Those rotary tools typically spin at 5000-20000 rpm.. for drilling aluminium you want a couple of hundred rpm and higher torque (and wd-40 or candle wax as lubricant)
If you have experience with drilling, you can use a handheld drill, otherwise you need a pedestal drill
This is what I use for drilling heatsinks. I can't drill a straight hole with is, the driller never stays vertical, holes are drilled a bit in diagonal. Also the driller doesn't really fit well, the colar seems a little too large for the stand.
Attachments
Last edited:
holes are drilled a bit in diagonal.
Make sure you are using good, sharp drills with plenty of lubrication (cutting fluid for aluminum).
I've had cheap or poorly-sharpened drills that wouldn't drill straight, so eliminate that possibility first.
Another 'trick' that works is to drill a vertical hole in a block of hardwood or metal (if you have a friend with a good drill press, or using your drill carefully) and then use that as a 'guide' to get your hole in the aluminum started.
Are you using a center punch to make a 'dimple' where you want to drill the hole?
It sounds like you could tighten up the attachment of your drill (motor) to the stand you have - cut some shims from an aluminum can (beer can?) for a start.
Used small bench mount drill presses can usually be found in classified adds like Kijiji, craigs list etc. Just make sure you get one big enough. Use it to drill the holes for your amp and then resell it if you don't want to keep it. You really want those holes to be straight and of consistent diameter if you are planning to tap them.
I've drilled all kinds of holes in HiFi200 casework and heatsinks with nothing more than a cordless 3/8" hand drill. As mentioned, it really helps to use sharp bits and some lubricant, although aluminum is extraordinarily soft. For accuracy you'll want to center-punch your position and create the proper angle, and maybe also use a centering bit for critical holes. For straight holes you can use a drill guide (google Big Gator for an example). Clamping the work is helpful. For really straight holes you'll need a drill press. With good technique and care a hand drill will take you a long way!
BK
BK
I've drilled all kinds of holes in HiFi200 casework and heatsinks with nothing more than a cordless 3/8" hand drill. As mentioned, it really helps to use sharp bits and some lubricant, although aluminum is extraordinarily soft. For accuracy you'll want to center-punch your position and create the proper angle, and maybe also use a centering bit for critical holes. For straight holes you can use a drill guide (google Big Gator for an example). Clamping the work is helpful. For really straight holes you'll need a drill press. With good technique and care a hand drill will take you a long way!
BK
Good tip about Big Gator. Thanks.
nash
A problem I have with the hand electric drill and the stand is that the colar of the electric drill is a bit large, I had to remove the plastic around the hole where the drill locks to make ir enter the hole. Even so it doesn't enter all the way. What if I buy another hand electric drill with a standard 43mm colar (about 40€) would that work? Will I be able to drill straight holes and tap the heatsink?
Other option would be buying a small drill press, the Proxxon TBM 200 looks small and nice. It's a bit expensive (about 200€), would that be a worthy investment? Or would the first option suffice?
I want to be able to drill and tap holes for mounting power transistors (M2.5 holes tapped to M3).
Other option would be buying a small drill press, the Proxxon TBM 200 looks small and nice. It's a bit expensive (about 200€), would that be a worthy investment? Or would the first option suffice?
I want to be able to drill and tap holes for mounting power transistors (M2.5 holes tapped to M3).
Last edited:
My advice:
-electric hand drill
-sharp bit correctly sized for Al
-center punch
-drill guide like Big Gator
-through-hole tap (to start)
-blind hole tap (to finish)
-good tap wrench like starret
-tapping block (the secret weapon)
-some practice
That will accomplish what you want. But a drill press is nice to have!
BK
-electric hand drill
-sharp bit correctly sized for Al
-center punch
-drill guide like Big Gator
-through-hole tap (to start)
-blind hole tap (to finish)
-good tap wrench like starret
-tapping block (the secret weapon)
-some practice
That will accomplish what you want. But a drill press is nice to have!
BK
Unfortunately HiFi2000 heatsinks don't allow for a nut on the other side. I have to drill and tap the aluminium.Hi. Just a thought, a nut and bolt is much easier than tapping holes and you'll be able to more thread strength steel to steel than steel to aluminium
My advice:
-electric hand drill
-sharp bit correctly sized for Al
-center punch
-drill guide like Big Gator
-through-hole tap (to start)
-blind hole tap (to finish)
-good tap wrench like starret
-tapping block (the secret weapon)
-some practice
That will accomplish what you want. But a drill press is nice to have!
BK
What's a through-hole tap and a blind hole tap? I only use one tap, M3 bit, like the smaller one in the picture.
What's a tapping block?
Attachments
A tapping block is nothing more than a block of steel or even aluminum with holes drilled into it that your tap just passes through. It guides the tap as you hold it down on the material. Tapping blocks should at a minimum be made on a decent drill press, best made on a Bridgeport type machine. I usually make them out of 1" thick stock, for tiny taps 1/2" would be fine.
Taps are an investment, if your going to be doing this for a hobby buy some quality taps. OSG is a good brand. For through holes use Spiral Point Taps and for blind holes use Spiral Point Plug Taps. They are run in without breaking the chips until your in deep enough. Use good quality cutting oil. Good taps will tap thousands of holes in all but the toughest of materials. Stainless steel as used in audio chassis is not tough material if proper tools are used. For drills I only use 135 degree split point cobalt drills. I have used a single 1/4" diameter drill like that to drill over 2000 holes in 1/4" thick 304 stainless steel and it was still going strong. It all comes down to speed, feed and coolant.
Those 4 flute taps shown above are very old school, I won't take them for free, not worth the aggravation when one breaks off in a part that I have several hours into. I only use them to chase an already tapped hole to clean it up. Or on holes 3/4" and up.
Make friends with a machinist and pick his brain. I've been doing this stuff (machining) for 45 years, love teaching my race car buddy's how to do stuff.
BillWojo
Taps are an investment, if your going to be doing this for a hobby buy some quality taps. OSG is a good brand. For through holes use Spiral Point Taps and for blind holes use Spiral Point Plug Taps. They are run in without breaking the chips until your in deep enough. Use good quality cutting oil. Good taps will tap thousands of holes in all but the toughest of materials. Stainless steel as used in audio chassis is not tough material if proper tools are used. For drills I only use 135 degree split point cobalt drills. I have used a single 1/4" diameter drill like that to drill over 2000 holes in 1/4" thick 304 stainless steel and it was still going strong. It all comes down to speed, feed and coolant.
Those 4 flute taps shown above are very old school, I won't take them for free, not worth the aggravation when one breaks off in a part that I have several hours into. I only use them to chase an already tapped hole to clean it up. Or on holes 3/4" and up.
Make friends with a machinist and pick his brain. I've been doing this stuff (machining) for 45 years, love teaching my race car buddy's how to do stuff.
BillWojo
Listen to BillWojo. 45 yrs experience shouldn't be ignored. I'm just a hack by comparison.
I use the OMW tapping block shown below. By using taps with different taper you can make threads all the way to the bottom of the hole (and still start the threads easily) so you get ALL that critical thread depth for good holding power when you later tighten down the bolt onto the device (and into soft aluminum!).
BK
I use the OMW tapping block shown below. By using taps with different taper you can make threads all the way to the bottom of the hole (and still start the threads easily) so you get ALL that critical thread depth for good holding power when you later tighten down the bolt onto the device (and into soft aluminum!).
BK
Attachments
That Proxxon (for me) is in the category of 'expensive toy drill'.Other option would be buying a small drill press, the Proxxon TBM 200 looks small and nice. It's a bit expensive (about 200€), would that be a worthy investment?
I'd look for a cheap Chinese small drill press if I couldn't find something on the used market locally.
Another thread recently discussed those 'drill stands' for handheld electric drills.
http://www.diyaudio.com/forums/equipment-tools/305355-cheep-cheep-drill-stand.html
Last edited:
What's a through-hole tap and a blind hole tap? I only use one tap, M3 bit, like the smaller one in the picture.
What's a tapping block?
A through hole tap is tapered at the end so that it makes it easy to start the threads. The blind hole tap is blunt on the end with full depth threads going as close to the end of the tap as possible. A blind hole is one that doesn't penetrate all the way through the material you are tapping. When tappin a heatsink you typically do not want the hole to penetrate all the way through to the fin side. So for HIFi 2000 heatsinks which have an 8mm base you need to drill a hole to maybe 7mm and then start the tap with the tapered through hole tap going in until it bottoms. This is another way a drill press is better than a hand held drill. You need a consistent depth which is difficult to do hand held. You then would back out the tap, clean out the partially tapped hole and use the blind hole tap to finish the threads. This way you can get more usable threads in your shallow 7mm deep hole. It's a time consuming job and you need to take your time and not force the tap. If it starts to get hard to turn the tap, back it out and clean tap and hole and start again. I use a soft brass bristle brush to clean my taps and use compressed air to clean out the tapped holes. Wear safety glasses when using compressed air to clean the holes. The air forces the al particles out of the hole and back at you.
I've never used a tapping block but it is a great idea. There is a certain amount of "mechanics feel" involved in doing this. You need to make sure that you don't put any force sideways on the tap. A large tap wrench and a small tap makes it easy to push down on one side of the wrench more than the other and break the tap. You also need to pay attention to the force required to turn the tap. When it starts to increase to the point where you can feel the tap flexing due to the torque, you need to back the tap out, clean and lube and start again. Go slow at first and look at some videos of tapping, which I'm sure must be out there on the web somewhere.
If you can find a used drill press, that is the way I would go. People often sell them just to get them out of the house. I've even found an almost new one on the side of the road on garbage pick up day. Much better than a hand held drill, especially for someone who has little experience with this sort of thing. You can always sell it again afterwards if you have no further use for it and get back most of your investment.
Last edited:
I see I have a lot to learn. Thank you for sharing your knowleadge. 
Whould this be a good buy? It cames with an UK plug but there are plug adapters for EU plugs, right?
PCB Art Jewleries Mini Bench Drill Press 6mm Chuck Fully Adjustable Speed | eBay
Whould this be a good buy? It cames with an UK plug but there are plug adapters for EU plugs, right?
PCB Art Jewleries Mini Bench Drill Press 6mm Chuck Fully Adjustable Speed | eBay
I see I have a lot to learn. Thank you for sharing your knowleadge.
Whould this be a good buy? It cames with an UK plug but there are plug adapters for EU plugs, right?
PCB Art Jewleries Mini Bench Drill Press 6mm Chuck Fully Adjustable Speed | eBay
In my opinion (IMO), it's not suitable for the job you want to do.
Maximum drill size in mild steel = 1/8" ...really????
That's another high speed (5000+ RPM) 'jewellery and model-making' drill press. Something like that might be OK for drilling holes in PCBs, but for drilling metal heatsinks and general shop use, you need something like this 22" high drill press as a minimum:
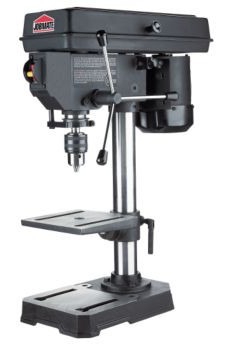
I have one just like that ($50 on sale, new, a few years ago, still under $100 on sale) and it works well on the bench-top when I don't want to go out to my garage where I have a larger floor-standing drill press.
- Status
- This old topic is closed. If you want to reopen this topic, contact a moderator using the "Report Post" button.
- Home
- Design & Build
- Equipment & Tools
- Drilling heatsinks - Proxxon 140/S any good?