mm thick and 6,7 mm wide. Not a pretty sight, the cap is worn right through!
The bare metal shaft looks like this:
http://i754.photobucket.com/albums/xx190/Myter01/2013-10-06b004_zps2bc8f612.jpg
As you can see that there is even a mark on tip of the bearing!
I would like to get a replacement cap, and I would like to open up discussion on what material to use when making a replacement.(I scanned the internet and there seems to be no replacements readily available)
There is an old thread on Audiokarma Bearing wear on an SP 10 mk II PICS - AudioKarma.org Home Audio Stereo Discussion Forums on this topic.
There is some interesting stuff in the thread but nothing conclusive. "Self repairing plastic" is mentioned, but conclusion seem to be that that was just marketing. Perhaps it is teflon or delrin?
Anyway, what would be a good material to make a new cap?
Regards
Nils
I made som photos of bearing shaft.
First picture shows shaft with cap. You can see how the cap has been worn through so the metal is actually showing:
http://i754.photobucket.com/albums/xx190/Myter01/2013-10-06b003_zps93a8bd16.jpg
The cap has overall approx dimensions: 2,6 mm thick and 6,7 mm wide. Not a pretty sight, the cap is worn right through!
The bare metal shaft looks like this:
http://i754.photobucket.com/albums/xx190/Myter01/2013-10-06b004_zps2bc8f612.jpg
As you can see that there is even a mark on tip of the bearing!
I would like to get a replacement cap, and I would like to open up discussion on what material to use when making a replacement.(I scanned the internet and there seems to be no replacements readily available)
There is an old thread on Audiokarma Bearing wear on an SP 10 mk II PICS - AudioKarma.org Home Audio Stereo Discussion Forums on this topic.
There is some interesting stuff in the thread but nothing conclusive. "Self repairing plastic" is mentioned, but conclusion seem to be that that was just marketing. Perhaps it is teflon or delrin?
Anyway, what would be a good material to make a new cap?
Regards
Nils
Last edited:
Hi!
I missed to include the Picture of the shaft with the cap still attached:
http://i754.photobucket.com/albums/xx190/Myter01/111_zps164b1c36.jpg
I missed to include the Picture of the shaft with the cap still attached:
http://i754.photobucket.com/albums/xx190/Myter01/111_zps164b1c36.jpg
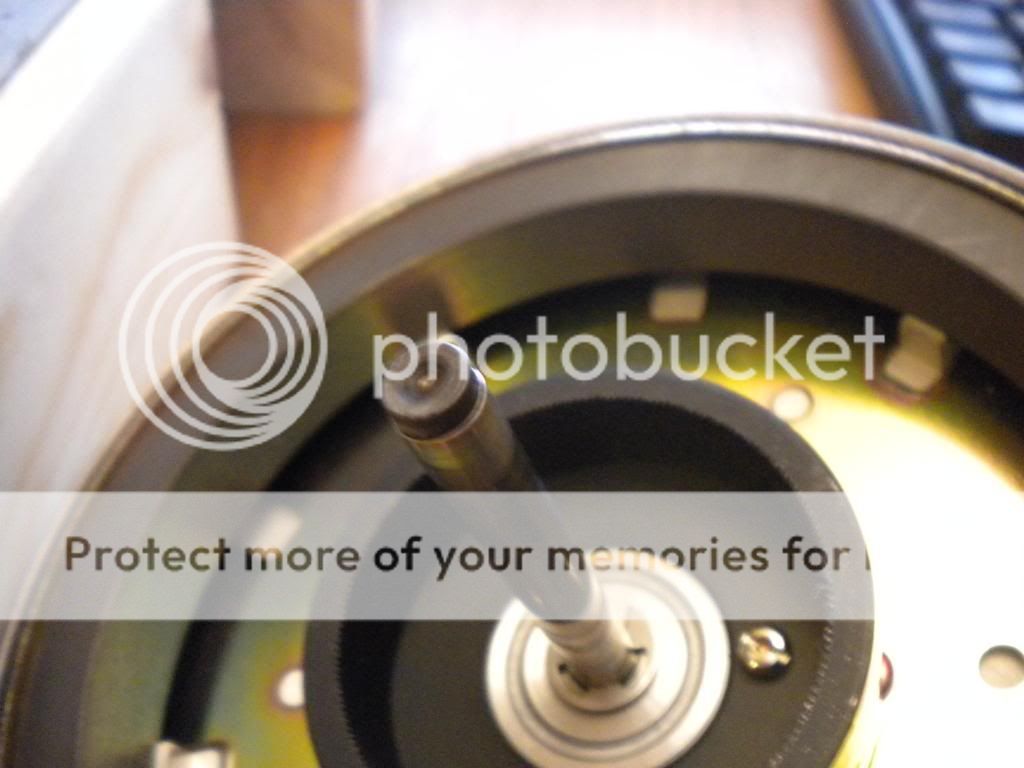
Hi Nils. Above I've referenced to the photo on photobucket. so far it seems to be coming through. So now we know you refer to the plastic thrust pad on the end tip of the platter bearing shaft. I have photos of mine with almost as much wear. This obviously needs to be renewed. But frankly I have not yet figured out how to remove this piece without breaking anything. It is high on my list and I will post to this thread when I have accomplished renewal of the thrust pad. Fwiw, the bearing ball (that takes this thrust) in my player shows no visible or measurable evidence of wear.
Stay tuned. We will figure this part of it out.
-Steve
Hi Steve.
The plastic thrust pad actually came off very easy. After cleaning the bearing shaft I noticed that the plastic pad turned on the metal shaft so I just tried very gently to pull it off. It came off with no force at all.
It would be great to have some input on the optimal thrust pad material for this application.
Also the exact original dimensions, would be interesting to get information about. I do not have proper tools to measure the pad, and years of wear means it probably lost some of its original thickness.
Regards
Nils
The plastic thrust pad actually came off very easy. After cleaning the bearing shaft I noticed that the plastic pad turned on the metal shaft so I just tried very gently to pull it off. It came off with no force at all.
It would be great to have some input on the optimal thrust pad material for this application.
Also the exact original dimensions, would be interesting to get information about. I do not have proper tools to measure the pad, and years of wear means it probably lost some of its original thickness.
Regards
Nils
Hi Steve.
The plastic thrust pad actually came off very easy. After cleaning the bearing shaft I noticed that the plastic pad turned on the metal shaft so I just tried very gently to pull it off. It came off with no force at all.
It would be great to have some input on the optimal thrust pad material for this application.
Also the exact original dimensions, would be interesting to get information about. I do not have proper tools to measure the pad, and years of wear means it probably lost some of its original thickness.
Regards
Nils
That's great news. I've been reluctant to apply force getting that part out because none of us, (except yourself, now) know what the hidden shape of that thrust pad is. for instance, we don't know if there isn't some sort of retainer function within. But I gather, by your above description, that there isn't. Any chance you can show a photo of the thrust pad after it has been removed?
-Steve
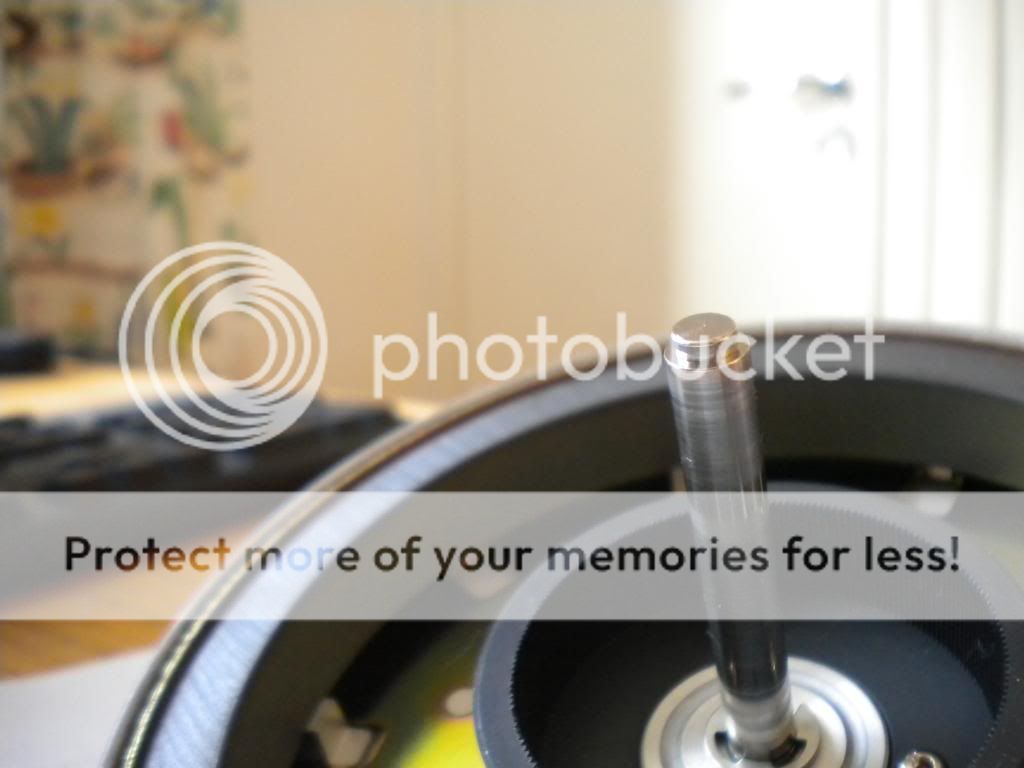
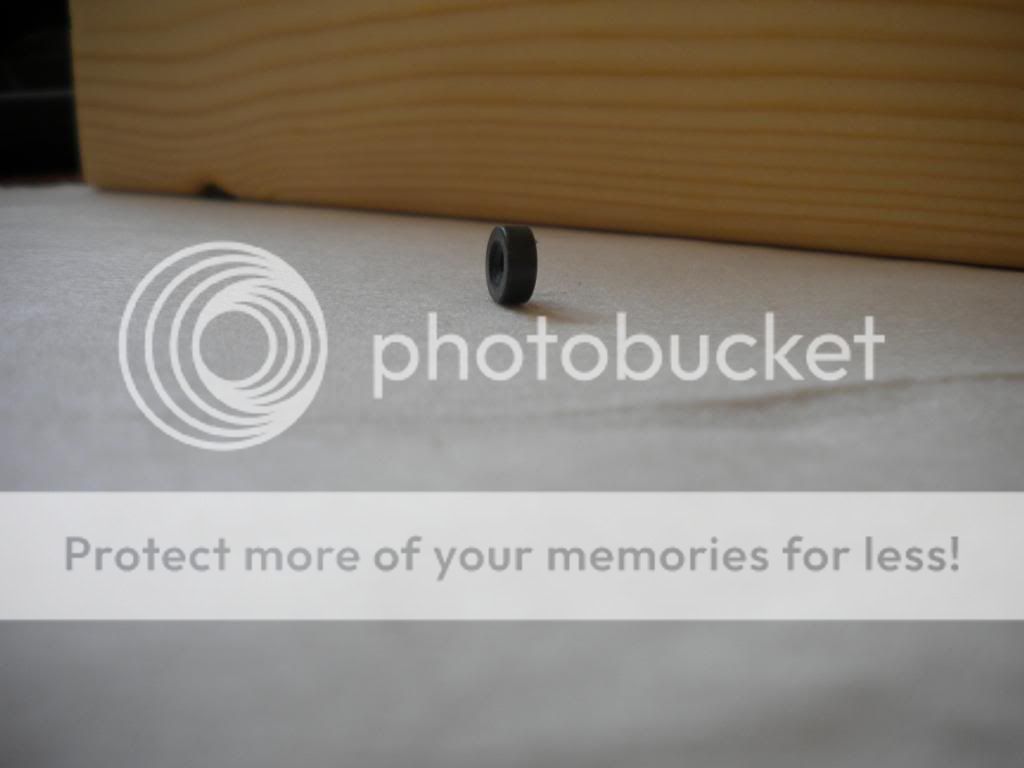
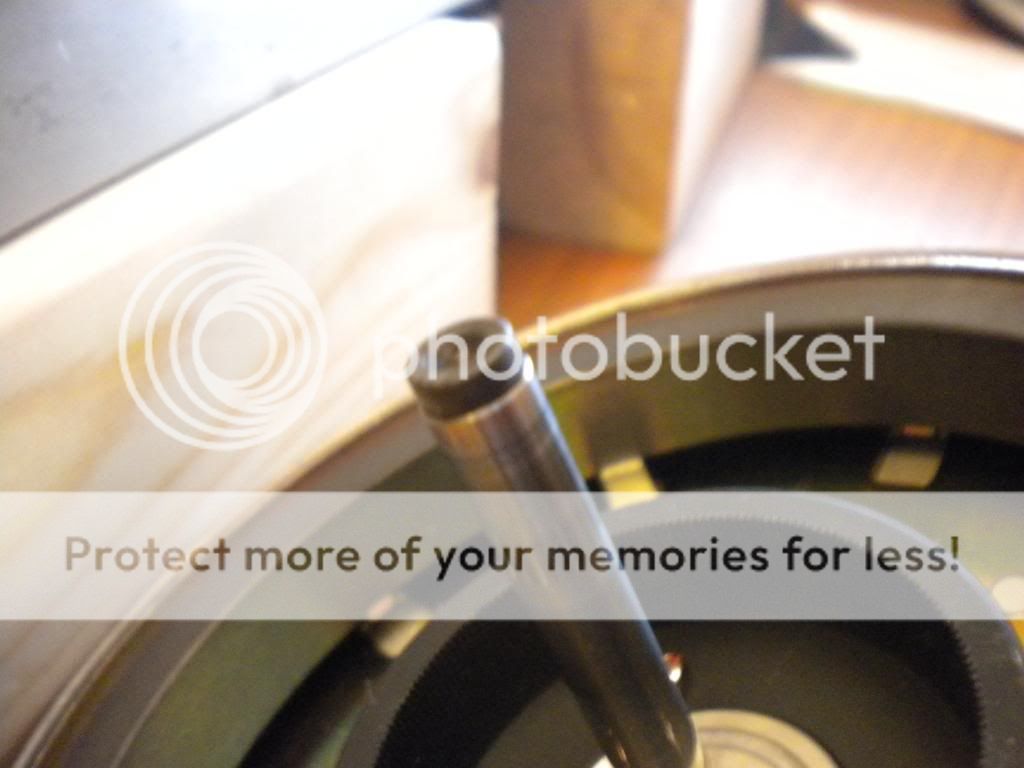
Quote:
Originally Posted by nilsW View Post
Hi Steve.
The plastic thrust pad actually came off very easy. After cleaning the bearing shaft I noticed that the plastic pad turned on the metal shaft so I just tried very gently to pull it off. It came off with no force at all.
It would be great to have some input on the optimal thrust pad material for this application.
Also the exact original dimensions, would be interesting to get information about. I do not have proper tools to measure the pad, and years of wear means it probably lost some of its original thickness.
Regards
Nils
That's great news. I've been reluctant to apply force getting that part out because none of us, (except yourself, now) know what the hidden shape of that thrust pad is. for instance, we don't know if there isn't some sort of retainer function within. But I gather, by your above description, that there isn't. Any chance you can show a photo of the thrust pad after it has been removed?
-Steve
I spoke too soon. Looking at the photo links you supply I found the photos I need. The pad actually fits like a cap. It looks safe to apply some force to remove the pad.
Those photos also indicate that your thrust pad is worn as far as it can go before breaking through the plastic and touching metal.
After I do some testing to my unit to gain some rumble and wow/flutter readings, for future reference, I will remove the pad on mine and get a close look at the dimensions of it. It appears like a part that would not be too tricky to machine.
re: different and more modern plastics that might be considered. Yeah. we can think about that. Probably the original material would be something like the Nylatron that was popular in the fifties and sixties. In my experience Nylatron wears longer than does Delrin. Teflon is too soft and wears through in short order. But now we have some "super plastics" like Torlon and Vespel to choose from. Both rather expensive. Perhaps some remnants can be found at a large discount
Thanks very much for sharing those photos. They tell me what I need to know.
-Steve
I made some additional photos, so you also can see the back side of the thrust pad ( or perhaps we should call it a thrust cap!)
Are you sure the bearing isn't supposed to ride on the center of the shaft in an oil bath?
Could it be the thrust pad is just there to center the ball?
I say this not knowing the answer, but Linn uses a metal to metal bearing.
I have not pulled mine out to look, (scared to look now!)
Rush
Are you sure the bearing isn't supposed to ride on the center of the shaft in an oil bath?
Could it be the thrust pad is just there to center the ball?
I say this not knowing the answer, but Linn uses a metal to metal bearing.
I have not pulled mine out to look, (scared to look now!)
Rush
Nil's thrust cap is worn through. But the one I have is not that far gone. Pic below is of my SP10 mkII bearing shaft just after disassembly and prior to any cleaning.

I think this photo indicates that the optimal condition would be a perfectly flat and square surface on the thrust cap business end. But with normal operation, and over time, a centered dimple wears into the thrust cap. And then eventually, if we don't replace it, the dimple will wear completely through. then you have the steel ball in direct contact with the steel bearing shaft. Not optimal for this design, imo.
-Steve
Steve your end cap seems to be in good shape! Would be interesting if you could get the dimension of your cap once you have done your testing ( I am also following that thread with great interest!)
I checked the service manual for the sp-10 from the Vinyl Engine to see if there is any information available there. Unfortunately the exploded view of the assembly does not show the actual bearing assembly. There is also a replacement part list but I have problems reading the small print.
Would anyone know if the thrust cap is listed as a separate part?
Also, has anyone ever tried to Contact Technics / Panasonic /Matsushita, to get some information? Perhaps they are happy to help with information like drawings, dimensions and material?
Regards
Nils
I checked the service manual for the sp-10 from the Vinyl Engine to see if there is any information available there. Unfortunately the exploded view of the assembly does not show the actual bearing assembly. There is also a replacement part list but I have problems reading the small print.
Would anyone know if the thrust cap is listed as a separate part?
Also, has anyone ever tried to Contact Technics / Panasonic /Matsushita, to get some information? Perhaps they are happy to help with information like drawings, dimensions and material?
Regards
Nils
- Status
- This old topic is closed. If you want to reopen this topic, contact a moderator using the "Report Post" button.
- Home
- Source & Line
- Analogue Source
- SP-10 mkII, the next project